|
Author |
Message |
marcwebdude
Member
|
# Posted: 3 Oct 2013 04:33pm
Reply
I have been working on a 20 x 20 cabin for a few months, getting a little more material every month around a budget, things seem to be going well and the guides I've found on this site have been very helpful. I'm not very experienced with building an entire building and am still having a bunch of fun. I have run into a small (unless I'm underestimating) issue with my foundation/floor frame.
I have been going along with steps in the proper manner, I have set out the concrete pillars and have 2 x 8's as the frame of the foundation. I have done a lot of adjusting to get the entire frame to be level. It has been sitting level for about a month and has warped a little due to the weather. I haven't really seen an issue until last night while I was installing the plywood onto the frame. it turns out that my angles aren't perfect 90 degree. I was able to adjust a little to get the plywood on 2 of the corners but I am worried about the concrete pillars moving or not lining up correctly the further along I go installing the plywood.
I would really hate to have to move everything and re-leveling, and it's not going to be cement underneath and I already have the vapor barrier in place to protect the underside of the plywood. I am doing everything I can to move the frame as necessary and understand that the foundation is the most important part. However, If my angles are slightly off, will that effect the structural integrity of the rest of the project?
I would guess that my left inside angle is around 100 degrees and my right inside angle is around 80 degrees. I could really use some more experienced feedback before I find myself having to reverse even more work before the building will be finished. I plan on continuing the plywood this Saturday, weather permitting, and hope to hear back from fellow builders by then, if possible.
Thanks for any feedback in advance and if there is any other info that I need to include, please don't hesitate to ask.
|
|
marcwebdude
Member
|
# Posted: 3 Oct 2013 05:01pm
Reply
Just as an afterthought, here are some pics to help show the progress, The only new status is the vapor barrier and the front side of the cabin has plywood down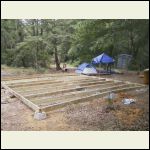 securedownload.jpg
| 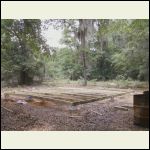 securedownload_1.j.jpg
| 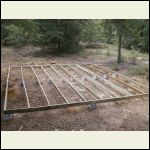 0712131303_01.jpg
|  |
|
|
PatrickH
Member
|
# Posted: 3 Oct 2013 06:31pm
Reply
A good way to check square is measure diagonally across the floor the measurement should be the same for both corners there is also the 3,4,5 meathod where you measure from 1 corner our 3' then measure out from the same corner the other direction 4' connecting the the two points should be 5' double the numbers for a bigger square. It looks like in the picture you are using 2x8x10' butted in the center? I mean this in the most helpful way but building this way it will make it very difficult if not impossible to get it square and level and the floor will be wonky.There are some better methods that will give you a better stronger floor. You will need some additional lumber of course. And if you are not flat and square to begin with (Or at least close) It will fight you the entire way to the last piece of steel roofing or asphalt shingle.
|
|
rockies
Member
|
# Posted: 3 Oct 2013 08:33pm - Edited by: rockies
Reply
It looks like your concrete blocks are resting on the ground or on some wider concrete pads? I think you are going to have major problems with this floor system down the road. For one, getting all those blocks centered and level down the middle of the cabin and keeping them that way is going to be tough, especially if it is already out of allignment. The middle picture seems to show a hump in one of the edge boards already, which will just translate all the way up the building and affect the proper installation and use of doors and windows, plus the roof rafters. I would replace all those blocks with a center beam of double or triple 2x8's glued and screwed together and have blocks under the ends and in the middle of the beam and then attach your joists into the sides of it and add joist hangers. Also, I think the spacing on your joists is a bit wide for 2x8's. It might be to code but you'll have a springy floor at that spacing. Are you putting down any weed barrier cloth and gravel under the floor to control the vegetation? The foundation must be square and level or there's no point in going further.
|
|
MtnDon
Member
|
# Posted: 3 Oct 2013 09:44pm - Edited by: MtnDon
Reply
Quoting: marcwebdude understand that the foundation is the most important part. Exactly. But this is not a good foundation. You will have no end of issues if you continue along this line. That is my opinion of course.
There is no nice way to say this; This is not a small issue. This is major. You have a problem that if left will follow you all the way up to the roof. You will run into many tasks that will be un-necessarily difficult and will probably yield what I would consider unsatisfactory results.
