|
Author |
Message |
upnorthmn
Member
|
# Posted: 23 Jan 2018 08:48pm
Reply
Hey all. Been browsing for about a year, first post.
My wife and I purchased some land last year. 40 acres in central Minnesota. The land we've got is pretty great, but it's fairly heavy clay. It retains a fair amount of water.
My curiosity is this: I look to build a 12 x 18 cabin. It's meant to be a placeholder until we build a house and then a workshop after we build the house.
What is advisable for a foundation? I've been reading about various methods, and most of them just seem too darn expensive/intense for what I'm looking for. 4' footings seem extreme. The floating cabin seems like a good idea, but I'm curious as to the details.
Any insight or experience stories would be appreciated. Thank you!
|
|
leonk
Member
|
# Posted: 23 Jan 2018 11:09pm - Edited by: leonk
Reply
Dry clay is solid as a rock, wet clay = disaster I said it many times before - either build proper foundation or stay on top of the grade (is it what you call "floating"?) Consider the above try to divert water away from the building, adding some crushed stone on top of textile might help with drainage. It really depends on the slope and land around. Freezing depth has to be 4' at least in your state, so you have to go deeper if you do decide on proper foundation, but again if it's not the main structure and the cost is a consideration, just don't dig.
|
|
Just
Member
|
# Posted: 23 Jan 2018 11:12pm
Reply
12x18 is getting close to the limit for skids , but very doable. Dig 8 holes two rows 11ft apart . The holes should go just below most organic matter . level the bottoms of each hole . Place as many shed pads (the ones I use are 12x16 in. By3in. Thick ) in each hole to bring the top pad above grade . Then place concrete blocks to get your cabin to your desired hight .Place them hole side up and fill with cement . Throw any spoil to the center of the cabin . The under side of the cabins grade should be higher than the surrounding ground. A sheet of black plastic covered with gravel will keep it dry under your cabin . That’s the way I do it and I have had good luck with mine . If the cabin settles a bit it can be adjusted with a jack and some shims . Goodlock
|
|
creeky
Member
|
# Posted: 24 Jan 2018 10:44am
Reply
Small buildings: I've done a couple of different methods. Floating has worked. Posts sank and shifted. I have had good luck so far (only 2 years) with helical piles.
Floating is the easiest. What I did was remove the grass. Put down heavy duty landscape fabric. You can find road fabric all the better. Then I put 8" of road gravel. I used 1.5"minus.
I put a 20x12 on top of that.
Can't say its been perfect. One corner has sunk. And this year I'm getting frost heave in the center of the building. It has been an unusually cold winter and I'm not there that much. So the building is colder than usual.
If I were to do it again I would probably have dug a deeper trench where the two beams go. Filled with more gravel. Maybe raised a bit more to allow for jacking up and releveling.
And maybe made more of an effort to keep critters out from under. Certainly sealing around the foundation has made the building easier to heat / warmer floor. (I use roxul wrapped in bubble wrap).
My building is designed to be removed.
|
|
fiftyfifty
Member
|
# Posted: 24 Jan 2018 01:04pm
Reply
Owen Christensen is a builder based in Duluth who used to post a lot on this forum and still does from time to time. He has built many sheds, cabins, and saunas, and floats a lot of them. Read all his posts if you haven't already. They contain a lot of good detail. He has been devoting himself to saunas lately, but a few of us on here (including me) are lucky enough to have a cabin built by him.
|
|
morock
Member
|
# Posted: 24 Jan 2018 03:06pm
Reply
My plan was to use helical piles but the clay has no strength. So I have straight piers down to bedrock. 3 rows of five cross braced on the corners in a triangle format. The building shakes because the clay has no lateral strength either, but the big thing is the frost heave. I have 4 foot plastic sleeves on the pipes to move with the ground. Without snow cover the frost goes deep and I have seen 8 to 10 inches of heave under my cottage. First year couldn’t open the front door, the ground heaved enough to grab the cross bracing and lift the pier. Another time one of my aluminum ladders leaning against the piers got rammed by a rock on the ground and was caught between my floor beam...destroyed it.
