|
Author |
Message |
Don_P
Member
|
# Posted: 8 Nov 2015 11:02pm
Reply
I was browsing old issues of Gustav Stickley's magazine "The Craftsman" from 1909 and came across this short article in the attached pic. The index to the old magazine copies is here, some dated but nice designs. http://digicoll.library.wisc.edu/cgi-bin/DLDecArts/DLDecArts-idx?type=browse&scope=DL DecArts.HomeDesign
|
|
Bret
Member
|
# Posted: 9 Nov 2015 08:34am
Reply
As Artie Lange once said "Very interesting". This is my favorite style of furniture. Clean lines made with quarter-sawn white oak.
You know the story of cobbler that didn't have time to make shoes for his own family, well that's my life when it comes to furniture. My dad and I started making antique reproductions in the 1975 and I've been fortunate to be working in custom woodworking ever since.
Last winter, I finally had time to make furniture for the house and cabin. Great fun making some things that the kids can have when when my wife and I are fertilizer. Bret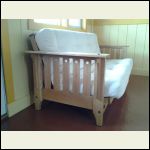 20150124_15.42.02..jpg
| 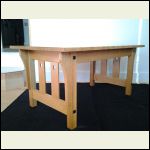 20150124_11.06.34_.jpg
|  |  |
|
|
Borrego
Member
|
# Posted: 9 Nov 2015 10:23am
Reply
Nice furniture, Bret! I have done some finish carpentry with quarter-sawn, mantels and such. It is such an unusual wood and looks so nice when finished! Out here in the San Diego area, there are a lot of old homes with this wood used for built-ins etc....
|
|
rmak
Member
|
# Posted: 9 Nov 2015 05:36pm
Reply
Thanks! That is news to me. I always thought that mission furniture was somehow connected to furniture of the arts and crafts movement in the late 1800's and early 1900's. A lot of that was boxy, using quarter sawn oak with square spindles. If you like mission furniture you might ask the google for some examples of arts and crafts furniture. It's really beautiful stuff.
|
|
adakseabee
Member
|
# Posted: 9 Nov 2015 09:29pm - Edited by: adakseabee
Reply
It's nice to see others on this forum who appreciate great furniture, and make it, too! Here are a few photos of side/night tables I made in the style of Charles and Henry Greene's Blacker House Side Table (they were contemporaries of Gustav Stickley) and my design of a barrister bookcase, all pieces made from quartersawn white oak with black walnut accents. The bookcase shelves are maple with amber shellac finish. All the oak and walnut are finished in dark walnut Danish oil and waxed.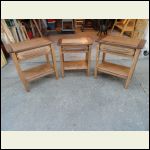 DSC05614.JPG
| 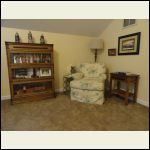 DSC05286.JPG
| 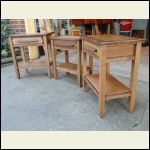 DSC05616.JPG
| 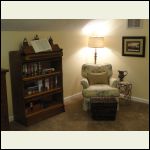 DSC04947.JPG
|
|
|
Don_P
Member
|
# Posted: 9 Nov 2015 09:51pm
Reply
I've mocked up a pine section for a barristers bookcase but couldn't come up with a good way to do the doors... what did you do?
What led to going back to find those magazines was a site visit to a 1920's Sears house in arts and crafts style that needs some TLC. I mentioned to the owners that it could have come from one of Stickley's planbooks. I sent them the link for rainy day reading and figured some of you would want to bookmark it as well.
