|
Author |
Message |
jcaudill0034
Member
|
# Posted: 14 Jun 2015 07:53pm
Reply
I work at sawmill and can get 4x6 beams really cheap ...thoughts on them for floor and roof. maybe even walls then let it dry
|
|
AK Seabee
Member
|
# Posted: 14 Jun 2015 07:58pm
Reply
Love it
|
|
bldginsp
Member
|
# Posted: 14 Jun 2015 09:02pm
Reply
Floors and roof, good material so long as you design for the loads. Walls, 4x6 is a bit overkill but you can just design a post and beam wall instead of stud framing. Say 4x6 posts at 48" centers with a 4x6 top plate running the entire perimeter. You then have a header running the full perimeter and you don't need jack studs at windows and doors. If you have heavy snow loads this might not work. Plus, you now have the problem of lateral bracing since plywood will not span 48" for structural sheathing. You could instal 1x6 let in braces, or sheath the entire outside with 1x8 at 45 degrees like they used to, then paper and instal siding. Are you in a seismic zone, and do you get a lot of snow?
|
|
jcaudill0034
Member
|
# Posted: 14 Jun 2015 09:58pm
Reply
We get normal snow. Nothing crazy. I can get a 16 ft 4x6 for 1.50 that's just why I would use them as much as I could
|
|
bldginsp
Member
|
# Posted: 14 Jun 2015 10:38pm
Reply
That's a hell of a deal on lumber if you can buy many dozens at that price. You could just do the floor and roof with the 4x6 and frame the walls with 2x4 and 4x6 headers. You have to work lateral bracing into the design and 2x4s on 16" centers with plywood is the easiest way, and won't cost much.
|
|
Don_P
Member
|
# Posted: 14 Jun 2015 11:24pm
Reply
4x6 is a shallow timber for a joist or rafter. Depending on species and grade it is probably going to max out at about 12' spans. You'll also need to think about how to insulate a shallow roof, foam is probably the best bet at that depth. At that price I'd use the 4x6's as studs at 2' on center and call it good nailing.
bldginsp... why are you concerned about laterally bracing a wall and yet are unconcerned that it is on an unbraced foundation?
|
|
bldginsp
Member
|
# Posted: 15 Jun 2015 07:49am - Edited by: bldginsp
Reply
Don- I think an unbraced wood frame is more likely to collapse than an unbraced foundation simply because it is taller. If he's in a serious seismic zone that's different. If not, simple piers whose vertical dimension above dirt is less than (or equal to) the vertical dimension below dirt will not fall over. IMO
I recently built a 6' x 7' outhouse/bathhouse on my property so I could use my septic system. I applied for a permit, assuming that the permit would only be for plumbing since the building is less than 120 sq. ft. But because I'm in seismic and snow country they wanted a permit for the building. They allowed me to build on piers (sunk 18" into the ground) but only reluctantly. VERY reluctantly. The reason was that piers just don't work in any way in any seismic calculations. The reason they let me do it is because I brow beat them over the fact that this is a 42 square foot building, for ****** sake! I don't give a ****** if the ****** thing falls over! It's an outhouse! It's not going to kill anyone! Stop applying theory where it doesn't apply!
Now, when I poured the foundation for my 300 square foot cabin, the only rebar actually required was one #4 top and bottom, nothing else. That, to me, is stupid. I put in far more rebar. I'm going to be sleeping here, and when the quake hits I want this structure to stay on the concrete and the concrete to hold together.
As for vacation cabins or permanent residences in non-seismic areas where the piers are not tall above the dirt, it doesn't matter. The piers are not going to collapse in the dirt, but the walls could collapse on the piers. That's how I see it.
Sorry to hijack the thread. Don and I have a long running professional 'discussion' about use of piers, which I see as a healthy discussion about the limits of the use of strict engineering. Maybe it should be on a different thread, particularly if I continue to drink strong French Roast in the morning!  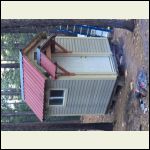 42 sq ft outhouse on deep piers
| 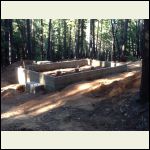 300 sq ft footing with lots of rebar
| 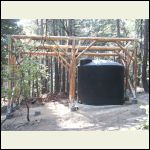 Post and beam shed on deep piers
| 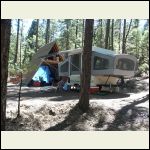 A frame on piers on grade
|
|
|
Don_P
Member
|
# Posted: 15 Jun 2015 10:36am
Reply
I don't think this is a hijack, it's all part of the discussion of the required "continuous load path".