Wet clay is bad. What you might want to try is getting used foam board and try to prevent the frost from getting into the soil. I use 4 inch ship lap type to cover my septic holding tank so I don’t have to pull the pump every year. It does work but it is also covered with all the snow off the steel roof. You may need as much as 8 inch of board. Just an idea, but you need to be aware of how much the soil can move without snow cover.
Good luck.
|
|
upnorthmn
Member
|
# Posted: 24 Jan 2018 07:45pm
Reply
Well, I had a nice response penned but ... I have one of the newer Macs with the touchbar across the top. FYI, if you're into Macs and need a new one... avoid the touchbar.
First, thanks everyone for your responses. I really appreciate them. I was afraid I was going to get the "build it proper or don't build at all" scolding that I've seen a couple of times. Thanks for taking it easy on me!
The purpose of the cabin is to serve as a short-term living space until we sell the house in the city. After the house is sold, we can focus on building a house on the property. Once that is done, the cabin will turn into a workshop.
I'm trying to find methods that I can still do if I have to do them alone. I haven't got access to a pump for water (Despite the wet soil... irony!) nor digging equipment, hence my consideration for a floating base.
leonk - We've got some hills, so water moves away pretty quickly from the area we're looking to put the cabin. The southern portion of the land is a little soggy at times, and the forests are soggy. But the areas we're building in aren't horrible.
Just - How do you go about watching for the need to jack/shim? Do you eyeball it or do you measure somehow? This is something that I thought I could do, jacking it up and shimming. It adds some work, but keeps me from having to dig too deep.
creeky - If I might ask, where are you with the cold? Minnesota has been awful this year. If you're north of me, I can't imagine what it's been like. If you'd built higher for jacking/shimming, do you think your heaving problem would be less of an issue? Meaning, do you feel it would have been suitable for the long-term?
fiftyfifty - Thanks for the heads up! I think I'd seen his site a while back. I'll do a search.
morock - What you mention sounds similar to a Frost Protected Shallow Foundation (FPSF). This is something else I'd considered, but I don't really have access to concrete (I suppose I could bring a truck in). Trying to keep the soil below the building from freezing too deep may be an option. With the FPSF, the concrete works with the insulation to keep the ground warm. I'm curious if there's a way with a wood foundation to make it work. Wood doesn't seem to maintain/transfer heat as well.
Thanks again, folks. I really appreciate it!
|
|
Just
Member
|
# Posted: 24 Jan 2018 10:54pm
Reply
Upnorth ,,, if the cabin is strait when you build it you will soon know if it moves ,as the doors and windows will quit working properly. A 4ft. Level on the floor will soon tell you which blocks need shimmed. Because the cement shed pads are larger than the concrete blocks there is room toget a small jack between the slab and the skid and shim the block. It is important to not have any piers under the middle of the cabin as they would be very hard to shim .l usually use two shed pads and one concrete block , but if you need the cabin to be higher more can be used. The ones I have built are 9x12 ,that is max size in Ontario.i like to build them with a loft as there is not a lot of room in a 9x12 ..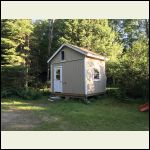 14EDFE8F2F1648F6B.jpeg
| 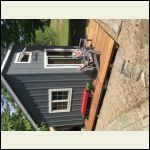 D78FA251A4B74CF2A.jpeg
|  |  |
|
|
creeky
Member
|
# Posted: 25 Jan 2018 09:38am
Reply
Quoting: Just A 4ft. Level on the floor Ha. I was reading your reply upnorth and I thought, "somebody needs a 4' level." And the next thought. "Bet that's what Just said."
I'm up around Just. North of you, but probably a bit warmer. Mn is mighty cold. And I'm an old prairie boy (way north). So we know cold.
