. 1 . 2 . >> |
Author |
Message |
caducus
Member
|
# Posted: 23 Feb 2018 01:15pm
Reply
Can anyone comment on the layout of this frame, foundation and the girder size?
It's a 14x20 cabin. Loft on one side. My plan was to use PT girders. Where they are extending out is to support a porch.
The 3 rows are spaced 8'10" apart. The spacing of the piers under the cabin on each girder are 5 and a half feet apart.
My plan was to use 2x8s for the joists. Not sure what the girders require or how this spacing and layout looks.
Edit: A little more info. This is temperate climate. No frost. No snow. The soil isn't great. Clay on top of sandstone mostly. I was intending to do sonotube, but I was also considering using larger precast footings (24" wide) that would sit mostly above grade. Thoughts on any of that?
|
|
UsandThem
Member
|
# Posted: 23 Feb 2018 02:44pm - Edited by: UsandThem
Reply
This may help: http://www.awc.org/codes-standards/calculators-software/spancalc
That span calculator should help you with the sizes. I don't see any concerns with the spacing. While the 2x8 will easily cover this distance, you may want to go with 2x10's since they are only about $1.50 more per board (at least at the 8' mark). This would add extra strength and less vibration for minimal cost. Again, the 2x8's should be fine, just a thought.
As for the girders, what size are you thinking? Have you considered using build your own LVL? 2x10 or 2x12 and sandwich 1/2 plywood with waterproof adhesive (and nails to hold it all together) in between to get a 5.5 width beam. You can get some triple plated post connectors to attach it all together. Those would be plenty strong.
While you mention no snow or frost, I'm assuming you do get rain. If that is the case, you will want all of what you are proposing to be pressure treated wood. I have ready anything less than 18" off the ground you want to be pressure treated as the ground will give off water vapor under your cabin. You don't want rot/mold.
If your soil is relatively soft, you will want as much surface area to spread the load as possible. If you do go with sonotube, you may want to go fairly large vs the smaller 6 or 8" sizes.
Again, YMMV, my personal mantra is, "anything worth engineering is worth over engineering" assuming the cost doesn't change significantly.
|
|
caducus
Member
|
# Posted: 23 Feb 2018 04:51pm
Reply
I hadn't considered girder dimensions. 4x10 PT seemed fine.
Girders will be PT. But the joists will be 18"+ off the ground, so I'm not worried about them.
I could build my own girders. Though I was thinking I'd avoid it by going with the 4x10.
|
|
ICC
Member
|
# Posted: 23 Feb 2018 05:23pm
Reply
I would suggest if you are in a no frost zone, you would be better off building on a full perimeter concrete foundation. When frost is no issue you can dig down 12 inches and lay a poured concrete footing with lengths of rebar running the lengths. 12" wide x 6" thick with the rebar held in the center, would do for a simple 1 story cabin. A rototiller can be used to that depth, in a few passes, to break up the soil and make the digging easier. Such a concrete footing spreads the loads out and it tied together by the rebar, whereas individual piers remain as individual piers and are free to move independently as soil moisture levels change. My only caveat about that is the clay. I would check with local builders about what has been proven to work best.
Girders, even PT ones should not be exposed to the elements as those ends under the porch would be. They can draw water under the cabin floor and cause joists to rot unless the joists are also PT. In geberal the girder and joist layout as drawn should be avoided in the interest of longevity.
Use a perimeter footer, lay blocks on that and build up to a decent height crawl space. You will be glad to have 24" minimum when you have to crawl under there for something in the future.
You could also investigate building a PWF, Permanemt Wood Foundation. That avoids all concrete but would still have a trench dug down with power compacted gravel in the bottom. Foundation Grade PT wood would be used, that's treated to a higher chemical level than regular lumber store PT. You'd build a short crawlspace wall on a PT 2x laid flat in the trench, place the floor joists on that and build upwards like usual.
Porches are usually best built as a separate addon BUT with proper planning for that. proper foundation for the porch, properly tied into the home or cabin structure and planned with a roof of sufficient pitch. Porches and decks often end up receiving higher loads than the main structure, like having a BBQ party and it rains and 25 people end up gathered on the porch or deck. Porches also end up being closed in as another room at times and a better foundation that piers is needed.
|
|
caducus
Member
|
# Posted: 23 Feb 2018 07:09pm
Reply
Appreciate the feedback. A full foundation isn't possible. Where this cabin is situated, everything is being moved in by hand. No equipment. And we're looking to pour a minimal amount of concrete. If I'm picturing the above foundation correctly, that's a fair amount of concrete to haul in.
