. 1 . 2 . >> |
Author |
Message |
mollym
Member
|
# Posted: 2 Oct 2010 08:33pm
Reply
We just had our cabin built. It's on skids on concrete blocks with an insulated floor. Soffits are closed, no roof vents, metal roof. We plan to insulate the walls and underside of roof, (no ceiling) ourselves. It's a 12 x 16 with log siding and OSB sheathing. So far we've been using catalyst tent heaters, but plan to install a vented propane heater within the year. My concern is condensation rotting out the OSB. We were going to use faced fiberglass bats with a poly vapor barrier over that. We would probably only use it a few winter weekends a year, but it gets pretty cold this part of Michigan in the spring and fall as well. I don't see an easy way to vent the underside of the roof. Should we worry?
|
|
hebegbz
Member
|
# Posted: 2 Oct 2010 08:54pm
Reply
Your unvented heater is pumping water vapor and soot into your cabin. You will really be glad when you get a vented heater. I doubt you will damage your OSB the first year, but you will be amazed at the amount of H2O in the air.
|
|
mollym
Member
|
# Posted: 3 Oct 2010 02:55pm
Reply
Thanks for the reply. I'm more worried about the water vapor over the long term even after the vented heater is installed. Justing breathing and a little cooking can create quite a bit of moisture. We're using damp-rid which might give us an idea how much water is being produced.
|
|
toyota_mdt_tech
Member
|
# Posted: 3 Oct 2010 05:42pm
Reply
Insulating the ceiling will create condensation inside the closed up roof. You need to have air ventilation. What size is your rafters or trusses? Hopefully, they are 2X8 or so. If you have a 2X6, you can add insulation that doesnt fill the entire area, ie R13 made for 2X4's, this will leave you an air space between the insulation and the underside of the roof. But you'd need each span to be open to air flow at the bottom and top. It can move air under the eaves up between the rafters and out the top via a ridge vent. Otherwise, once heated, the cold and warm will create sweat.
|
|
dk1393
Member
|
# Posted: 3 Oct 2010 08:52pm
Reply
What about using close cell spray foam insulation?? I don't think it is affected by moisture.
|
|
mollym
Member
|
# Posted: 3 Oct 2010 10:25pm
Reply
We only have 2 x 4 rafters. It's a vaulted ceiling with 4 ft 2 x 4's tied horizontally about a foot below the ridge. We were thinking of putting gable vents on each end of the gable and leave that triangle of air space at the ridge open. But it seems from what I'm hearing that fiberglass bats will do more harm than good, even with a vapor barrier. We can't afford spray foam. What about ridgid foam boards?
|
|
hebegbz
Member
|
# Posted: 4 Oct 2010 12:17am
Reply
If you actually lived there all the time, moisture would be a big problem. But since you will only use is from time to time, I would worry more about not being cold.
|
|
MtnDon
Member
|
# Posted: 21 Oct 2010 03:53pm
Reply
If you can afford the rigid foam panels I would install them under the 2x4 rafters and leave the rafter bays open, unfilled. Then cover the underside of the foam with whatever you want. Furring strips may have to be attached on the underside of the foam sheets, with screws through the foam to the rafters. Then install soffit venting and vents at or near the ridge. The open rafter bays will provide all the venting you need.
|
|
mollym
Member
|
# Posted: 13 Nov 2010 02:43pm
Reply
MtnDon, That sounds like a good idea. We are going to find out for sure how much spray foam would cost. If it's out of our price range I think the ridged foam boards would be doable. It wouldn't be very high R-value , but it's just a little space to heat. And it would make for a lot quieter roof as well. We have till spring to figure out which we'll do. Thanks.
|
|
fthurber
Member
|
# Posted: 22 Nov 2010 05:00pm
Reply
Can someone explain the purpose of a vapor barrier? Everyone uses is for home but I don't understand why. Is it for insulation? Wouldn't it prevent the cabin from breathing?
|
|
MtnDon
Member
|
# Posted: 22 Nov 2010 06:29pm - Edited by: MtnDon
Reply
Vapor barriers originated in cold climates and should have stayed there. They have unfortunately migrated to other climates by builders who don't know any better.
