|
Author |
Message |
kenn
Member
|
# Posted: 13 Mar 2016 11:07pm - Edited by: kenn
Reply
I'm planning on building a 16x36 gambrel style roof. I've gone over and over various designs, plans, etc. and have arrived a using a twin board 2x10 bolted together and down the middle to build the subfloor and then T&G plywood on top of that. The hard part is figuring out the best bet for support. Best, of course, would be post-tension slab but that is expensive.
I've considered piers but I would probably need to go down 4-5 feet to get below the clay and based on the building size, I'd need 10" or 12" piers with footers. The footers mean I'd have to either backhoe giant trenches or get someone to auger me 24" holes so the base will fit. The cost of all of this would be about the same as just having a slab poured.
The third option is to pour 2x2x6" or 2x2x8" rebar reinforced pads at the surface. I'd basically scrape down, tamp in some gravel, and build a form using 2x6 or 2x8 and fill with 3000 or 4000 psi cement. I'd use a laser level to get them all very close and I'd use 21 total putting them 6' apart lengthwise and 8' apart widthwise. Floor joists would be 2x8 which is plenty for the span. My thinking on the mini-pads (other than being 1/3 the cost) is that I can jack them, repair them, or even repour if one gets really bad. I would put two concrete blocks on each to give 16" of rise so I can plumb, insulate, etc. underneath. Is the 2x2 pad even a feasible option or is it a really bad idea?
|
|
Just
Member
|
# Posted: 14 Mar 2016 09:44am - Edited by: Just
Reply
You only need to go as deep as the frost line even if it is clay . With a building that large surface pads are not a good way to go . And concrete blocks are never good for making piers .
|
|
tverga
Member
|
# Posted: 14 Mar 2016 01:09pm
Reply
Helical Posts, one day install, frame the same day...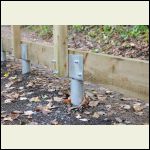 DSCF4776300x200.jpg
| 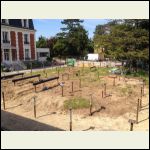 IMG_3489MansTours3.jpg
|  |  |
|
|
Julie2Oregon
Member
|
# Posted: 14 Mar 2016 07:49pm
Reply
I'm having a 14X24 gambrel built and we're going with a perimeter crawlspace foundation with rebar. Not sure yet if the perimeter is going to be block or ICFs. That will depend on whether a cement truck can get to my land. We ARE going to excavate down to the bedrock. It will make for a solid foundation in a seismic zone.
But I'm not dealing with clay, thank goodness. Are you excavating yourself without big, heavy equipment?
|
|
kenn
Member
|
# Posted: 15 Mar 2016 12:21am - Edited by: kenn
Reply
Those posts look pretty cool. How much were they installed? I'm in central texas and "extreme" frost penetration would be about 5" max. Most years it is very little. Maybe an inch.
I've got a tractor with a pretty robust box blade and can cut channels pretty easily. Below frost depth would be cake.
I'm trying to keep this as inexpensive as possible but I don't want the building shifting around. In looking around at the helicals, they seem to be $300 per coil or more. On a 16x36, I'm guessing 18 or so "piers" which would set me back $5400. I got a quote for less than that for a full slab. With a good gravel and soil prep and keeping the perimeter watered so it doesn't swell/dry, I'd probably be fine.
Thanks for the information guys -- I appreciate it.
|
|
kenn
Member
|
# Posted: 15 Mar 2016 10:28pm
Reply
Ok, I got a helical quote today and the estimate was 300-400 per. I'd need 15-18 making this a really, really expensive foundation! I've asked for clarification on span as, obviously a 10' span would reduce the number of piers dramatically.
That said, I can get 24" holes dug and put a concrete footer in there with a 24" base. According to several calculators, clay is 1500-2000 psf soil capacity. I do have a little bit more sand as I dig down and probably could estimate 2000. 1500 is worst case scenario - pretty much pure clay. On a 24" base, Id still get 6K+ pounds per pier and if I assume 50lbs per square foot on a 16x36 cabin, I'm still about 3x over the capacity. I can get the holes dug for about 30 per and a 12" tube+base is about .24 CY. Whole thing would be about the same and 3 helicals. I'm not set on concrete piers, but man, 5-6K for the helicals is, well, a lot.
|
|
Don_P
Member
|
# Posted: 15 Mar 2016 11:22pm
Reply
50 psf is the total for a floor load 40psf live+10psf dead. add at least 20 live + 10 dead for a roof if just single story.