Quoting: bldginsp The reason was that piers just don't work in any way in any seismic calculations. The reason they let me do it is because I brow beat them over the fact that this is a 42 square foot building, for ****** sake! I don't give a ****** if the ****** thing falls over! It's an outhouse! It's not going to kill anyone! Stop applying theory where it doesn't apply!
Agreed, I recieve the reports and pics after you folks shake, piers and soft stories fail regularly. They were not applying theory, that is a simple fact of life. Your arguments for using piers were based on building importance, and I agree with that. This is why we exempt small non habitable accessory structures from foundation requirements. If you live and sleep in it the importance of the building changes quite a bit.
Don't forget seismic isn't the only lateral force. Wind is the lateral force that we deal with more, and the source of uplift. It also takes down poorly built buildings.
Quoting: bldginsp simple piers whose vertical dimension above dirt is less than (or equal to) the vertical dimension below dirt will not fall over. IMO Let's think about that for a minute. When I cantilever something, the required backspan is a minimum of 2:1. If I want to extend a joist out past the support beam say 2' I need to have at least 4' inboard of the beam. All well connected and solid. The beam is the point the joist is trying to rotate about. A common misconception is that the ground surface somehow provides a hard point that a pier must rotate around. The point of rotation when a pier fails is well below grade and depends in large part on just how bad the soil or pier backfill compaction is. Those are more than likely shallow piers under your structures. The point of rotation can be from the very base of the pier, I have seen sonotubes tipped off their footings. Basically if you aren't a geotech assume the soil isn't there and brace accordingly. See attached pic from the standard.
Which is why repeatedly I've said that a better way to build on "piers" is to run the posts from the top plate of the wall down to the footings unbroken. The post is then cantilevered out of an 8' wall and is braced by the sheathed wall.
An explanation of the engineering standard related to shallow post and pier foundations is in the link below. I have the standard as well but piers are too much theory for me, a continuous foundation is stronger and avoids guessing and misunderstood theory about what shoulda worked. http://www.constructionmagnet.com/frame-building-news/shallow-post-and-pier-foundatio n-design-major-revision-of-standard-completed
The A frame foundation... we should talk about that at some point
|
|
bldginsp
Member
|
# Posted: 15 Jun 2015 03:58pm - Edited by: bldginsp
Reply
I agree with you Don that soils (generally) provide little or no resistance to rotation, and I'd go further and say that if a lateral force is applied over time the soil will move out of the way of the rotating object, witness leaning fences with solid posts. But in the case of a pier, rotation is limited by the fact that it is secured at its top to a floor diaphragm. It is not as free to pivot as a canted joist or fence post. Obviously the connection is critical. So, applying the principle of 'building importance', I think piers will hold up 'well enough' for 'buildings of lesser importance' or 'minimal threat to life health and safety'. Small cabins are dicey at best on piers alone in any area with any serious possibility of lateral force such as wind or seismic, so then the debate shifts to whether or not lesser requirements should apply in 'temporary use' buildings. Problem is that temporary becomes permanent.
In Hawaii I once saw a smaller building that had a criss-cross spread footing at the center, about 8 by 8 foot, to which the floor diaphragm was bolted. The remainder of the building, around its perimeter, was on deeper poured piers. So long as you have enough continuous footing to hold against lateral movement in both directions, the remainder of the floor can be supported against vertical loads alone. They do things differently in Hawaii.
I live in one of the lowest wind areas in the country, so I have not witnessed severe lateral effects from wind, except on 'Wizard of Oz' when Dorothy's house takes off in the twister. I feel sorry for anyone in a structure on piers when the tornado hits, or hurricane. But tornadoes and hurricanes can beat the daylights out of any structure save a concrete block wall with #5s at 12 inches both ways. But most structures affected by hurricanes are not in the eye, and don't take the full blast, but they still take far more wind than in your average storm. In places like that wind shear is a critical factor.