Interesting thoughts about the wood foundation. And good point about the girders being exposed.
|
|
Just
Member
|
# Posted: 23 Feb 2018 07:15pm
Reply
if we’re mine I would use 2. 20 ft. Girders and 2x10 x14 joists then you have no piers under the cabin . You can adjust things if need be
|
|
caducus
Member
|
# Posted: 23 Feb 2018 07:22pm
Reply
you'd run the girders joists in the other direction then?
|
|
toyota_mdt_tech
Member
|
# Posted: 23 Feb 2018 08:06pm
Reply
My 2 cents, I would avoid the cantilever or if you must, keep it as small as possible.
|
|
UsandThem
Member
|
# Posted: 23 Feb 2018 08:38pm
Reply
I'd echo Toyota on this one. I would try to put as much of the weight as possible directly over the support areas.
|
|
Just
Member
|
# Posted: 23 Feb 2018 09:13pm
Reply
Yes i would use 5 piers on each side and a double joist on each end .
|
|
Just
Member
|
# Posted: 23 Feb 2018 09:20pm
Reply
What style of roof ? Do you need any interior supports for the roof?
|
|
Just
Member
|
# Posted: 23 Feb 2018 09:21pm
Reply
What style of roof ? Do you need any interior supports for the roof?
|
|
caducus
Member
|
# Posted: 24 Feb 2018 12:51am
Reply
Can you clarify what you mean by double joist on each end?
Shed roof 4/12. rafters spanning the 14 foot section. No interior supports.
|
|
Just
Member
|
# Posted: 24 Feb 2018 09:23am
Reply
Put two sistered joist under the two 14 ft. Walls to help support the span. Or you could support the 14 ft. Walls with two extra piers .
|
|
caducus
Member
|
# Posted: 25 Feb 2018 11:15am
Reply
Ah, got it. I like the idea of running the girders down the 20 foot length with the joists spanning the 14 feet. Doing that with 5 piers it seems that a 4x8 beam would be more than enough for the girders. With 5 piers on each side, that's like 4.5 feet between piers and span tables say that a 4x8 beam is good for 6 feet. Any reason you'd disagree?
|
|
Just
Member
|
# Posted: 25 Feb 2018 12:25pm
Reply
If you make the girders from 2x8s they will only be 3x7.5 . What are you using for piers??.
|
|
caducus
Member
|
# Posted: 25 Feb 2018 02:20pm
Reply
I'd buy two 4x8 beams, 20 feet long. Those are 3.5x7.25 inches each. A little bigger than building one out of two 2x8s. Piers are sonotubes. Not sure how wide yet, but ideally pretty wide.
|
|
ICC
Member
|
# Posted: 25 Feb 2018 03:45pm
Reply
What span tables are you using for the beam sizing?
|
|
snobdds
Member
|
# Posted: 25 Feb 2018 08:06pm
Reply
I made beams from 4, 2x12x20 glued and bolted together for the load bearing walls. Then the center got a beam of 3, 2x12x20. This on a 20x22 cabin. Remember that 2, 2x8, are stronger than 1, 4x8. The opposing wood grains and the laminating process make it stronger.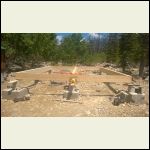 WP_20160702_001.jpg
| 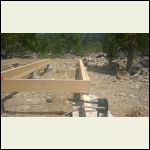 WP_20160702_002.jpg
|  |  |
|
|
caducus
Member
|
# Posted: 25 Feb 2018 09:53pm
Reply
no one specific span table. Just googling around. Is there one that's more reputed? They all seem to say more or less the same things.
On that 2x12 frame, you're not resting that on any girders I take it?
|
|
caducus
Member
|
# Posted: 25 Feb 2018 09:59pm
Reply
Here's a revised drawing. 14x20' cabin.
4x8 pressure treated girders on 12" sonotube footings spaced 55" apart. The frame is 2x10s, doubled up on the perimeter. Non pressure treated, but it'll be over 18" above grade.
Joists are spaced 16", overhanging the girders by a foot.
Thoughts?
|
|
Just
Member
|
# Posted: 26 Feb 2018 09:43am
Reply
I would over hang the girders by 1 in. Just enough to keep them dry .
|
|
toyota_mdt_tech
Member
|
# Posted: 26 Feb 2018 10:16am
Reply
Quoting: Just I would over hang the girders by 1 in. Just enough to keep them dry .
Bingo, I hate to see cantilever where a load bearing wall is not directly over the footing. Maybe its just me.
|
|
snobdds
Member
|
# Posted: 26 Feb 2018 11:00am
Reply
Quoting: caducus On that 2x12 frame, you're not resting that on any girders I take it?
No girders. All the floor joist are hung off the side and middle beams by joist hangers. I love modern mechanical fasteners and use them everywhere. Joist hangers are great because you will never get any lateral or compression movements. Plus with "TECO" nails holding everything together, it resists wind uplift coming from under the floor, since I am 3 feet off the ground.
