|
Author |
Message |
wascostreet
Member
|
# Posted: 14 Oct 2016 12:42pm - Edited by: wascostreet
Reply
Reading here has been super informative for my cabin build but I haven't found a comprehensive guide to foundation design.
Plan: 12'x12' shed/cabin with a loft - 45 degree pitched metal roof for high potential snow load. 2x6 walls and rafters/rafter ties.
Lot: Mostly wooded with very well-drained soil of varying depth over lava bedrock.
Site: Gentle slope, about 1' over 12'. Limited site access for heavy machinery. Frost line is 24". Surrounded by trees - low wind exposure.
I'm thinking post-and-beam/girder on piers. But how many piers, their spacing, how many girders of what size, and what joist size and span?
I think I could get away with two rows of 3 footings, the footings each spaced 6' apart, with 8' between the rows and a PT 4x6 girder atop each row. Then 2x8 PT joists spaced at 20" across the girders. This wold give an 8' joist center span with a 2' cantilevered section at each joist end. Forgive the not-to-scale ASCII illustration:
2'-><-8'-><-2' ----O------O---- |----|------|---- 6'---|------|---- |----|------|---- ----O------O---- |----|------|---- 6'---|------|---- |----|------|---- ----O------O----
Is there a guide in layman's terms as to how I should answer the engineering questions and get a solid foundation without overbuilding?
Thanks!
|
|
bldginsp
Member
|
# Posted: 14 Oct 2016 04:58pm
Reply
Do soil load bearing calcs. Calc the load onto each pier when the roof is loaded with snow. Determine the soil bearing capacity to determine the needed area size of each footing depending on its load. If you can dig all piers to bedrock, you won't need bearing calcs (with such a small building) or widened footings.
Size of foundation, number of piers, etc. is always a function of load carried and load bearing capacity of what takes the load.
|
|
rockies
Member
|
# Posted: 14 Oct 2016 07:56pm
Reply
You could try a pole barn technique where the posts go down into the ground below frost level and rise up to support the floor and roof. It's kind of like putting in a fence post and then the sill plate of your raised floor is attached to the sides of the posts.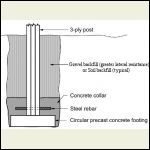 Typical Foundation detail
|  |  |  |
|
|
wascostreet
Member
|
# Posted: 17 Oct 2016 01:01am
Reply
So I found a soil survey and my soil type is "stony ashy loam". Looking for bearing data has been fruitless for this soil type. Where should I look further? Do I need a professional analysis?
I also visited the site today and dug some test holes at opposite corners. I hit what feels like bedrock on one corner at 36". At the other corner we went 4' down and hit no bedrock. Brought a sample of soil back with me if there's something I can do with that.
It was easy digging so sinking 9 holes wouldn't be a major issue labor wise.
|
|
wascostreet
Member
|
# Posted: 17 Oct 2016 01:05am
Reply
A local builder does pole barns: he goes down 4' with an 18" auger. Unfortunately the site doesn't have heavy machinery access.
|
|
Steve_S
Member
|
# Posted: 17 Oct 2016 07:23am
Reply
Can you get a two man auger in there ? or a Tow Behind unit ? They are typically available from most rural rental places.
Honestly for what your building I would not get too crazy over soil loads... You are not building a 3500 square foot log home that will weigh 100's of tons. Look at the land, the slope, drainage, flood potentials etc... Dig down 4 - 5 feet even and see what is there - that's the only way to know for sure.
K.I.S.S. is most often the best approach for most things unless you like complicated & we all know, more complicated = more cash...
3 Rows of 3 Posts creating three beams will hold it all up. How deep the footing / posts go depends on what is under it... 4' with 1' of gravel under that wide base to 8" tube... Have you seen Big Foot Forms ? REF: http://www.bigfootsystems.com/
Ground Clearance / Air Space should be considered (really depends on your climate zone too), water / plumbing considerations for draining and maintaining climate & usage dependent...
SLOPE: You say our on a slight slope, make sure you make a "swale" on the high side to direct / divert rainfalls - drainage away and around your cabin... So many folks forget that obvious detail which is so important.