The gravel base on my "great room" keeps the frost heave down a bit. In 7 years I haven't had to shim. But the one corner has sunk. I've been meaning to jack it back up and scrap some gravel under the beam.
And ya. My washroom built on stilts/posts heaves mightly. And this year is a very cold winter. What I've done is protect around the posts with sheet insulation. Its relatively haphazhard. Sheets of this that and the other thing. But it does reduce heave. I've had only minor heave this winter despite unusually cold weather and not a lot of snow cover.
So like a frost protected foundation. But its a post protected foundation.
And by minor I mean the door still closes. Even if it is a bit sticky at the bottom. Compared to the first winters I had heave (year two and three); where the door had to be held closed with a bungie cord.
|
|
Jammer
Member
|
# Posted: 28 Jan 2018 09:18am
Reply
I have a camp near Timmins Ontario. Been there 35years. Ground is clay with large boulders. My experience and advice to you is to clear topsoil, including all roots. Put down crushed rock and pack it making sure you are above grade. Get any drainage water to run away from each the cabin area. Put down cottage pads with concrete blocks on them. Put on your beams and build. You are going to have some frost movement."Do not try to level or shim until frost is out of ground". If you do you will be wasting your time. Good luck.
|
|
upnorthmn
Member
|
# Posted: 1 Feb 2018 01:47pm
Reply
Thanks again, everyone. Lots of great ideas and info. I'll most likely approach with clearing what I can of the top soil (lots of manual labor... better get some friends) and then placing crushed rock. Using pads on that and then placing skids.
I really appreciate the input. Thank you!
|
|
Mike 870
Member
|
# Posted: 1 Feb 2018 02:11pm
Reply
If you can, build on a “finger†where the land slopes down away from the cabin on each side. I have clay soil as well. Thankfully it was not too far to limestone rock where I built my cabin. In the video you can see how soft my soli is when it rains.
https://youtu.be/UcHQa2GQ-FQ
|
|
Steve_S
Member
|
# Posted: 1 Feb 2018 04:56pm
Reply
Quick note. You do need to clear the organics (roots, vegetation and more). Once done, lay down heavy Builder's Cloth, Road Cloth or Commercial Grade heavy landscaping cloth. Next you want a solid base of packed gravel to give a solid base. The Cloth prevents the gravel from being "absorbed" by the soil, clay etc as it will eventually just sink in.
An ounce of prevention is worth a pound of cure and a crap load of labour. To that end, you should very seriously consider & plan for drainage away from your build. The simplest solution is a combo of French Drains that can direct water, rains, snow thaw away from your spot. I would also note, that you do not want ANY depressions under your build IF not actually pouring a Slab. Make sure everything is well packed down and that there is a slight hump in center allowing for water to drain away rather than pooling underneath.
Keep in mind, that frost heave will happen for anything on surface and above the frost line. While an FPSF Foundation is "on surface" above frost line, the "wings" 24" + spreading out from the edge prevent the frost from creeping under the slab, this varies a bit depending on where you are and the colds you get.
I'm in North East Ontario, have an FPSF Foundation with 2' wings all around and no problems but I also have 4" thick XPS which is double what code requires (just happened to be what I could get really cheap [$9 for a 4'x2'x4" sheet] from a commercial roofing contractor).
|
|
tverga
Member
|
# Posted: 1 Feb 2018 05:26pm
Reply
I have a company that installs Helical Piles, wet clay is fine as long as there is some type of bearing soil below. During our installation we take torque readings and can determine the load capacity, if we do not hit our design capacity we weld on an extension and keep going. It is not uncommon in the Great Lakes area to put the helix 15-20' deep. The advantage is Helical Piles are cost effective and work very well.
The biggest issue for using them in cabin construction is they need to be installed by a certified installer. Installers tend to be in populated areas so getting them to come out to the woods can be a challenge. We cover Illinois and Indiana, and have done jobs in out of the way places, we just work with people on scheduling during our off season.