I also wonder about a sense of general proportion in these issues, or a sense of reverse exponential. In other words in any larger building (1000 sq ft and up) issues of wind shear and other lateral forces are critical, but in a 200 sq foot building, are the factors 1/5 less? I don't know the math, but I think they may be exponentially less, or at least disproportionately less to the difference in size of the buildings. When you look at the weight of the concrete in a 2500 sq ft house as a proportion to its wind shear or seismic lateral forces, and compare that number to the proportion of weight to lateral that the piers constitute in a 200 sq ft 'small cabin', I think the cabin may have more concrete per pound of force. I could be wrong about that, it's speculation. But if you built that 2500 sq ft house on proportionately sized pier blocks, compared to the small cabin piers, they'd be 3 foot square in the larger house. Or something like that. A hurricane would have a pretty hard time yanking a 2500 sq ft house sitting on 3 foot square piers on 8 foot centers. Would it have an equally hard time with a 200 sq ft on ordinary piers?
It costs so much more to put in a decent spread footing, and it's so much easier and faster to use piers, the practical reality is that that is what most vacation cabin builders are going to do. I think we might be best off telling them about the limitations of this very limited building method, in the hopes that they will put some thought into it and beef it up a bit, if not put in a full spread.
As for my A frame, it's a down and dirty building not expected to last very long. After 8 years it shows no evidence of problems. It's a dirt floor storage shed, meant to shed water. But, after I sell the place, if someone decides to put in a floor, insulation, woodstove, toilet, shower,..... whew- those crazy humans. They'll do anything.
|
|
leonk
Member
|
# Posted: 15 Jun 2015 05:37pm
Reply
another option is building walls in a log house fashion, with lap joint, dove tail etc I know that what I would do. is 4x6 the only size you can get..? or you're asking about rough lumber in general?
|
|
leonk
Member
|
# Posted: 15 Jun 2015 05:39pm
Reply

|
|
littlehouseontheprarie
Member
|
# Posted: 15 Jun 2015 06:17pm
Reply
Ok that is real nice.
|
|
jcaudill0034
Member
|
# Posted: 15 Jun 2015 08:25pm
Reply
4x6 Is biggest we usually saw....mostly a floor and cabinet boards
|
|
littlesalmon4
Member
|
# Posted: 16 Jun 2015 11:38am
Reply
We used stacked 6"x6" for our build. We used sill plate foam in between. I think 4"x6" would work fine, it would just take more rounds to make an 8" wall.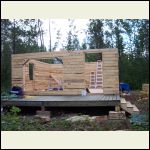 07_L_S_and_sled_pics.jpg
| 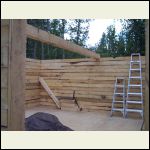 07_L_S_and_sled_pics.jpg
| 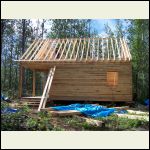 07_L_S_and_sled_pics.jpg
|  |
|
|
bldginsp
Member
|
# Posted: 16 Jun 2015 03:33pm
Reply
Nice buildings. The only problem I see with this method is that if water gets between the timbers it can't drain away. A good gasket may solve the problem, or other sealant. But this must be maintained, and if not, rot may set in. The best way to deal with moisture is to give it a slope to run away, rather than relying on a sealant to keep it out of where it cannot.
|
|
leonk
Member
|
# Posted: 16 Jun 2015 09:40pm
Reply
foam has short life span, I'd use something like jute or wool. BI, correct, however with nice overhands (like any other log bldg) very little water will get in and if it does, it will evaporate, in dry to moderate climate. I wouldn't do it in coastal Oregon.
|
|
littlesalmon4
Member
|
# Posted: 18 Jun 2015 12:48pm
Reply
First time i have ever heard of foam being accused of having a short life span. You can find that stuff lying around everywhere, never seems to break down. If it starts breaking down it would likely be caused by UV light. With this method the foam is tightly squeezed between 2 heavy beams and fastened with 12" spikes. There are no air leaks so I think water would be unlikely. We put an addition on last year and removed a 12' section. There was no sign of water between the logs. This building went up about 8 years ago.
|
|
skootamattaschmidty
Member
|
# Posted: 18 Jun 2015 01:28pm
Reply
I agree with Leonk. A large overhang will keep the walls dry that water won't be an issue.
|
|
|