|
|
adakseabee
Member
|
# Posted: 10 Nov 2015 12:03am - Edited by: adakseabee
Reply
Don, I use one short (about 1") length of 1/4" diameter brass rod stock (obtained from Graingers) inserted in the each stile about 1" down from the top of each door, that slides in a groove slightly wider than 1/4" as one pulls the bottom of the door out, then up and in. The door then rests on brass rod pivots, that are located about 3/16" behind the door (when it is closed) to the center point of the 1/4" rod and about 1/16" plus half the width of the door frame under the groove. The photographs should help. The first photo shows quartersawn white oak, except for the maple shelves. The remaining three is plain sawed red oak (my first attempt at this project using much cheaper lumber). Each shelf section, the top section, and the base section are easily separated and are held in position with a lock board attached to the bottom of each shelf box and bottom of the top section that fits into a slot in the top surface of the base section and top surface of the three shelf sections. For the three shelf sections the four sides are joined using half-blind hand-cut dovetails (I build these to last a very long time). The dovetails cannot be seen when the bookcase is assembled, but they are there nevertheless providing strength and rigidity to the entire assembly. Hope this helps. Adak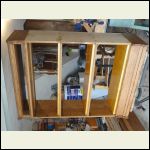 DSC04738.JPG
| 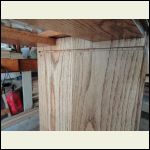 20130517_DSC02994..jpg
| 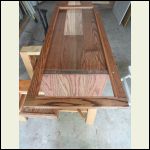 20130517_DSC02996..jpg
| 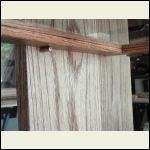 20130517_DSC02997..jpg
|
|
|
Don_P
Member
|
# Posted: 10 Nov 2015 12:39am
Reply
Thanks Adak, That's what I did in my mockup, it's quick and dirty so used dowels. One thing I learned on that was that sloppily I put the dowel on the door a little off center and the door, centering itself, didn't hang straight. I think in the final I'll probably off center the other way and let it rest closed with a little pressure. They'll be beech, I was in the beeches and glued up the panels awhile ago, another winter project.
|
|
adakseabee
Member
|
# Posted: 10 Nov 2015 04:25pm
Reply
Don, will you be making it in sections or one complete assembly? I'd be interested to see what it looks like with beech once you are done. Yes, the grooves and holes for the dowels / pins need to be precisely located.
By the way, did you know that Stickley furniture is still being manufactured? It is not cheap - meaning it's expensive, but well-made. Stickley has their factory in Syracuse, NY. The original factory was in Binghamton, NY, not far from my cabin. Adak
|
|
Don_P
Member
|
# Posted: 10 Nov 2015 06:42pm
Reply
I hope you're patient, but I looked at that corner of the shop the other day and I want it back. I planned to make them stack for ease of moving, beech is heavy enough as it is. It is a root suckering tree that forms a mat which then begins to choke out the other trees. I've been trying to eliminate them from one area where they took over and will restock it to oaks or hybrid chestnut. In medieval England a bodger would travel through the woods with his wagon and springpole lathe, thin the doghair thickets of beech and rough turn chair parts. They were stacked on his cart and taken to town for final drying and turning. I'll leave a considerable number of them in the surrounding area, the grouse prefer beechnuts. We did go through a round of beech bark disease but seem to have survived. Nice, extremely dense and strong, high drying losses but heats good. It is self polishing making good tool and textile parts. I've used planks to slide heavy timbers on, it quickly polishes up and makes sliding them around easy.
I knew Stickley was producing in the 80's when I was around furniture enough to keep up with the trade mags. I'm glad they made it through, Chinese furniture dumping decimated the industry down here. I saw a beautiful old Stickley bookcase for sale in a shop in IL on our travels years ago, the price was right and for some reason I passed on it, almost turned back around for an hour. Later I saw another gracing a hall in the Grove Park Inn, it felt pretty much like a dope slap to the back of the head.
|
|
rockies
Member
|
# Posted: 10 Nov 2015 08:22pm
Reply
One table I've always wanted to have was a Frank Lloyd Wright "Print Table". It was designed for one of his clients around the 1900's. It was featured on an episode of "This Old House" and it's interesting because the lattice leg panels swing out from the main body of the table to support the top, but when they are folded up against the vertical uprights the top folds up like a butterflies wings and slides down inside the central cavity. It could also be used half open to show off artwork. I've never seen a table where the top folded up and was stored that way.
By his own admission, Frank Lloyd Wright said that most of his furniture left him covered in bruises whenever he used it, but I thought this table was quite unusual and very beautiful.
It's funny that the reason for the "Mission" and "Craftsman" styles being created in the 19th century was to offer cheaper alternatives for housing and furniture (since it was all handmade instead of machine made) and now it's incredibly expensive to make or buy.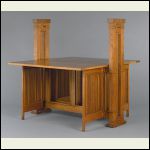 Table open
| 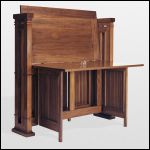 Half open
| 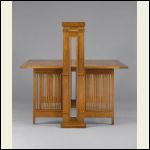 Side view
|  |
|
|
Borrego
Member
|
# Posted: 11 Nov 2015 10:40am
Reply
Really nice end tables, adak! Love that look....
here's a good article on the differences between the styles..http://www.arts-and-crafts-style.com/mission-style.html
Here's a fireplace surround/mantel I did, not with 1/4 sawn, but a similar style, all locked together like a puzzle...
|
|
Don_P
Member
|
# Posted: 11 Nov 2015 09:18pm - Edited by: Don_P
Reply
Good job.