Would it be possible to make use of that slight slope ? Like cut into it and build a retaining wall against the back and down the sides... Like a semi basement built with blocks open on one side with the cabin on top ? Store the ATV and other stuff underneath ? Maybe put a Garage Door on it even ?
|
|
sparky30_06
Member
|
# Posted: 17 Oct 2016 07:54am
Reply
DO NOT set wooden posts in concrete unless you are required to by code. They will rot off quickly. auger down 4', drop in a concrete round, set your post then backfill will pea gravel using a rod to settle the gravel every 6". the post wont move and will last a VERY long time. If your worried about frost heaving the post up go deeper. that's my .02 and how we built pole barns and set post up in northern Illinois & southern Wisconsin
|
|
wascostreet
Member
|
# Posted: 17 Oct 2016 01:35pm
Reply
I can get a 2-man auger in there and we had thought about that. We'd have to widen the holes manually anyway so I'm not certain that the auger adds a lot of value given that two guys dug two holes in about 30 minutes without much sweat. But it's an option.
We've only got about a 1' difference between high and low sides of the site, so a retaining wall wouldn't add a lot of headroom. The girders will add 8-10" above the top of the piers so will have about 1-1.5' below the floor joists at the high side for air space.
Swale: do you have an example to share?
On soil load - yeah i know it's overkill to get exact but I want to validate that I'm building right the first time. Nine (9) 8" piers with 16" footings will result in about 1400psf at the footings at the max snow load which is less than a published capacity I found for clay, so it really ought to be more than sufficient.
|
|
sparky30_06
Member
|
# Posted: 17 Oct 2016 02:36pm
Reply
any lumber within 18" of the ground will need to be treated lumber.
|
|
Steve_S
Member
|
# Posted: 17 Oct 2016 05:41pm
Reply
Swales are effectively small ditches which simply take the water where it won't harm your building(s) or property... The trick is in the detail... Using rocks & heavy landscape cloth to allow water flow and prevent t from filling with debris. This is all very dependent on the land it is being applied to, so there is no "instant answer to do it X way".
Best I can do for multiple examples is this: https://www.google.ca/search?q=drainage+swale&source=lnms&tbm=isch&sa=X&ved=0ahUKEwi3 tJGa5eLPAhXKDpoKHW8GCaAQ_AUICCgB&biw=1112&bih=908#tbm=isch&q=drainage+swale+detail
A pinch of water management / control at the start will save many many hours of potential grief and retrofitting when needed. IT IS NOT MANDATORY but one if those things that many start with "should've, could've, would've", which I personally hate to the extreme after the fact....
9 Piers in 3x3 format as you stated should be pretty darn solid... The trick is that bottom 6" of gravel and a wide enough base - Why I like the Bigfoot forms. Used then a few times in different projects and well... made me a fan of them.
|
|
wascostreet
Member
|
# Posted: 17 Oct 2016 06:32pm
Reply
Plan is to do PT to the subfloor - so girders, joists and subfloor all PT. Most of the joists would be above 18" from soil -- is there any reason not to do all PT?
The site is sloped but it's not on a slope, if that makes sense. There's no uphill, the site is just at the foot of a 10' high pile of weathered lava rubble. The surrounding area is mostly flat. I'll keep drainage in mind for sure though.
I did some calcs on girder and joists:
Girders: according to IRC guidelines for a girder supporting a floor with center beam support, ceiling and roof, two (2) 2x10s would span between piers and not be overkill. Joists: 2x8 at 24" OC would work for joists, 16" OC would actually be overkill. But it's only 3 extra joists.
If I use 16" OC in the floor joists, does that limit me to using the same spacing in the wall and rafter framing?
|
|
bldginsp
Member
|
# Posted: 17 Oct 2016 06:50pm
Reply
Quoting: wascostreet Nine (9) 8" piers with 16" footings will result in about 1400psf at the footings at the max snow load which is less than a published capacity I found for clay, so it really ought to be more than sufficient. Yes.