Moisture in the air (vapor) wants to migrate from the warmer side to the cooler side of the building. In a cold climate water vapor from the interior would migrate through to the cold exterior wall and condense. Once there it will cause problems. So a vapor barrier is placed on the inside. This can be a plastic sheet under the drywall for example, or even a special paint on the drywall. Water vapor is prevented from reaching the cold exterior wall.
There are many places where a vapor barrier should not be used. Hot & humid climates with indoor refrigerated air conditioning is one. If a vapor barrier is applied under the interior finished wall humid air from the outside will try to get to the colder inside wall. It will condense there inside the wall. That is bad. In a hot & humid climate moisture in the wall will dry to the inside air conditioned space (with its reduced humidity), if there is no vapor barrier present on the inside.
Trivia: For a hotel to obtain a 5 star rating it must use vinyl wallpaper in the rooms. In the hot & humid south those hotels grow mold in the walls right under the wallpaper. Continual remedial action is required. Keeps a lot of people employed.
Great source for assorted building information is Building Science.
Here's a good article on Vapor Barriers from there.
There are air barriers and there are vapor barriers. They are different and confused by many people. Here's an article on Air Barriers vs. Vapor Barriers
|
|
fthurber
Member
|
# Posted: 22 Nov 2010 07:33pm - Edited by: fthurber
Reply
I still do not get it. Here is the northeast the weather gets really cold and there are a zillion traditional old homes built long before vapor barriers that are still standing. Drafty but no rot. I would think that a vapor barrier will keep the moisture in and rot the house.
A very very experienced wooden boat builder who knows a thing or two about construction was telling me that he cannot understand why he sees all these new houses with the vapor barrier on the outside of the house (outside the sheathing) just under the siding. This is going to trap the vapor against the sheathing. He suggested the vapor barrier on the inside if at all.
My wife who lived in Houston said that in the 80's a ton of new houses were constructed with OSB and vapor barriers but they did not last long. Junk disposable plastic houses.
|
|
MtnDon
Member
|
# Posted: 22 Nov 2010 08:06pm - Edited by: MtnDon
Reply
Quoting: SquidLips Drafty but no rot
Exactly. The drafts removed the excess vapor, but also greatly increased the heating bill.
As I mentioned above many folks confuse air barriers and vapor barriers.
The wraps on the outside are not vapor barriers. They are air infiltration barriers. Tar paper or building felt is the original air barrier. Tar paper stops air movement but does permit vapor to pass through. The felt absorbs water and the water can evaporate. The new wraps, called housewraps, (Typar, Tyvek, etc.) have very small holes or pores. They are supposed to keep liquid water outside while allowing the smaller molecules of water vapor to pass through, inside to outside. Unfortunately if water vapor condenses under the housewrap it is trapped. Being liquid it can not pass through the housewrap to the outside. It can be absorbed by the OSB though, and lead to mold problems. Bad news. That water would have to be heated enough to vaporize before it could get through the housewrap. If the builder had used old fashioned tar paper that water would be absorbed by the tar paper. The water would wick to the outside and be able to evaporate. Good news.
House wrap is very popular with contractors; it goes on faster than tar paper / felt, reducing labor costs. It is also promoted as being the best thing since sliced bread. That is not always true.
Some of the problems with modern housewrap stems from improper installation, improper flashing of windows and doors for example.
The problems associated with housewraps and vapor barriers have developed since buildings are being made more airtight. Air tightness is good, but requires proper design, proper use of materials and proper ventilation. A house may also require installation of dehumidifier systems, air/heat exchangers along with the proper use of air and vapor barriers to prevent problems with rot and mold. It is not impossible but requires an understanding of the dynamics at work.
Or a house can be built the old way, air leaky. That of course results in enormous heating and cooling bills.
