|
Author |
Message |
EvoQ
Member
|
# Posted: 26 Dec 2012 05:33pm - Edited by: EvoQ
Reply
I get this newsletter and today took a look at the Free 12x24 Cabin plus Loft plans. I was impressed with the detail and overall design.
For some this might be what they need or at least give them a better idea of where to get started and even answer a few questions too.
Take a look at the Free 12 x 24 Cabin plus Loft Plans here
Hopefully those might be useful to some people here on the forums
And also here is the NewsLetter where the plans came from as they have other Free Plans there as well.
|
|
northernspirit
Member
|
# Posted: 7 Jan 2013 01:03pm
Reply
thanks for the link, i will most likely be using these plans when I build my cabin. my only question is why did they sink the 2X4 in the 2X6 walls down the length of the wall? would that really offer you that much more support to the wall? it looks like more work than its worth, but i'm no expert.
|
|
EvoQ
Member
|
# Posted: 7 Jan 2013 07:12pm
Reply
They put those separated pieces of 2x4 between each stud(s) up at 8 feet off the floor. That is used as what is called Blocking, which is what the 4x8 sheeting is screwed or nailed to at the very tops of that 4x8 sheeting. Does this make sense to you ? You need this blocking to have something to attach the sheeting to, otherwise there would be nothing there along the tops of the 4x8 sheets to screw or nail to. What you originally thought was bracing is not. Now if there is ever a call or need for bracing, which is called Wind braces they are added at a 45* degree angle from one wall corner to the next, in an X like fashion but with only 1 leg of the X not both. For such a short length wall no wind bracing is needed. However wind bracing is frequently used on longer exterior walls to add strength. I do like they call for 2x6's for the wall studs. They are much stronger and also give you an added 2 extra inches of insulating space for a total of 6 full inches of insulation. I hope you will consider the blown foam type insulation if your cabin will be in a very cold environment. The Blown Foam insulation is by far the best and in most cases hardly any heat source is need to maintain a steady comfortable heat inside the cabin. Great choice for plans, free is always best, Keep us posted..any more questions just ask.
|
|
MtnDon
Member
|
# Posted: 7 Jan 2013 10:14pm - Edited by: MtnDon
Reply
Quoting: northernspirit why did they sink the 2X4 in the 2X6 walls down the length of the wall?
Which 2x4 do you refer to? On what plan page?
I could be wrong but I think you may be referencing the 2x4 that is inset as shown on page 2 just under the loft floor joists. I attached an image with the piece circled in red. Is this what you wonder about?
If so that is a ledger board. It is inset into precisely cut notches to help support the loft joists. The joists rest on the board edge and are also face nailed to the wall stud.
The cuts are easiest made before the wall is framed. Clamp all the studs together on the floor. Mark and cut them as they lay there stacked together. Cut with a skilsaw and clean with a chisel or use guides and a hd router. Care must be taken in layout to try to avoid having the notch at a large knot or stud defect.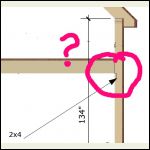 this 2x4 or some other one???
|  |  |  |
|
|
MtnDon
Member
|
# Posted: 7 Jan 2013 10:21pm - Edited by: MtnDon
Reply
Walls are best braced by sheathing the exterior walls with OSB sheets and then applying a weather resistant barrier and finally whatever finish cosemetic siding is desired. OSB sheathing is available in 4x9 and 4x10 sheets and can eliminate a lot of panel edge blocking. And the panels are best nailed rather than screwed... (unless you go to the expense of structural screws) 6D common (2" × 0.113") every 6 inches on the edges, 12 inch spacing in the field.
|
|
northernspirit
Member
|
# Posted: 8 Jan 2013 12:35am
Reply
thanks for your replies, MtnDon that is the spot I was talking about. but what EvoQ says about the blocking makes more sense to me only because the ledger as you say does not appear to stick out from the wall. how would this add a spot for the joists to rest if its flush with the wall?
|
|
MtnDon
Member
|
# Posted: 8 Jan 2013 12:55am
Reply
The joists extend into the wall cavity.
Assume the wall studs are a full 12 feet apart as measured on their outside edges/faces. The floor joists are a full 12 feet in length. It rests on the 2x4 inset ledger and extends over the wall stud right to the exterior sheathing. Then the joist is nailed through into the wall stud.
The ledger is inset as that makes a more solid support than simply replying on the nails to provide support. This can only be done with 2x6 studs not 2x4 wall studs. (In years gone by it was commonplace enough to find 1x4 or 1x6 inset into 2x4.)