Let us know if we can help https://youtu.be/LC-uLJEwa6I
|
|
upnorthmn
Member
|
# Posted: 4 Feb 2018 09:08pm
Reply
I tried to contact a couple of folks about helical piles, but nobody responded. I was interested in the concept, as I have no running water for concrete and don't have any major equipment for digging.
Steve_S - If I could do an FPSF, that's what I'd do. It'd be the simplest for measurements and it would last longest. However, I'm not certain I'd be able to dig it all by hand or whether I'd be able to get a cement truck to make the trek out to my plot. It's a little bumpy.
How remote is your cabin? How did you get the cement poured for the foundation?
|
|
Steve_S
Member
|
# Posted: 5 Feb 2018 07:40am
Reply
Well, in my case, I had hired a excavation company to come in and clear my build pad area, parking pad area, driveway and such.... It was all done with a Cat DL-390 excavating beast because I am on Glacial Deposits meaning lots of rocks and Erratic's in excess of 30 ton. 18 Dump Trucks of Pit Run and crush to fill in all excavated space which was then packed down with that excavator.
We brought in a large cement truck and because I had the driveway done and everything well packed, it did not sink in (must avoid that always). I believe the Cement Factory is 120km/75 miles from me and the roads are good, even mine, so not a problem. The ONLY problem we did have was the truck making the turn into my driveway which at that time was only 20' wide with deep ditches on both side and the cement truck ... well... got a wee tricky (cement truck can get very tippy when just the right conditions happen).
** There is also a local company that comes and mixes cement on-site with a smaller cement mixer truck, they mix what you need, pump it out & float it all smooth. This can be cheaper in many ways and gives a bit more flexibility and easier if you want to colour/die the concrete or if you want to use Fibre Reinforcement instead of or with Rebar (rebar can make problems later when it rusts, swells and breaks the concrete, see under bridges). It's possible you may have a similar company nearby... That may be another option.
Well, you want at least 6" and up to 12" of the organic soil taken off and backfilled with neutral then packed really hard. The Daily Rental Excavators are not too bad in price and can do amazing work if you work smart. **NOTE** These are rented on a per hour or day basis of 8 hrs, they use the Run Time HR Meter to get that, so when not using the machine turn it off, idling is wasting your hour time. Some builder supply places, even HomeDepot rents such machinery, not bad a price generally. Make sure THEY run you through the machine use before driving off with it (also if something wrong, better to find out at store first, never assume).
You'll want 16x22 area cleared to put your 12x18 shack on, then you have a packed drainage area around your pad. Around that have your French drains to take water away. Laying up the foam for your Concrete Pad is easy enough but that again needs a plan and be well thought out when you get there.
I know your Building in Minnesota and you get a "Respectable" Winter every year. To that end, I cannot praise Radiant Floor in the concrete slab any higher.... The comfort factor just can't be beat and once that slab is at temp, takes very little to keep it there (my FPSF slab has 4" XPS foam [R-20] under & on the sides). I bought a complete radiant flooring kit which I installed prior to the concrete pour, complete with floor sensors. I highly recommend the method & the company that produced the kit http://www.radiantcompany.com/ Even got my Heater from them as you can't beat their pricing on that product line. PS: I even put Radiant Pex into the concrete slab of my Power/Pumphouse for future solar radiant heating.
Screw Piles / Helical Piles. The commercial solutions for structures work well and can reach depths depending on soil type, that can be an excellent solution BUT. There it is.... IF you want something to last 50+ years, a small metal pole stuck into the ground isn't the answer, coatings etc are irrelevant. I've used Screw Piles and no issues but realize they have their limits and lifespan points. I used these and their smaller versions as well http://pylex.com/en/products/10730-commercial-pylex-66-black These are not quite the same as the big commercially installed types that need machines but good for most things. BTW - WARNING: Drunken Sailor Talk occurs when your screwing the thing down and you hit a big rock that shifts you to one side (out of alignment) or stops you from going down...