As was mentioned you are facing a very difficult task with trying to level that center row of deck blocks. It can be hard enough making 4 or 5 pier tops level, but 10 will make you crazy. When you add the inevitable shifting that will most likely occur to some of those you will likely have a wavy floor at the least.
PatrickH mentioned the best method to use for getting things square.
Just what is the spacing on those floor joists? The first line mentions "20 x 20". I count 9 bays across the width... if that is 20 feet there should be 10 bays if the maximum spacing of 24" on center was used. ???
In order to help better with this project it would be helpful to know where is this located? The general area. Do you have freezing weather? What type of soil? Is the lumber pictured PT wood? Will the plywood be PT? For longevity all wood used for beams should be 12" above grade and joists should be 18" above grade.
If like most of us you are faced with staying within a budget it is my opinion this will be a waste of your resources and time unless you do a more proper foundation.
The 10 foot span for the floor joist is barely within specs if we use 40 psf as the live load. Your LL will likely be less than that so the joists span should be okay. However the 2x8's that those joists attach to are undersized and poorly supported. How are the joists connected to the perimeter 2x8's? Just nails into the end grain is not very strong. This is not a plan for a cabin with a long trouble free life.
This can be salvaged if you are willing to dismantle and rebuild using a better foundation. If you have winter weather with snow looming in the near future I would recommend dismantling and storing the materials under cover until spring. That gives lots of time to learn and plan more and better and then end up with a completed project that will bring much more satisfactory results.
Sorry if this comes across as a harsh critique, but in truth as I stated earlier, I believe to continue as is will bring all sorts of construction woes and a less than happy result.
|
|
Truecabin
Member
|
# Posted: 3 Oct 2013 10:24pm
Reply
take off the plywood sheets. use a comealong and pull across the long diagonal until it's straight and square 90 and 90. maybe you will have to adjust the piers as you go then nail down some sheets to hold it square
eyeball down each joist or use a tight string you want it straight.
you will be sorry if you keep going, like Mtn said above no end to problems
starting with a square foundation is maybe the most important thing you can do and your almost skipping it nothing from here on out can be straighter than this step so make it deadnuts dont screw around
you will waste hours and hours down the road not knowing where to measure from if its not square
did you understand what i wrote about the comealong? not sure how to explain better that but its a good way if you do take it all apart then you can add a few more joists i'd go every 16 inches
|
|
rockies
Member
|
# Posted: 3 Oct 2013 10:29pm
Reply
I was going to type all that but my fingers cramped lol. This might help. http://www.countryplans.com/foundation/ you might have to use beams and then add the joists and rim boards on top of the beams to get the floor far enough off the ground. You might have to dig down and put in a concrete pier below the frost line. You could also have "Technoposts" screwed intothe ground to act as the supporting piers. Then you wouldn't need to mix concrete, but I think you should definately start over. Sorry
|
|
Truecabin
Member
|
# Posted: 4 Oct 2013 12:01am - Edited by: Truecabin
Reply
you can probably just lever it square, pound some stakes in the ground to pry against and walk the piers over with a sledgehammer but a comealong would help too if you have one
to be honest I would not build that. I think that foundations OK for a 12x12 maybe 12x16
a 20x20 is big and heavy and costly you should use a higher level of build, it would need about 5 piers under each joist to work like you started out also you should double your rim joists
you have a lot to learn but you have to get started so i think you are doing good by trying then ask on a forum but you know forums some people will tell you to build it all to code or dont even try i like people who try and ask questions i think you should downsize it to much smaller you could add on another room as your skills develop or just build your 20x20 later
|
|
marcwebdude
Member
|
# Posted: 4 Oct 2013 04:18pm
Reply
@PatrickH Thanks for the feedback and I can give the 3,4,5 a try and thus far have moved the beams to get 90 degree corners on one side and have been moving the other side to get it better in-line.
@rockies Thank you as well for the feedback, and I'll get right on the added support beams.
@MtnDon Also, thanks for the feedback and for being honest in your assessment. this was going to be a long project which would get worked on a lot during these upcoming winter months. It has snowed once in history down here, it'll be easier to get the work done with the temp lower. I hate to take it back apart, but if it's has to be done, I will try other recommendations to straighten it out first. Again thanks for your detailed feedback.