Helicals and piers also have lateral issues that the slab won't.
|
|
carr0406
Member
|
# Posted: 16 Mar 2016 10:18am - Edited by: carr0406
Reply
I built a 16x32 Cabin on two rows of pads. 6 feet apart. The frame rest on two large skids. I followed Owen Christensen on this forum who has a lot of experience building on skids but I bet 36 feet long would be pushing it...My cabin has not moved yet though I'm trying to keep weight down by using a metal roof.
|
|
tverga
Member
|
# Posted: 16 Mar 2016 12:48pm
Reply
Quoting: kenn Ok, I got a helical quote today and the estimate was 300-400 per. I'd need 15-18 making this a really, really expensive foundation! I've asked for clarification on span as, obviously a 10' span would reduce the number of piers dramatically.
The cost per pile may be high due to the remote location, I have seen them installed for less. As far as the 10' span that depends on the floor joists, the larger the joist the greater the span.
|
|
bldginsp
Member
|
# Posted: 16 Mar 2016 01:22pm
Reply
Clay is the worst soil type to build on, because it is so plastic that it almost has to move when weight is applied. Even when you are at or well above the assumed soil bearing capacity, I'd be a bit nervous about it moving over time. So you could put in separate pads and plan to jack the building up later, but that's a lot of work.
Getting a big tractor out there with a boring attachment to cut deep piers wouldn't cost too much, you'd be done in less than a day. But piers don't provide much lateral support.
Have you considered a mat slab? It's a thick slab, say 1 foot thick, with mats of rebar in both the top and the bottom. Your idea of a 6 or 8 inch slab with 4,000 lb concrete doesn't really address the problem- you want a slab that won't crack and bend. Stronger concrete is just stronger in compression and can still crack in tension. That's why having a lot of rebar in both the top and the bottom will prevent such a failure.
Scrape it down 6", put up 2x12 perimeter forms, gravel-plastic-sand for vapor barrier, #4 rebar at 12" in the bottom, same at the top, perimeter bolting and go.
Such a slab will float on the clay. This method is used in areas of extreme freezing in poor soil where it's impossible to get away from heaving.
|
|
kenn
Member
|
# Posted: 16 Mar 2016 08:27pm
Reply
Thanks again, guys. I think I'm going to seriously explore concrete piers. I know they don't provide as much lateral support, but I'd go 12" and put a 24" footer at the base. I think I can get 24" holes drilled for about 30-35 a hole. I'd either use a bigfoot or just elevate the tube 12" above the floor of a 24" hole tamped with 1.5" gravel. That would give me about 3.13 square feet on the footer. Bigfoot systems BF24 (24" circle also) provides, according to their engineer-stamped data, a max load on clay of 6283 lbs. Using a 12" tube would give me greater lateral support. Cost for one pier would be:
hole - $35 .24 CY of cement for the tube and base - $28 1/2" by 5' rebar x3 per hole - $7.50 1/2" by 2' rebar x3 per hole - $5.00 Mount plate of some sort $20 (guess)
I'd be all in for one post @ 95.50 x 18 would be $1719 total.
In looking around at "weight of a building", it seems that 40-45lbs per square foot for a wood-framed building seems to be about normal. I'll be using a metal roof which I believe is quite a bit lighter and even if I assume 60lbs per square foot, I'd be 576 square feet (16x36) totaling about 35K lbs total. 35K/18 is 1944 per pier if evenly distributed (it's not because of perimeter) which would be 1/3 of max load. If I assume 90% of the building weight is at the perimeter, I'd be at .9(35K)/14 or 2250 pounds on each perimeter pier. There is some "sandy loam" or orangish sandy clay-like stuff that appears as you go down. In some areas it's a couple feet down while in others, it is just below the surface. If I go down 4-5 feet, I'm hoping I'll find nothing but that sandy stuff as if I can get below it with a footer, I'm hoping I'd be OK with the 12" piers.