After all that, I guess you have some pondering to do. A 12x18 on Skids could work just fine and still allow you to drag it somewhere later if you have a big machine to do that (that will be heavy). Or build as a Base that you can later attach more to and so build it with future planning.
I'll throw a Wrench into this for you to consider as well. Those "Garage Kits" you can buy from Builder Supply houses can be just the ticket in both cost wise and keeping it simple. The trick is to get a 2x6 framed build (some still sell 2x4 based kits) replace the Garage doors with French / Patio door and Window, insulate the building and voila... These Building Material Kits with plans are pretty good and often you can decide on siding etc or leave it off if you have something else in mind, you can upgrade windows & doors. I SEARCHED IN Minnesota and found this https://www.menards.com/main/building-materials/carports-shelters/shop-all-garage-pro jects/c-9891.htm Think of those 2 storey versions with dormers etc... IF I was to build my 20x24 Cabin again, this is what I would do instead of stick building from scratch and using my own plans... although I would "upgrade" a few things on the kits.
Hope this helps and that it gives you some options to ponder upon... at least with snow on the ground you have time to do all that thinkin 
|
|
upnorthmn
Member
|
# Posted: 11 Feb 2018 06:18pm
Reply
Steve_S
That is, without a doubt, one of the nicest responses I've ever read. Thank you.
I was able to find the Pylex 66 you linked. As a newbie, how many of these would you suggest for supports? Further, would it be worth considering to use these to make the skids to place the cabin on, versus completely digging up the space and putting down gravel?
|
|
Greenland South
Member
|
# Posted: 11 Feb 2018 11:09pm
Reply
My place is on clay. I bought a bunch of 10' 6" pipe at an auction and pounded them in until they stopped. Took me all weekend with a friends post pounder. You know, the ones for pounding fence posts. I did have to pre-drill with an auger for the first couple of feet so they would fit under the ram. They all went down about 8-9'. It's been almost 3 years and I haven't experienced any disernaful movement.
|
|
Greenland South
Member
|
# Posted: 11 Feb 2018 11:11pm
Reply
The smaller diameter posts in the picture are for the deck in case you're wondering.
|
|
Steve_S
Member
|
# Posted: 12 Feb 2018 08:45am
Reply
Thanks & Your Welcome. I try to answer anticipated questions and to also provide more "meat" to a newcomer reader when I can... part of having been a technical engineering type. 
Couple of things first you need to think on.
The idea of building on "skids" is to make a "shack" which can be moved / dragged. This is typically 8' wide and up to 24/30' length because such is built to be able to be pulled onto a flatbed for moving, not dragging across a property. Also keep in mind that a 12x18 cabin, empty but finished will likely weight in at 10 tons or more... I am NOT KIDDING, so this is not something your gonna be moving about easily on a whim.
Another typical reason for skids is to get around some building requirements in some regions and that's accomplished by building that way and so it's not considered as a "permanent structure". Again, that varies in regions and makes for headaches.
The load ratings etc are located on the Pylex Site and for the 66 they are pretty heavy duty. These are commonly seen on those temp barns with the canvas tops & hard sides (usually wood). See photo below as an example, and you can imagine the pull when winds get up under these, so the pyles are designed with that in mind.

IF you want to build with these you certainly could do it but appreciate the caveats for doing so. * not intended to last forever, maybe 25 yrs +/-. * Resale values, property values would be lower (temp building).
IF your still interested then I would think of 3 primary 6x6 runs with 6x6 cross, then a 2x8 floor joists and perimeter framing & build on top of that. See quicky doodle I just whipped up below. Note the compacted sub base of gravel that has a camber to prevent water from collecting underneath the structure. 6x6 overhang allows to attach porch etc & if ever needs to be moved, this will help. Wrap around deck / porch very highly suggested !