Those drafty old NE houses more often than not had low interior winter time humidity. As we seal our homes better we also retain more humidity and so it becomes even more important to prevent the moisture from coming in contact with that cold exterior wall. Water vapor will migrate quite freely with fiberglass batting insulation.
The Houston area is a hot & humid area. If an interior vapor barrier was used that's a potential problem, as mentioned above.
FWIW, one of the best products that can be used in a new build is spray on foam. A one to three inch layer of foam sprayed in the wall cavities after all electrical and plumbing has been installed seals the walls against air infiltration like nothing else can. The foam also insulates so well that the cold surface of the exterior wall is removed; the foam does not get cold enough in most cases to cause water vapor to condense. Then finish the insulation with dense pack blown cellulose.
|
|
fthurber
Member
|
# Posted: 22 Nov 2010 09:28pm
Reply
Ah very interesting and informative post. Scary about the OSB absorbing the moisture. I have seem old OSB in this area (on sheds and dog houses etc.) that just crumbles.
As far as this I am hoping that my tiny woodstove will do the trick:
Quoting: MtnDon Or a house can be built the old way, air leaky. That of course results in enormous heating and cooling bills. I do plan to use good old tar paper though...
|
|
MtnDon
Member
|
# Posted: 22 Nov 2010 09:44pm
Reply
OSB is good until it gets (too) wet. Doesn't matter much if it dries out as the swelled wood fibers do not recompress.
I prefer the old tar paper myself.
|
|
lukabrazi
Member
|
# Posted: 21 Feb 2011 09:00pm
Reply
I know this is an old post but it has lots of good info. I am building a 8x14 gable shed style building with a loft this spring. I am planning on heating it with a small marine coal stove. I'm new to building and have been spending the winter reading and learning. Vapor barriers have been the one hang up for me because there is so much conflicting info. So I live in North Central Pennsylvania and will only use the cabin maybe one weekend per month. I think that the spray in insulation is out of my cost range. Will probably use fiberglass batts or maybe Roxul but it costs a little more. Have also looked at Green Fiber which is a blown insulation but not sure if this can go into new walls or if it is only meant for attics. So should I go with tar paper on the outside and then no vapor barrier inside. I will drywall the interior walls and roof and then put a wall vent on facing sides. Do I need tar paper on the outtside if the inside is drywaled? It doesn't seem like moisture could get through this.
|
|
MtnDon
Member
|
# Posted: 21 Feb 2011 10:09pm
Reply
Exterior tar paper and interior vapor barrier or retarder are two different things.
The exterior wrap is to prevent liquid water from entering the wall from the outside. The exterior siding, stucco, brick, whatever is cosmetic, looks pretty. The tar paper or house wrap keeps the liquid water outside. As they are vapor permeable water vapor in the wall can exit to the outside. A well installed layer or tar paper or wrap will also help in stopping air infiltration.
Interior vapor barrier or retarder is to prevent or reduce the amount of water vapor that moves from the building interior into the wall. Water vapor hits the vapor barrier, which is warm like the wall and the interior and just stops there. It won't condense, but if it migrated through the wall to the cold exterior wall it can condense. Don't want that happening.
The Green Fiber cellulose can be installed in walls. The common blower that building supply places often make available free can not be used for wall installation though. That requires a different blower capable of high density installation.
|
|
lukabrazi
Member
|
# Posted: 22 Feb 2011 07:02pm
Reply
This is what I am thinking that the makeup of my walls will be. Drywall, 2x4 framing, insulation (Roxul Comfortbatt or Green Fiber), tar paper, Smartside panels. I believe that with smart side panels I do not need any sheathing. Will the painted drywall stop moisture from traveling from the interior wall? Thanks
|
|
MtnDon
Member
|
# Posted: 22 Feb 2011 07:44pm
Reply
LP makes three varieties of Smartside. Only one, the Precision series, is approved for structural use. One thing about that I don't like (personal thing) id that the structural panels, the Smartside. is only protected from the weather by a coat of paint. When the structure is sheathed with OSB or plywood that material is protected from the weather by the tar paper or house wrap as well as the cosmetic finish siding, stucco, whatever. But if it's not in a code area or is "under the radar" then it's a personal choice.