Frame spacing can be different in floor, wall and rafters.
I personally believe the is no sense in using PT for such a subfloor unless you adequately soak the exposed cut ends. If not they just rot out the center of the stick
|
|
Steve_S
Member
|
# Posted: 17 Oct 2016 08:16pm
Reply
For what your building a few extra joists, studs & rafters for 16oc doesn't really add up to much more really, so it's a matter of choice... Building 3000 sq feet then the extra lumber get's steep.
I'd do PT and as bldginsp pointed out, treat the ends.
For the rebar you use in the piers you might want to consider using epoxy coated ones. If you bend them for shapes do it gently as possible. The reason I suggest the bit extra expense, is the epoxy will help prevent the steel from rusting & swelling cracking the concrete eventually. Might take longer than you'll use your cabin in this lifetime, but.... Available at big box building supplier, pretty much everywhere...
|
|
rockies
Member
|
# Posted: 17 Oct 2016 08:57pm
Reply
What are you going to do about water and septic? Did you have a perc test done?
|
|
toyota_mdt_tech
Member
|
# Posted: 17 Oct 2016 10:23pm
Reply
I would not cantilever it, maybe a bay window, but not the entire sides. Just my opinion.
|
|
tverga
Member
|
# Posted: 18 Oct 2016 05:21pm
Reply
Have you considered Helical Piles? Installation should be less than a day. You will be charged travel time depending on your location but all the calculations will be done and you will have piece of mind.
|
|
wascostreet
Member
|
# Posted: 24 Oct 2016 12:35am
Reply
So I dug my footings this weekend. We dug 18" diameter holes to 42-44" (frost line 24") and backfilled with 4-6" of 3/4 minus gravel. After tamping down the holes are 36-38" deep. It doesn't look like 16" footing forms are available so I thought I would just pour footings directly on the gravel 6-8" thick. Goal is to have all footings at 30" or deeper.
This would help me split the pours which we're doing by hand. I could do the footings, let cure then level, square and plumb the pier forms and backfill.
Questions:
1) Can I do the footings one weekend and the piers the next? I have limited time and don't want to start a time-limited process without being sure I can finish it. 2) What's the smart way to do rebar? I will definitely add rebar and intend to keep it fully encased in the concrete. 3) is there a foolproof way to keep the pier forms from getting water damage? Again, time is my enemy and I may have to leave the forms in place until I can get out there again. Is there a plastic form available?
And finally - we hit bedrock in one hole at 34". Should I just pour the pier on the rock or just pour a shallower footing?
|
|
bldginsp
Member
|
# Posted: 24 Oct 2016 12:55am
Reply
1- yes, but make sure the footing concrete is clean and have rebar sticking out, embedded in the footings 2- put 2 #4 rebar each way in the bottom. Make U shaped #4 rebars that are embedded in the footings, and the curve of the U sticking up, with corresponding U shaped post bases at the top, the Us interlocked. 3- sonotube is supposed to take a rain or two, but don't risk it. Get yourself all set up to quickly install the sonotube when you arrive, with parts all cut out to hold them in place etc. Have a shop vac there to suck water out of the holes if necessary. Rather than pour footings one weekend and piers the next, I'd do each one complete, do half this weekend, half the next. Concrete on bedrock is the best you can possibly do. But if the bedrock is at an angle, bore holes in it and put in some rebar pins to keep the pier from sliding off. Post pics!
|
|
wascostreet
Member
|
# Posted: 24 Oct 2016 11:33am
Reply
Good stuff, thanks! Follow ups:
1) what tools are necessary to work with rebar, in case I either need to bend it or cut it onsite? I'm without power at the location but have a battery jigsaw with metal blades as well as a hacksaw and volunteers. 2) how close to the top of the column should the rebar extend?
And the big question: my approach idea has been to set the forms all together to ensure square/level/plumb before the pour. I intend to use backfill to hold the form, not framing, which requires pouring the footings first. In my mind that's a more foolproof method to get things right. But I'd have to get the rebar height and center correct when doing the footings if done separately.
