|
Author |
Message |
stubborn
Member
|
# Posted: 9 Apr 2018 09:18pm
Reply
Hello,
Been reading up alot and searched - but have yet to see / find an answer - hoping I am not going to repeat a question.
I will be building a 12x16 cabin in north east ontario canada ... so frost happens. I cannot pour concrete for footings (too remote to get enough water etc), so will be using some combination of patio blocks / pre-cast piers and gravel. I also need (permit) to anchor to resist wind etc.
So ... what wins / how does this all need to work ... frost will push up ... anchors hold down ... will this just tear it all apart ... or will enough anchors resist the frost and prevent heave .... ?
Feedback? other suggestions? I hear people doing this ... but the forces are at odds and it just does not seem to add up
|
|
ICC
Member
|
# Posted: 10 Apr 2018 09:57am
Reply
Nature wins in the end, most of the time when comes to things like frost heave. Just like for rain; water always wins.
|
|
rockies
Member
|
# Posted: 10 Apr 2018 07:05pm
Reply
If you're going to be experiencing frost heave you should look at this foundation system developed for the high artic, where most of the soil is subjected to permafrost. It might cost a bit more, but there's no digging, concrete, rebar, forms, tubes, etc. You could put it together yourself in about a day and then start building.
http://multipoint-foundations.com/
|
|
stubborn
Member
|
# Posted: 10 Apr 2018 10:32pm
Reply
Thank you for the info so far
Next / related question ... are people who build on skids anchoring? If so how?
|
|
socceronly
Member
|
# Posted: 11 Apr 2018 05:45pm
Reply
Oh, wow. Those are really neat.
I like the pic of the one stacked on the other....ha
|
|
rockies
Member
|
# Posted: 11 Apr 2018 07:30pm
Reply
I find skids to be a fine solution for a temporary building. A seasonal fishing shack or something. If you're planning on handing the cabin down to a future generation then a more substantial foundation is necessary.
Don't base your structural decisions primarily on cost. Upgrading later when it comes to structure is very difficult and expensive, while upgrading interior finishes is usually much easier (and can be down DIY over time). Invest in the best structure you can now.
|
|
NorthRick
Member
|
# Posted: 13 Apr 2018 06:13pm
Reply
Quoting: rockies If you're going to be experiencing frost heave you should look at this foundation system developed for the high artic, where most of the soil is subjected to permafrost. It might cost a bit more, but there's no digging, concrete, rebar, forms, tubes, etc. You could put it together yourself in about a day and then start building.http://multipoint-foundations.com/
That isn't going to solve the problem he is worried about. Sounds like he is being required to anchor the building so it doesn't blow away. Ground freezes (and expands if there is enough moisture and fines in the soil) from the top down. The surface of the ground will rise (again, if the soil is frost susceptible) lifting a cabin resting on the surface, while the anchor several feet down will not.
I'd build the cabin with several feet of overhang on the roof and make sure drainage is away from the cabin. It's water in the soil that expands when it freezes. No water, no expansion. Completely eliminating moisture is near impossible but you can minimize it to where it doesn't cause problems.
The other thing would be to make the connections between the cabin and the anchors have some flex in them. The third idea would be to disconnect the anchors after the inspector leaves unless you are building in an exposed area that is prone to high winds. Our 12x16 cabin sits on patio blocks with no anchors and has been through several storms strong enough to take down a lot of trees in the area without any problems with the cabin.
|
|
stubborn
Member
|
# Posted: 13 Apr 2018 07:41pm
Reply
NorthRick
Thank you - you are exactly correct. Greatly appreciate the feedback.
My current plans have a large overhang front and back - and about a foot on the sides. Also have a detached patio on one side that I will hide some flashing under to direct water away. Will see how easy to expand the side overhang out a bit - but also start thinking of ways to keep water away - tucking my piers under the cabin a bit more and covering the area around them seems pretty straight forward. May build a firewood ‘awning’ on the only real exposed side and use that to keep water 2ft away from the foundations ... hmmm ideas coming.
|
|
KinAlberta
Member
|
# Posted: 14 Apr 2018 12:37am - Edited by: KinAlberta
Reply
Maybe slope and slightly trench the ground around the cabin, lay in a membrane or plastic and gravel over it. You create a nice firebreak and ensure that the perimeter is as close to the centre in terms of ground moisture.