The ledger is not meant to stick out from the wall as that would not be as strong and would present a problem when paneling, drywalling, etc the interior.
|
|
MtnDon
Member
|
# Posted: 8 Jan 2013 01:04am - Edited by: MtnDon
Reply
hope your studs are straighter than this.... 
If it was meant to be blocking it would be on the exterior face of the wall. Blocking is not inset; it is simply short lengths of 2x4 inserted horizontally between studs where necessary.
|
|
EvoQ
Member
|
# Posted: 8 Jan 2013 03:23am
Reply
It's hard to say/tell what the Questioner was referencing to without showing us on the plans. As MntDon has referred to the only other situation that might be an question to him is where the upper loft is supported by the 2x4 running horizontally nailed to the 2x6's. You need to think of the load from the loft and how this 2x4 supports this loft.
In a Counter Opinion I personally would Not use OSB for exterior Sheeting. While is more than adequate for a little more money I would use Hardy Board Sheets.
These Hardy Board 4x8 sheets are made up of Concrete rather than Pressed together Wood Chips. Eventually OSB will succumb to water infiltration. Water will not effect this Concrete board. Now these Hardy Board Sheets are heavy, one can support and carry them with experience but they are challenging, but the security that one gets from knowing that the sheeting will never rot is priceless.
And a side note the Hardy Board Sheeting is Fire Resistant, fires will not reek havoc on Hardy Board like it will on OSB with the wood and chemicals contained. I have personally tried to burn this Hardy Board and it just can not be done. The last small Building that built I bought Hardy Board Sheets.
One might also think of the harmful chemicals that these OSB sheets give off in a small confined space too. However; OSb is more than adequate and will give one years of service. But there are Better alternatives IMHO.
Either way, these are nice plans, especially for Free. And will help someone without much experience in framing.
|
|
MtnDon
Member
|
# Posted: 8 Jan 2013 10:30am - Edited by: MtnDon
Reply
Quoting: EvoQ You need to think of the load from the loft and how this 2x4 supports this loft.
On a 12 ft wide there is no worry about using an inset 2x4 in the 2x6. If the building was much wider or if the studs extended higher above the loft floor there are other factors that come into play and should be considered. On something this small, even though the inlet 2x4 ledger would not pass code inspection, I would not give it a second thought.
Quoting: EvoQ In a Counter Opinion I personally would Not use OSB for exterior Sheeting.
I would never use OSB as a single layer siding or sheathing. I think what I wrote was misunderstood. Note I was suggesting OSB as the structural sheathing, to be covered by another final choice of siding.
Quoting: MtnDon Walls are best braced by sheathing the exterior walls with OSB sheets and then applying a weather resistant barrier and finally whatever finish cosmetic siding is desired.
Hardi panels applied over the osb and weather resistant barrier makes for a fairly nice wall. But IMO Hardi Panels are not nearly as good as many other treatments. What I do not like about Hardi Panel is that it is fairly easy to crack an edge when nailing an edge. Then it looks like crap. That is not a condemnation of the product, just a thing to be aware of. Other panel materials are made with shiplapped edges, Hardi Panels are not. You have to leave a space between panels and then go back and caulk each seam. To me, that reliance on caulk is a downer. I've never met a caulk that was failure proof. And redoing caulk is a pita, IMO. I've installed Hardi Panel and am happy enough with the material on our shed. But I did the cabin in Hardi Plank.
The fire resistance is great and the lap siding looks great and is easy enough to install.
There are clearances from walks, decks, strairs, roofing and others that must be watched to preserve the hardi warranty. The edges can absorb moisture if placed too close to a deck surface for example. The material can then delaminate. I've seen that happen. As with any product it pays to read the manufacturers information well.
|
|
MtnDon
Member
|
# Posted: 8 Jan 2013 12:54pm
Reply
page 16 from plans detail joist ends and blocking
|
|
northernspirit
Member
|
# Posted: 8 Jan 2013 01:16pm
Reply
many thanks guys for the detailed explanation, I understand what ledger does now. for the exterior I was thinking about using the OSB than a weather barrier, and than finally putting vinyl siding on. I know vinyl kind of takes away from the remote cabin look but I scored all the vinyl siding from a house that was 30 X 70 for free, its a yellowish tan color which isn't too bad of a color, it shouldn't stick out too much in the woods.