I would try to leave a minimum of 18" better 24" from grade to 6x6 so you can get access underneath when it's needed and if any water issues arise it will stay drier longer... not having enough space & air movement underneath invites mould, mildew & eventually rot, all of which is best avoided.
You do not want organics under your building, so it is really best to remove topsoil and fill + pack with a neutral thing like gravel and to make sure that water / dampness cannot affect from below... also prevents bugs & some critters.
NB> The whole clay being so close to surface makes me think your in a potential floodable spot... be very aware of water levels reached and potential for flooding. If you are on a floodplain, even if rarely floods, that really needs seriously better thinking and more planning. Look at how many folks get flooded out and the insurance etc is getting harder to get and crazy expensive too and even the Gov't won't help ya out much and that will not be getting any better in the future.
My quicky doodle.
|
|
upnorthmn
Member
|
# Posted: 12 Feb 2018 06:52pm
Reply
Greenland South I'd thought about using pipes. How did you pound the big pipes? My standard post pounder seems too small for that job.
Steve_S
I've no immediate (within 50 years) concern for resale. The cabin is being built for the following reasons...
1. Setup a temporary home to live in until the house is built. 2. To serve as a workshop for either my wife or I after we build the house.
My story follows. You can scroll right by if no interest. Right now, we've a home in Minneapolis with a fair amount of equity. The plan is to build a cabin that we can live in, sell the house in Minneapolis and then use the proceeds to build the dream home.
As a kid, my dad was an electrical engineer. He ended up hating his job and moving the family onto a trailer on the backwoods of an organic tree farm/nursery. As much as I hated the whole being yanked out of one like and thrust into another, I loved it out there.
I've gone to college, tried a few careers, etc. I hate the city life and I hate middle management (I work surgical services in a hospital, managing a team).
So, this is my out. We've bought 40 acres of land near where I grew up. While I'm serving out my time in management, we're going to start a farm and work on getting to that simple life we both want.
Anyway. That's where the cabin comes in. I've attached an image of the land. The spaces we're building are high; and one of them is half hill, so it would allow for water drainage pretty well. The blue spots are possible cabin locations, the red is where the house will be built. The southern (bottom) portion is the wet zone. We're going to build a pond down there to collect the water from the land.
I really appreciate the input. I've seen a smaller Pylex available on Amazon (Link to Amazon) It has the same weight bearing as the 66, but I imagine the lateral strength is less. Would this be usable for my purposes?
Thank you again.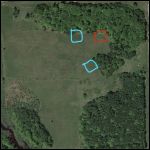 Land; blue for cabin, red for house.
|  |  |  |
|
|
Steve_S
Member
|
# Posted: 12 Feb 2018 07:43pm
Reply
Sounds like a good plan, I was just trying to be a bit more "complete". As for the point on resale, hey, I'm gonna die in my place, so... but sometimes shit & circumstances for unexpected reasons that can never be planned for.
Now that you describe the property details, that's a pile not to worry about your good to go there I'd say.
BTW, the one on amazon is ok for a deck, not what your doing. Those "adjustable's" are also a weak point. Good Heavy Duty ones should do just fine, you should be able to get the Pylex ones in the states, should check that out.
|
|
tverga
Member
|
# Posted: 20 Feb 2018 05:20pm
Reply
Quoting: Steve_S Screw Piles / Helical Piles. The commercial solutions for structures work well and can reach depths depending on soil type, that can be an excellent solution BUT. There it is.... IF you want something to last 50+ years, a small metal pole stuck into the ground isn't the answer, coatings etc are irrelevant. I've used Screw Piles and no issues but realize they have their limits and lifespan points.
Helical piles routinely out live pour in place concrete piles. Average lifespan can be over 100 years, schedule 40 or schedule 80 galvanized pipe. The Plex ones you list are only for temporary structures like landscape and free standing decks.
|
|
|