FYI, when nailing any material on as a structural member do not over drive the nails. This is common with air nailers. Crushing the wood fobers destroys the rated holding ability. I always set the air pressure a litle low and finish them off with a hammer blow.
Most oil paints would qualify, most latex would not. There are latex PVA primers that qualify as a vapor retarder when applied as directed.
|
|
bushbunkie
Member
|
# Posted: 25 Feb 2011 07:24am
Reply
Hi MtnDon...some advice? My 10 x 10 Bunkie is 14" tall....the loft is 6' at the peak with open rafters (2x4). In my zest to want to sleep over in my new bunkie last Feb.2010, I insulated with fibreglass batts and vapour barrrier...did the same in the loft. Things were great in Feb. with my propane heater (Canada -25c)...but came up in April and noticed moisture dripping from the vapour barrier in the loft...thought I had a leak!! Tore it all off and found no leak...but the 2x4 rafters were wet...even with some minor mould starting...couldn't belief how fast it all happened! Though I have a large window in the loft, I have no soffits or roof vents. My plan is to reinsulate the loft with styrofoam board...leaving air space between the foam board and roof sheathing, as well as space at the bottom and peak for air circulation...no vapour barrier. I'll probably just cover with pine tongue / groove at some point. Advice??
|
|
lukabrazi
Member
|
# Posted: 25 Feb 2011 08:18am
Reply
I didn't realize that they weren't approved for structural use. Thanks for pointing that out. I assumed they were like T1-11 panels with plywood on the back and a layer of siding on the outside. So you would recommend OSB, tar paper, then siding on the outside. On the inside am I okay with insulating between the rafters and then painted drywall?
|
|
spee
Member
|
# Posted: 25 Feb 2011 10:55am
Reply
Quoting: bushbunkie Hi MtnDon...some advice? My 10 x 10 Bunkie is 14" tall....the loft is 6' at the peak with open rafters (2x4). In my zest to want to sleep over in my new bunkie last Feb.2010, I insulated with fibreglass batts and vapour barrrier...did the same in the loft. Things were great in Feb. with my propane heater (Canada -25c)...but came up in April and noticed moisture dripping from the vapour barrier in the loft...thought I had a leak!! Tore it all off and found no leak...but the 2x4 rafters were wet...even with some minor mould starting...couldn't belief how fast it all happened! Though I have a large window in the loft, I have no soffits or roof vents. My plan is to reinsulate the loft with styrofoam board...leaving air space between the foam board and roof sheathing, as well as space at the bottom and peak for air circulation...no vapour barrier. I'll probably just cover with pine tongue / groove at some point. Advice??
Odd. I wouldnt expect you to haev moisture but hard to picture unless i see if with my own eyes. I think the styofoam board would be a good idea.
How was it using your propane heater to heat up the cabin? did you have to leave the windows open a tad because the high amounts of fumes that the propane generates? I assume a CO sensor would be a good idea for that setup also.
|
|
bushbunkie
Member
|
# Posted: 25 Feb 2011 03:12pm
Reply
Yup, Spee...moisture in the loft was a big surprise...probably I made it too air tight...and also shouldn't have listened to the goof at Home Depot who gave me the advice (no problem, buddy,,trust me it'll be fine). As far as heating, propane during the day, windows cracked..at night..2000 Watt King Silent generator powers my electric heater. I've salvaged a working vented gravity propane furnace from an RV, which I'm installing in the next month or so. (check i t out on my "100 sq. ft cabin in Southwestern Ontario" thread :) Made any decisions about your lot in BraceBridge???
|
|
MtnDon
Member
|
# Posted: 25 Feb 2011 04:09pm
Reply
bushbunkie. a lot (most?) of that moisture may have come from the non vented heater. Other sources are cooking and breathing. Can't do much about some of those. Yes, mold is all around us in the air, when it finds a spot it likes it grows quickly. If it gets too cold it stops and then starts growing again when it gets warmer. BTW, clorine bleach does not kill mold, it just bleaches it so you don't see it. There are special mold killers available.