I do enjoy Wright's houses and am a fan of his Usonian ethic. His furniture, well, not so much. I've heard that many clients had everyday furniture and only brought his out for show or when he was visiting. In his house sits a comfy chair on the ugliest blue shag throw rug over the live stone floor, I don't think he used his furniture either .
Attached are some pics inside a craftsman-ish timberframe that was fun.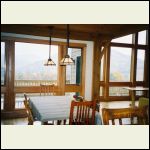 793046R1012_002.j.jpg
| 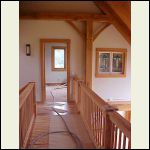 bridgerail2.jpg
| 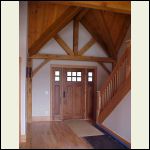 entrytrim.jpg
|  |
|
|
Don_P
Member
|
# Posted: 11 Nov 2015 11:26pm - Edited by: Don_P
Reply
We've talked about quartersawn lumber... the first pic below shows the difference between a quartersawn board, and where it comes from, from a flatsawn board. If you think about how the blade is slicing across the concentric growth rings it'll become clear why the boards look, and act, differently. White oak has very striking rays that are visible when quartersawn.
One problem when trying to show just quartersawn grain is what to do with something like a table leg, if truly quartersawn then 2 opposite faces will show rays, and the other opposite faces will be flatsawn. In the second pic look at the square in the center. Then look at about 2 o'clock. This is rift sawn, the grain on all faces is uniforlmly around 45 degrees to the face. Those parts have moderate ray flecking and the basic grain of quartersawn and no face looks flatsawn
|
|
DaveBell
Moderator
|
# Posted: 12 Nov 2015 01:25am
Reply
Quartersawn Fleck. See the picture True Quartersawn to get more fleck lumber out of a log. http://www.core77.com/posts/24891/how-logs-are-turned-into-boards-part-2-quartersawn- 24891
Wood grain figures:, Fleck, Flame, Tiger Stripe, Curly, Birds Eye, Burl, Knots, Crotch, color variations, etc. .
There are over nine species or more that can render nice Ray Fleck figure. Red and White oak have the most pronounced rays.
I found a piece of curly cherry 8'x1' at a mill outlet in NC for $4.00 a BF. Cheap! Had to have it.
I also found black walnut that had 3" white grain in the middle from a tree in VA. I made a box for my wife out of it where the white grain is on the top and spills over to the front.
Here are some pics of Burl on my WV place.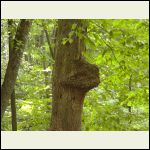 wvburl_053.JPG
| 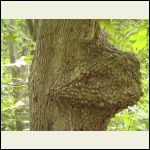 wvburl_054.JPG
|  |  |
|
|
adakseabee
Member
|
# Posted: 12 Nov 2015 07:43pm
Reply
Borrego, thank you for your comment about my side/night/end tables. It takes about 65 hours of labor to make one. Your fireplace looks like a modern take on one of Stickley's craftsman fireplaces. I like the nice simple lines of your woodwork.
Rockies, the Frank Lloyd Wright folding table is very interesting. I might modify that design to make a drafting table for my shop. Like Don indicated, shop space is at a premium and that folding table looks a good solution to save space.
Don, when I made the legs for the tables, I cut quartersawn white oak on my tablesaw with the blade inclined 45 degrees to cut both long edges of each of the four pieces for each leg. I then glued four pieces together so that the flecking shows on all four surfaces of each leg. In cross-section (viewed on the end) it looks like four triangles glued together with the long sides with the flecks facing out. It's a lot of extra work, but I believe that the result is worth that effort. And I hear you about beech being a root suckering tree. I have the same situation up the hill from my cabin in my grove of quaking aspen. As much as many folks consider them to be trash trees, to hear the wind blow through the leaves is very soothing and they provide a "nursery" environment for young oaks, maples, and white pines.
Dave, that's a great link you provided. Cherry, maple, walnut, oak, and pine are the only wood species I use for furniture. I guess I am partial to wood that grows where I grew up in NYS. I haven't used hickory, beech, or ash yet, but might in the future as they all grow on my NY property.
|
|
Don_P
Member
|
# Posted: 23 Nov 2015 11:05pm
Reply
I stumbled upon a neat youtube of a bodger at work; https://www.youtube.com/watch?v=KUv3OwY5Etg
|
|
|