Any thoughts on this plan?
|
|
bldginsp
Member
|
# Posted: 17 Mar 2016 01:37pm
Reply
90% of the building weight will be at the perimeter if all roof loads go to the walls, but it won't be evenly distributed. The corners take half what the mid sections do. You can calc this out and reduce your concrete needs.
Piers aren't much for lateral unless they are 15-20 feet deep. I personally think piers are fine for very small buildings, but yours is beyond that. For a building this size I think you should at least consult an engineer.
I'm not an engineer, but I have seen some small building foundations with a partial spread footing for lateral support, then piers to support the rest. This would need to be designed so the walls not above spread footing have shear transfer to the partial spread, through floor diaphragm, etc.
|
|
kenn
Member
|
# Posted: 18 Mar 2016 02:29pm
Reply
bldginsp,
Thanks for the input. I believe we may be talking about the same thing. My idea for piers was that they would all have footers which I believe is the same as a spread footer, is it not? Basically 4' of 10 or 12" concrete pier with a 24" diameter base. I could do it with bigfoot forms or clean the hole well of lose dirt, pack 1.5" gravel in with a tamper, raise the tube form up 12-14" and brace it so that once the concreted is poured, it forms to the side of the 24" hole until it reaches 12-14" at which time it would fill the form.
As far as calculations of side loads go. Hows this: 16x36 cabin. 60psf for the building. 90% on the side walls. At 9' apart, there would 5 piers on a side. 90% side weight is 15,572. If 75% of this weight was on the middle three posts (2 remaining corners holding 25%), that would put about 12K pounds or 4K pounds per form on the middle 3. That is still a good bit under the 6250 or so rated pounds on clay for a single bigfoot 24" form.
I'm not necessarily trying to talk myself into a bad path, but I have to get this done inexpensively but it needs to last. In a nutshell, I'm trying to violate the axiom, "Good. Fast. Cheap. Pick any TWO."
|
|
bldginsp
Member
|
# Posted: 18 Mar 2016 03:10pm
Reply
Sorry, I'm sick right now and not in the mood for calculations.
But piers and spread footings are not the same, because piers are all independent of each other, and can move independently, or lean. A spread runs the full perimeter.
Good luck
|
|
Just
Member
|
# Posted: 18 Mar 2016 04:49pm
Reply
with a shovel dig 10 holes 16 in' deep and 24 in . across ,,14 ft. apart,, keep the sides as perpendicular as u can. pour 10 in. of cement with rebar. install protruding rebar for pier, cover each protruding rebar with a inverted 5 gal. plastic pail, press into the wet cement 1in. next day cut the tops out of the pails and fill with cement , add anker bolts GOOD FAST CHEAP YOU ASKED !!
|
|
neckless
Member
|
# Posted: 20 Mar 2016 09:06am
Reply
i dont like pads ,they are not evenly distrbiting the weightand frost can move one or two ,than the shifting starts... its -40 here some times.3ft frost,,, i have a 16 x 20 cabin that i built on a wood fondation that has two walls drywall ,no cracks in 10 years, i started out with railway ties and put them in a trench all most flush with ground,than added treated bridge decking 3x5 16s on top, than made a 16" pony wall with glued treated plywood on face,,,this is the start floor,beam across center and built like a nomal house,after the pony walls were up i mix ed a couple wheel barrels of concert and smeared the in side of footin were ties meet . this mouse proof. this was labour intensive ,but iam very happy with the rusals ten yeas later
|
|
creeky
Member
|
# Posted: 20 Mar 2016 10:05am
Reply
I have similar soil. Actually maybe even worse. Here is what I found doing research.
It's from greenbuildingadvisor. Response #5 is what you're looking for. Response #18 discusses your ideas clearly. It is very similar to Justs response in fact.