Our two cabins (24x30 & 24x24) are both on bocks. They were built in the 1950s and we’re the second generation owners. They both need a bit of work but could easily survive for several more generations. Decades of storms and high winds have had zero impact.
|
|
Gary O
Member
|
# Posted: 14 Apr 2018 01:02am
Reply
Quoting: NorthRick I'd build the cabin with several feet of overhang on the roof and make sure drainage is away from the cabin. It's water in the soil that expands when it freezes. No water, no expansion. Completely eliminating moisture is near impossible but you can minimize it to where it doesn't cause problems.The other thing would be to make the connections between the cabin and the anchors have some flex in them. The third idea would be to disconnect the anchors after the inspector leaves unless you are building in an exposed area that is prone to high winds. Our 12x16 cabin sits on patio blocks with no anchors and has been through several storms strong enough to take down a lot of trees in the area without any problems with the cabin.
that post is gold
we're on skids on blocks the key has been a solid overbuilt floor strongly secured to the walls, one unit, tied together generous eaves
The first cabin is ten years old...no signs of weakness, tweaking
|
|
NorthwoodsGuy
Member
|
# Posted: 14 Apr 2018 01:25pm
Reply
We also have a 12x16 on skids. Where we are, there isn't much topsoil, and the soil there is is very rocky clay. It is generally 12" or so down to bedrock, so there isn't a lot of soil to heave. So far, we have seen some movement, but it has been in half inches or so. Most folks in our area who are on skids jut throw a level on the floor and take a jack to the cabin if it isn't level in the spring. But soil conditions might be different where you are.
|
|
KinAlberta
Member
|
# Posted: 14 Apr 2018 10:46pm - Edited by: KinAlberta
Reply
You neither want to end up with a situation like this, nor want to deal with it this way. (I see a few safety issues here.)
Jacking up a cottage - YouTube https://www.youtube.com/watch?v=HcOcdezGkEI
Getting off topic again, here’s my thinking on a couple things:
So the ground may suffer from some movement but as long as the cabin doesn’t bend and twist little damage could be done. Beam strength goes up dramatically with vertical depth (such as from a 2x8 to a 2x10). Look at the numbers and you can see where a wall at 8’ height could potentially be very, very stiff (walls, like shear walls could really add strength and so any mild heaving might just lift the structure but not appreciably bend or twist or damage the structure.
Basically a bit of overbuilding could go a long way when just using blocks.
Using plywood in built-up beams - Fine Homebuilding “If you use four 2x10s and no plywood, the relative stiffness is 18% more than three 2x10s with plywood spacers. Make the beam from a pair of 2x12s only, and you get 5% more stiffness than three 2x10s with plywood. Three 2x12s yields 65% more stiffness. ...†http://www.finehomebuilding.com/1995/01/01/using-plywood-in-built-up-beams
Best source of span tables - irregular framing - JLC-Online Forums “You mention 2x6's...is that a mis type? As an example 2 2x6 is equivalent to a 4x6. I went through the calc's last month with a stress eng. and noticed that 2 2x6 is not as stiff(strong) as a 2x8. It is all about the height of the beam for stiffness. I used some 2x6's on 12" centers for a cabin (no building rules) because that was the material available, and it worked out fine. My floor ended up about 2+ inches thick though. I think it is a bad idea to cheat on the height especially with 2x6. My span was 11 1/2 ft. “ http://forums.jlconline.com/forums/forum/jlc-online-expert-forums/rough-framing/42397 -best-source-of-span-tables-irregular-framing bolding mine
Has anyone ever seen a span table for old ACTUAL dimension floor joists? | GreenBuildingAdvisor.com My results are as follows. A nominal 2x10 (1.5x9.25) deflects .009 inches under a 300 kg centered point load with both ends of the beam fixed in all directions. An actual 2x10 (2x10) deflects .0064 under the same loading conditions. .0064/.009 = approx 71% Thus, the modern, smaller, nominal "2x10" is approximately 71% as stiff as an actual 2x10 of the same material. Invert this and you have that the real 2x10 is approximately 140% as stiff as the smaller beam. I hope this helps all. ANSWERED BY NICK MCALPIN Posted Jul 9, 2015 8:47 AM ET 3. This rough-sawn lumber span table comes from The Visual Handbook of Building and Remodeling by Charlie Wing. It's been published by several publishing houses, including The Taunton Press. My version was printed by Rodale Press in 1990. ...†http://www.greenbuildingadvisor.com/community/forum/gba-pro-help/13426/has-anyone-eve r-seen-span-table-old-actual-dimension-floor-joists
|
|
FatGans
Member
|
# Posted: 27 Apr 2018 11:15pm - Edited by: FatGans
Reply
I built the foundation for my 12x14 shed with deck blocks and adjustable deck supports. I'm located in QC so the winter is really cold here. It was -27C for 3 weeks this year. The wind also is pretty strong here, sometimes up to 90 km/hr. The shed was built 5 years ago and stays in the same place and still strong. https://plasticinehouse.com/how-to-build-slanted-roof-style-shed-guide/

|
|
Ken Robbins
Member
|
# Posted: 28 Apr 2018 07:12pm
Reply
I used these helical posts with Teflon sleeves to allow ground heave to slide up the galvanized pipes. I couldn't be happier with the install and results, this was on the Kenai Peninsula, AK. They might be available in your area and they can get the machine anywhere a boat or helicopter can get to. I couldn't find anything that was close to the cost to get the job done, they weld on extensions as needed.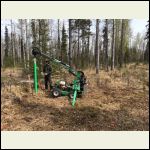 Tempo_posts.png
| 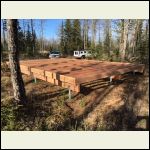 stringers.png
|  |  |
|
|
|