The space under the roof needs to be vented at the bottom and top so outside air can circulate bottom to top. A one inch space is what is usually spec'd as a minimum space.
The only good sealed rafter spaces I know of are those with spray foam on the inside or those with rigid foam applied on the sheathing on the outside.
The rigid foam board (blue or pink in most places, not the white bead board) could be cut to fit between the rafters. I have done that and have sworn I will never do that again. Lots of labor and bother, IMO, especially when sealing all the edges is included. Alternatively install the foam board right over the studs from the inside. Reduces headroom a little but much easier to do. Your choice of course.
If that is done in two layers with staggered and taped/sealed seams it makes a good barrier. Some caulks "eat" foam. There are special ones that do not.
|
|
MtnDon
Member
|
# Posted: 25 Feb 2011 04:13pm
Reply
lukabrazi , one of three is structural, but I believe a better building is made by using sheathing grade osb first. Then building felt (tar paper) and then the cosmetic finish product.
The drywall can seal the interior well (vapor barrier) if two coats of a PVA based primer are used. Most latex paints do not qualify while most oil paints do, but are a pain to apply, IMO.
|
|
MtnDon
Member
|
# Posted: 25 Feb 2011 04:25pm
Reply
bushbunkie. One other detail. The roof peak has no collar ties. They can be 1x4 material cut to connect one rafter to another. Every other rafter would be fine. They also help keep the roof peak from peeling apart in conditions of high winds. The would be code required, but in non code areas it's up to the builder.
From the photos it is hard to tell how the tops of the side walls are tied together. Do your loft joists connect the wall tops? That is perfect if they are at the top of the wall. If the loft is not full length a 2x4 or bigger that connects from one side to the other will halp to keep the tops where they should be. Rafters put two forces on the side walls where they connect, straight down and horizontally outwards. A rafter tie every other rafter or every 4 feet minimum, used to be good practice. newer calls for at every rafter. Every 4 should suit your application.
|
|
bushbunkie
Member
|
# Posted: 25 Feb 2011 05:04pm
Reply
Thanks MtnDon.
The loft is 10' long and 6' wide (front entrance is open 4', clear to the peak.) The loft joists are 2x6 , at the top of the wall and run the entire length of the cabin connecting the walls. The 2x6 loft joists are mounted every 16". The actual roof is not sheathing or plywood, but made up of 14' lengths of 1 1/4 " barnboard running length ways. The extra 4' extend out to make the front porch. Do you think I still need the rafter ties? Great advice so far, by the way...thank you.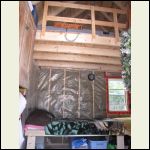 loft joists
| 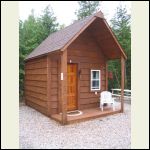 Bunkie w porch
|  |  |
|
|
MtnDon
Member
|
# Posted: 25 Feb 2011 06:15pm
Reply
If they are as described they are rafter ties and loft joists both. 
A tie across the front over the porch would help strengthen that area. Think in terms of triangles. Boards or 2x nailed together in triangles are stable. Something has to break before they shift or give way.
The boards on the roof are okay but diagonal would have been more able to resist racking. Triangles. But with lots of nails and boards snug like that you should be alright.
|
|
Erins#1Mom
|
# Posted: 25 Feb 2011 07:50pm
Reply
MtnDon, Checked out the Building Science site. Found much I can use in the future. How did you get so smart!!!!!
|
|
MtnDon
Member
|
# Posted: 25 Feb 2011 08:23pm - Edited by: MtnDon
Reply
Some schooling. Some discussion. Read a lot, both books and internet.
Building Science is an excellent site. Joseph Lstiburek is a favorite of mine. He gets the ideas across in an easy to read manner.
|
|
. 1 . 2 . >> |