In my area. A local fellow built a slab foundation for his workshop building. He followed a similar process to #5. He used 18" of crushed aggregate for the drainage area protecting the slab. 10 years on and his slab is perfect. This with a great deal of heavy construction/farm equipment moving in and out etc. His slab is heated year round.
Also look at the waffle mat foundation. wikipedia has this to say.
Especially if you're looking to save $$$.
I liked a foundation created by a fellow in Saskatchewan but I can't find the link anymore.
He built a "rubble trench" foundation ala Frank Lloyd Wright. Modified with XPS insulation on top. Then he poured a concrete beam over the trench. And then built a huge house on top of that. It worked the ticket. Cheap and easy.
Good luck.
|
|
kenn
Member
|
# Posted: 27 Mar 2016 02:30pm - Edited by: kenn
Reply
Thanks for the data, creeky. Your first link doesn't open a thread and I've done a few searches and can't find anything with 18 posts or more that seem related. Would you please let me know the link or thread title? I'll look into these other ideas as well. I should add that my frost depth here is maybe 5". This year we had no freeze at all which is typical for the area. We got down to the low 30s/high 20s for a day or two but right back into the 40s. I'm not worried about frost heave. My concerns are the drying/shrinking and absorbing/expanding clay.
|
|
Asher
Member
|
# Posted: 29 Mar 2016 10:52pm
Reply
I originally had the same mindset as you in the piers. The advice here wasn't promising with the use of piers... I talked to a local concrete guy about options. He said, if I wanted to do piers they do them all the time (here is how he does them), they pour a footing for the entire perimeter of the structure and then set piers off that structure and on the 4 corners they would make L-shaped forms that extended 2 foot in each direction, this will tie everything together...
Then he suggested another option pour a footing and build a block foundation off of that. So I am going the poured footing and block foundation direction... here is where I am at after last weekend... You can't tell very well but that is a solid rock shelf I have gotten down to..
I rented a Kubota B26 for the weekend to do this digging, I was a little worried about the size at first but after a couple hours it was blowing through those boulders like a pro...
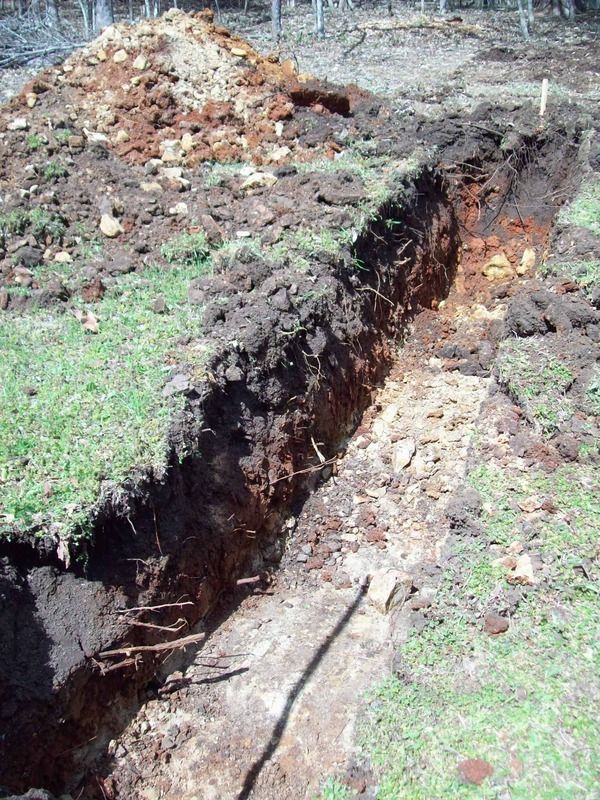
|
|
Don_P
Member
|
# Posted: 30 Mar 2016 07:31am
Reply
Quoting: Asher they pour a footing for the entire perimeter of the structure and then set piers off that structure and on the 4 corners they would make L-shaped forms that extended 2 foot in each direction, this will tie everything together...
... with rebar from the footing up into the piers and braced corners. He's picking up uniform bearing, and then bracing the corners, two things you don't get with the fencepost type pier. In shrink swell conditions, it would probably be a deeper reinforced grade beam.
|
|
|