|
|
northernspirit
Member
|
# Posted: 8 Jan 2013 01:20pm
Reply
oh i forgot to ask you MtnDon, you said the ledger wouldn't pass code, how could you make it pass code? would making it a 2 X 6 instead of a 2 X 4 allow it to pass code?
|
|
MtnDon
Member
|
# Posted: 8 Jan 2013 04:16pm - Edited by: MtnDon
Reply
I should have phrased tat more carefully. It is not the ledger, per se, that would not pass code; code does allow a 1x4 for that. But the installation of the ledger and floor joists as drawn in the plans causes an issue with the rafters. The necessary rafter tie no longer exists. It has been moved down the wall and can not be counted as a rafter tie anymore. Elimination of the rafter tie will permit roof loading to exert outward horizontal forces on the stud stubs (referred to as kneewalls).
If there was need to pass code an inspector might use his judgement, his authority and let this go on a small cabin. And he might not. Strictly speaking it would not meet code. On a small building with steeply pitched roof it probably would be okay; but no engineer I know would likely pass it as okay. On a larger building I know from conversations I've had, the engineers I know would not approve.
And someone is going to come along and say that there are thousands of buildings built like that, and they are correct. That does not make it a good design though. I simply point out potential problems and try to explain the theory or reasoning behind it. If there are permits, codes and inspections involved where the cabin is to be built it is than smart to go have a talk with the AHJ (Authority Having Jurisdiction) before planning much further. As the AHJ they do have the power to interpret things in a manner that may be passed.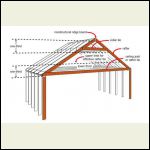 rafters and collar & rafter ties
|  |  |  |
|
|
northernspirit
Member
|
# Posted: 8 Jan 2013 05:19pm
Reply
out where i'm from we get 3-5 feet of snow on the ground sometimes in winter which is why i liked the idea of a 12/12 pitch roof. I don't like the idea of building something sub par. I want to know that when I leave the shed it will be still standing when i get back. If I add the collar ties to the roof is there anything else i could do without losing more head space in the loft and still have it to code? also i was planning a half loft not the full one in the plans, so for almost half the roof I can build it with proper rafter ties.
|
|
MtnDon
Member
|
# Posted: 8 Jan 2013 07:46pm
Reply
northernspirit, have a look at this snow load map. You have to scroll through some pages of text before the map comes up. Find the snow load in PSF for your location. Report back and we'll see what we have.
|
|
Rossman
|
# Posted: 8 Jan 2013 08:49pm
Reply
MtnDon: Thank you for the link to that PDF. I was looking for exactly that!
Wish the map was a bit more detailed though, looks like I am right on the edge of a 40/60 lb/sq.ft boundry, be nice to know which of those I'm dealing with.
|
|
MtnDon
Member
|
# Posted: 8 Jan 2013 09:38pm - Edited by: MtnDon
Reply
Quoting: Rossman looks like I am right on the edge of a 40/60 lb/sq.ft boundry, be nice to know which of those I'm dealing with.
That's when a call to the local bldg dept might help... or ya' go with 60... Sometimes more detailed is available online, but if you've been looking... 
There's yet another link,,, Scroll down just a little to get to snow load. That one has a list of cities, maybe one is nearby. ? But it is in Kg/sq meter. divide that by 4.88 to get PSF if your mind works like mine does.
|
|
northernspirit
Member
|
# Posted: 8 Jan 2013 09:46pm
Reply
according to the page 15 map, i would say i'm around 40 ib/sq/ft but lets just say 50 ibs to play it safe.
|
|
Rossman
|
# Posted: 8 Jan 2013 09:53pm
Reply
Quoting: MtnDon There's yet another link,,, Scroll down just a little to get to snow load. That one has a list of cities, maybe one is nearby. ? But it is in Kg/sq meter. divide that by 4.88 to get PSF if your mind works like mine does.
Thanks again MtnDon, closest in that list to me is Smiths Falls or Kemptville which are both 255 or 52lb/sq.ft. I guess I'll figure for 60!
Cheers!
|
|
MtnDon
Member
|
# Posted: 8 Jan 2013 10:32pm - Edited by: MtnDon
Reply
The snow maps indicate ground snow load. That is the figure used. Now, it may be correct that most of the time a steep pich roof will shed snow. However, I have seen even steep metal roofs that have had a large build up. Sometimes that occurs when there is a sleet that freezes to the roof and then collects snow. Or if the roof insulation is inadequate and the roof warms enough snow melts and runs down to the eve overhang where it freezes. That makes an ice dam and snow starts to collect as well.