Plus I wand my load bearing walls on the outside of the beams, nothing on the cantilevered portion of the floor.
|
|
caducus
Member
|
# Posted: 26 Feb 2018 11:02am
Reply
I understand not wanting to cantilever a wall. Though 1' on 2x10s with a doubled up rim joist seems adequate to me. I'd worry that in pushing out to the edged with the girders I'm getting up to a joist span that's a little spongy.
The other consideration is that the ridge I'm building on has much better soil the closer you get to the center line. Keeping the footings at that width feels a lot more stable than pushing them out to the full 14'. Not that I'd worry they'd fail being an extra foot out, but long term it would give me a lot of peace of mind.
|
|
caducus
Member
|
# Posted: 26 Feb 2018 11:07am
Reply
I just read this regarding load bearing walls and cantilevers:
"So how far can you cantilever joists and put a bearing wall on the end of the cantilever without engineering the joists? Loads transfer at a 45-degree angle through whatever is supporting them. Therefore, if 2x10 joists, which are actually 9 1/4 inches deep, support a bearing wall 9 1/4 inches from the support underneath, the loads will transfer at a 45-degree angle back to that support, and no engineering is required. So the answer is the depth of the joist from the support. Cantilevers beyond this distance need to be engineered."
So maybe there's a compromise there. 9 inches of overhang.
|
|
caducus
Member
|
# Posted: 26 Feb 2018 11:17am - Edited by: caducus
Reply
9 inches of overhang gives me 11'11" joist spans with the 2x10s. That works for a floor. What about the load bearing walls on the front and rear rim joists? Between the wall, glass windows, a heavy glass door, that's a lot of weight. I'm having a hard time finding load tables that take into account the load bearing wall weight on a rim joist. It would be doubled (tripled?) but I just want to be sure that 2x10 with a nearly 12 foot span is sufficient to carry a wall of the cabin.
|
|
ICC
Member
|
# Posted: 26 Feb 2018 11:59am - Edited by: ICC
Reply
Quoting: caducus What about the load bearing walls on the front and rear rim joists?
Rim joists are not there to support weight.They are used to prevent the floor joists from rotating. Rim joists are, after all, only nailed to the ends of the floor joists. There is not much strength to a nail connection into end grain like that. The rim joists also provide the connection point for nailing the subfloor sheet edges. Also note that because rim joists are nailed to end grain they should not be used to add a porch or deck to. In fact recent code does not allow that; there is special hardware that permits tying a deck or porch floor, past the rim and to the floor joists under the main floor. Just threw that in as an extra as this started out with a porch included.
I don't recall any mention of roof type. IF you are doing a gable roof the end walls are not load bearing walls. In that case the floor joists at each end should be doubled up. Those are not rim joists, they are floor joists and the load is carried down to the beam.
One of the potential issues with doing piers with beams on top of them is that the piers are only connected to something at the top end. The middle or bottom is free to move around, tilt, rotate, whatever if the soil permits movement. Wet soil has little resistance to lateral movement. That is why you will not find in any building code book, any reference as to how piers should be installed, which is why I recommended a poured perimeter footing or a PWF, also full perimeter.
You mentioned the dirt was better closer to the ridge top. How is it better?
And the mention of a ridge brings up the question of winds and uplift forces. Another pitfall of piers is poor performance for uplift resistance.
The cantilever info you found is bang on. Codes permit an overhang equal to the joist depth without needing an engineer.
If you use 2x10 you are fine on span with any commonly used species and grade according to the AWC calculator. At 16" OC you could safely install tile flooring. AWC also has mobile versions available now.
|
|
Just
Member
|
# Posted: 26 Feb 2018 12:12pm
Reply
As far as I know a 2x10 is good for a 14 feet floor joist . As long as you put the girter under that support wall there will be know worries . In this pic of our bunky the door is supported by a double rim joist it’s been there 6 years still works well .
|
|
caducus
Member
|
# Posted: 26 Feb 2018 09:40pm
Reply
was using rim joist to describe all joists around the perimeter. Obviously I'm mistaken.
Regarding actual rim joists, you mention that they aren't meant to carry the load of the wall. I've seen a lot of frames with doubled up rim joists. Basically double 2x all the way around the perimeter. But it sounds like you're saying that doubled up rim joists would actually be a problem, as the extra width would mean that most of the wall was being carried by the rim joists.
I was intending not to nail the rim joist into the endgrain, but to attach it all with upside down joist hangers. The joists would rest on the girders, and rim joists would attach to them on hangers. My original intention was to double the rim joists up and to double the end joists.
It's a shed roof. Sloped from one 20 foot wall to the other.
|
|
. 1 . 2 . >> |