Is it better to just do a row at a time, then? Could I start with one column, get it right and pour it, then set the next column and take the level from the first with a water level, etc. etc.? Or is it better to do several at a go?
This is probably too anal. I assume I need the piers to be very close to perfect, and that the column-top fittings for the girders do actually need to be perfect. Just wondering how perfect at each step. This seems like the right place to take my time and get it right.
|
|
bldginsp
Member
|
# Posted: 24 Oct 2016 01:38pm
Reply
Yes, take your time and make sure all is correctly aligned. Best way is with batter boards and string lines. Look for pictures on the web, but basically you set up four strings level and square to the outside line of the building or the post bases in the piers. Leave the batter boards in place until all concrete is poured so you can verify alignment frequently. Use 3,4,5 right triangle to make sure it's square. It really pays to line it all up very carefully.
They make rebar cutters with a big lever for both cutting and bending rebar. For a small project like this you may not need that. Hacksaw works to cut rebar but it's a lot of work. Battery sawzall works well, as does angle grinder with cutting wheel.
You should have two rebar vertically through the length of the pier, looped over a post base for uplift.
|
|
wascostreet
Member
|
# Posted: 24 Oct 2016 03:23pm
Reply
What do you mean when you say "looped over a post base for uplift"?
I thought that maybe I could drive one rebar vertically at the center of each column, which would serve as reinforcement and center mark.
|
|
toyota_mdt_tech
Member
|
# Posted: 24 Oct 2016 05:15pm - Edited by: toyota_mdt_tech
Reply
Quoting: wascostreet So I dug my footings this weekend. We dug 18" diameter holes to 42-44" (frost line 24") and backfilled with 4-6" of 3/4 minus gravel. After tamping down the holes are 36-38" deep. It doesn't look like 16" footing forms are available so I thought I would just pour footings directly on the gravel 6-8" thick
Caution, use a smooth sided sono tube for the form in those holes after the footers are in place. Just pouring cement in the dug hole can and will still lift up. As it freezes, it will hold onto the irregular shaped sides of the concrete column. Footer pinned with rebar, maybe not. No rebar, good chance.
|
|
wascostreet
Member
|
# Posted: 24 Oct 2016 05:21pm
Reply
Yep, the plan is to pour the footings in place directly on the gravel bed, then use sonotube or similar for the column form. The top of the footings will be at least 6" below frost line.
Anything to consider when pouring concrete on a compacted gravel bed? I assume I'll have to agitate it some to make sure there are no voids, but will it tend to mix with the gravel bed or drain through or...?
|
|
Just
Member
|
# Posted: 24 Oct 2016 05:40pm
Reply
Were I come from we pour cement on undisturbed soil it is thought to be better than trying to compact other materials.
|
|
wascostreet
Member
|
# Posted: 24 Oct 2016 07:01pm
Reply
And one more question: when I think about ways to set rebar, I'm having a hard time with how to suspend it above the bottom of the footing to encase it. I understand that rebar needs to be encased in concrete to prevent corrosion. But the footing will be on crushed gravel on well-drained soil, so would it be a bad idea to make a "cage" that I could just set at the bottom of the hole, center and plumb, then pour?
The base of the rebar would be on gravel and not encased - would this be a bad idea? Upthread i thought about driving a piece of rebar into the center of the hole, but that would definitely create soil contact.
|
|
wascostreet
Member
|
# Posted: 26 Oct 2016 04:48pm
Reply
So I think I've figured out how I'm going to set rebar and pour the bases and columns. What I can't seem to find is the right beam base to set at the top of the column. I plan to use doubled 2x10 girders across the width of the foundation with the joists on top. But the bases I'm finding in the stores look like they're for 4x posts set vertically, not doubled 2x lumber.set horizontally. What should I be looking for?
|
|
sparky30_06
Member
|
# Posted: 27 Oct 2016 06:52am
Reply
these might work
http://www.homedepot.com/p/Simpson-Strong-Tie-12-Gauge-Bolted-Holdown-HD3B/202796760
or use the ones for 4x4 post and pad the outside of your doubled up girders and threw bolt them
|
|
|