Here's what my calculator produces.
First we assume the dread load, the roof materials weighs in at 10 PSF, though on a steep pitch the raters and all are longer and that weight can be 15 PSF. If we use the 10 psf DL and add 40 psf LL (live load, the snow) we have 50 PSF.
Bldg 12 ft wide, rafters 24" OC, 50 PSF total load. Each rafter will have a horizontal outward push of 300 pounds
With rafters 16" OC the rafter thrust is 200 pounds
24" OC and 60 pounds total roof load Each rafter has a thrust of 360 pounds
16" OC is a thrust of 240 pounds
With no rafter ties on the top of the wall that force is pushing out trying bend or break the wall studs where the loft floor rafters are mounted. If the 2x6 stud has a 2x4 notched into it at that point the 2x6 is actually barely more than a 2x4 at that point.
That's a lot of potential thrust and this is a narrow building. You can imagine what that might grow to in a 20 ft wide... up to 600 pounds...
Unfortunately collar ties do little if anything to prevent spreading of the bottom end of the rafters, the walls. Collar ties are simply too far up the rafter. Collar ties are meant to prevent high winds from peeling the roof apart at the peak. They also hold the roof together if in a high wind the gable end windows blow in. That is how roofs sometimes are weakened enough to then begin disintegrating under extreme wind conditions.
One solution involves actually making the kneewalls taller. That may sound counterproductive but wait... A rafter tie is acceptable in the lower third of the rafter triangle.
Raising the rafter tie that much would normally require making the rafters larger, but that plan already has the rafters way oversized as far as load needs. That's likely to permit better insulation. Good thing to have.
Now raise the rafter and rafter tie assembly enough to get the headroom wanted between the loft floor and the raised rafter tie. That is how high to make the kneewalls. It would probably be easiest at this point to simply frame the lower floor walls with standard 8 foot studs and place the joists right across the top plates. Install the subflooring and then platform build the kneewalls and install the rafters with the raised rafter ties.
The cabin will be taller, but the roof and frame will be stronger. However, no good deed goes without some consequence. In this case the extra height makes the building more tippy, more prone to high winds causing greater tipping forces. A more massive, more robust foundation with more metal ties would be best used.
That is one way to have a good solid building for the more sever winter conditions.
Another would be to forego the loft idea and build a larger main floor and use a common flat 8 foot ceiling. That was our choice. That also eliminates the issues with heat rising and making lofts hotter than downstairs.
With the loft at one end built as I describe the other open end could still be balloon framed. If the side walls are over ten feet in height in the open end another issue arises though. Walls should not be higher than 10 feet without some side force bracing... But that also depends on how many feet of open cathedral ceiling there is... beams across the width at 9 to 10 feet height is one way. You might only need one, maybe 2 depending on the length of the cathedral ceiling area. There are some other techniques such as what amounts to a beam laid flat 8 to 10 feet up the high wall to resist sideways wind forces.
If you can figure out how much kneewall height would work to give you more upper space that would help me as I have a ton of other things I should be doing. Just picked up 5 new windows I'm changing out here at home, adding foam insulation, new siding....
|
|
northernspirit
Member
|
# Posted: 8 Jan 2013 10:40pm
Reply
Quoting: northernspirit according to the page 15 map, i would say i'm around 40 ib/sq/ft but lets just say 50 ibs to play it safe.
according to the other map i'm closer to 70 ibs. however the closest city was a few hours away. Thats quite the difference between maps.
|
|
MtnDon
Member
|
# Posted: 8 Jan 2013 10:42pm
Reply
Just FYI... a 15 pound load, mainly the weight of the roof materials comes out with a 90 pound thrust on 24: centers.
I just realized that with 2x10 for raters the DL may be as high as 20 PSF
20 PSF load = 120 pounds thrust
|
|
northernspirit
Member
|
# Posted: 9 Jan 2013 01:00am
Reply
Thank you MtnDon for your time, and your expertise it has already helped me greatly. 
Quoting: MtnDon If you can figure out how much kneewall height would work to give you more upper space that would help me as I have a ton of other things I should be doing. Just picked up 5 new windows I'm changing out here at home, adding foam insulation, new siding....
my guess is about 5 feet for height min, but honestly this is my first time building a shed I figured it out and I can get by with a 12X20 if I had too. yes it would be a tight fit for the 4 of us in my family but it would save me a lot in material costs, and it would be easier for me to build it. How often would we really be spending the whole day inside the place anyways.
I guess without the loft and the need for head room, would you still recommend a 12/12 pitch for the roof? in 70 ibs conditions?
my other concern now if you could call it that is I was planning to build a 12' long X 8' wide sized deck down the 20' length of the shed which I was planning to fully inclose with bug screen. with the terrain the deck placed there works best, however without the height of the original walls it will be harder to get a good pitch on the roof for the deck unless i make another 12/12 pitched roof coming 90 degree off the main roof like a "T" if that makes sense. is that what you would recommend?
|
|
ShabinNo5
Member
|
# Posted: 9 Jan 2013 05:57am
Reply
northernspirt
The shabin is very similar in design. In our case the footprint is roughly 11 x 20. We have a 6 foot deck that wraps three sides. Our location is two miles inland from Lake Superior (snow depth range 2-4 feet). The roof over the deck has a pitch of 17 degress (approx 4x12). We chose to build will all rafters being 16" on center. The rafter material is 2x8.
The drawing is from the original plan. Due to our terrain and a 25' hight limit, I adjusted the planned 8' ceiling to 7.5' on the mail level and also shaved 6 inches from the loft knee wall. Long story short, the total hight from the main floor to the top of the knee wall is within 1" of the free plan. You will notice in the photo that the lower roof is still separte from the upper roof just closer than indicate on the drawing. Also I extented the lower roof 24 inches past the deck edge (similar to what you would need for an 8' deck).
One of the projects this summer is to finish the roof over the deck.
Steve Shabin_No_5__Beginn.jpg
| 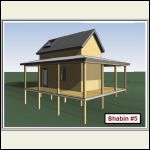 Shabin_No_5.jpg
|  |  |
|
|
MtnDon
Member
|
# Posted: 9 Jan 2013 10:34am
Reply
If you built w/o a loft the roof pitch can be just about anything you like the looks of down to about a 4/12 or 5/12. On a 12 ft wide 2x6 (2x6 #2 common species, 16" OC) rafters will support over 100 pounds of total roof load. That is with rafter ties across the wall tops (2x6 #2 common species, 16" OC). The joint where each rafter and ceiling joist connects should have 5 - 16D common nails on a 5/12 pitch, 6 nails on a 4/12 pitch, 4 nails on a 7/12 pitch. They will penetrate and protrude and can be clinched over for a strong connection.
I like the looks of a 12/12 pitch roof. I also totally dislike even the thought of working on one. Others don't mind working on that steep a slope as much... that's just me. Looks are important too; a big part of what and why we build. I just dislike the danger of steeper pitches. My personal comfort level is 6/12 for shingles and 4/12 or maybe 5/12 for metal. If there is a chimney to be cleaned keep that in mind.
|
|
northernspirit
Member
|
# Posted: 9 Jan 2013 03:59pm
Reply
after a bit of thinking and taking with the wife, we have decided it will be better to go without the loft. we'll plan to have 8' walls, and a 6/12 pitch roof made with 2X6's with collar ties and rafter ties, as shown in your rafter picture. most likely i'll be using a metal roof on top of the roof sheathing and felt. about the middle down the length of the shed we're planning to extend the roof further out another 4' past the wall to allow for a small deck approx 10'X4' with the front door in the middle of the deck/shed. the shed will be sitting about 2' off the ground built the same way as in the plans. I will have to lower the added deck about a 1' to make the over hang work for the roof and still have about 7' ceiling height for the deck.
I will plan to put another 2 posts on each of the deck corners to support the roof better with a 2X10 laminated beam (X2) sitting across the top of the two posts for support . will this be enough to support the extended roof in this area?
|
|
ShabinNo5
Member
|
# Posted: 9 Jan 2013 05:35pm
Reply
Another option to consider is to raise the wall hight in the building from 8' to 9 or 10'. Then you would not have to lower the deck to insure a roof height of 7' or more.
This would also provide options for more storage with upper cabinets or shelves inside.
|
|
Anonymouse
|
# Posted: 24 Mar 2013 08:51pm
Reply
Couldn't you solve the problem with lateral forces from the rafter on the knee wall with a simple knee brace connecting the top of the knee wall/rafter with the floor joist, like so?
/ + |\ |.\ +-+--
Anonymouse
|
|
ak_flyer
Member
|
# Posted: 17 Jun 2014 03:55pm
Reply
So as for the original plans, were they determined to be good design as is with no changes?
|
|
|