@Truecabin Last but not least, thank you as well for the valuable feedback. I would really like to fix any errors and continue with this project, since this was the plans my fiance and I have both become invested in, even if it takes several years to put up, I'd rather have to rework some of the defects instead of readjust the plans for a smaller floor-plan.
|
|
marcwebdude
Member
|
# Posted: 4 Oct 2013 04:26pm - Edited by: marcwebdude
Reply
In addition to my progress, I didn't take a look at these pictures before attaching them, there was a lot more leveling and adjusting that has been done since these pictures were taken. I will take more pictures this weekend and post them prior to continuing the work. All of my cement blocks and boards have already been reinforced and I also used 4x4 PT piers to support the beams. Everything is perfectly level and stable. The main problem was the angles were a little bit off for the corners which I thought I could remedy by lifting the outer beams off of the cement blacks and using the plywood as a straightening medium. once if screwed the plywood on both (side and front) I replace the frame onto the cement blacks and it readjusted them all to be parallel and are still level.
Yeah, in looking at these pictures, I can see why anyone who responded was disappointed, but I assure there was a lot of time I had spent adjusting and fixing the frame.
|
|
rockies
Member
|
# Posted: 4 Oct 2013 08:20pm
Reply
Well, it sounds like a lot of heartache has been avoided by doing all that work now. Whether you build to code or just try things out is a matter of personal preference, but you have to remember that "code" is the absolute minimum you are expected to do in order to not have your house collapse. A greater disappointment would be to get all the way up to the roof and discover that everything is tilting and twisting out of alignment and the cabin has become a pile of firewood. The most expensive parts to build in any house are the foundations and the roof. Your plan is a little more complex because you need that beam down the middle (or under an interior load bearing wall if you have one) so you can't just use one joist for the entire width of the cabin. If you have any interior posts you'll have to transfer that point load down to a footing block as well. Did you draw up plans for the finished cabin or are you "winging it" as you go along? If you stick with basic framing material dimensions and use off the shelf doors and windows you should end up with a nice cabin, but always make sure that loads from rafters, beams, posts and walls are transfered to the ground.
|
|
Truecabin
Member
|
# Posted: 5 Oct 2013 04:09pm
Reply
code is minimum to not fall down? i dont think so code is way way stronger than minimum if you dont understand structure you probably should build to code
|
|
rockies
Member
|
# Posted: 5 Oct 2013 06:08pm
Reply
http://www.nationalpost.com/related/topics/Mike+Holmes+Goad+building+code/3396709/sto ry.html
|
|
MtnDon
Member
|
# Posted: 5 Oct 2013 07:42pm
Reply
code is way way stronger than minimum
How would you define minimum then? Is minimum the one that shifts on its poor foundation, has the roof blow out with some 70 mph gusts, etc? Code is the minimum we can get away with and expect to NOT have to have major issues within a decade or two. There are many reasons to do better than code and few if any reasons to shortcut code.
~~~~~~
if you dont understand structure you probably should build to code
IMO, a huge percentage of DIY builders do not have a clue about structure, and most of those w/o a clue have structures that fail code in one or more areas; usually more. Lucky for them it can take a long time for any deficiencies to show up.
There is one project in particular where I witnessed structural failure before the unit was more than a dried in box on stilts. No code, no understanding of anything. A complete waste of time, effort, money and materials.
I believe in following code recommendations as a minimum. That's to protect the foolish from building dangerous structures. However, as the article posted by rockies points out there are good reasons to exceed code.
|
|
Truecabin
Member
|
# Posted: 6 Oct 2013 10:28am - Edited by: Truecabin
Reply
dont forget once those guys start coming theres no end to the problems they can find and cause and cost falling down is a small risk shutdown of the whole thing and the persons dream is a big risk
big cabin should be code small cabin it can be too much trouble i think 20x20 should be code but who knows what other trouble the inspectors will cause of course its good to build to code but dont say its the minimum because if you build to code then it falls down you get to sue the county so its overbuilt for safety from lawsuits not minimum for strength those are 2 different standards
|
|
jgiffi
Member
|
# Posted: 6 Oct 2013 12:15pm
Reply
Have you ever thought about placing 6x6 PT posts in the ground and then build your flooring off of that? It will get you off the group to help get the wood away from moist and it will allow easy access to get underneath to install installation, run water lines, etc. If set correctly a 6x6 posts will last your lifetime and you will never have to worry about it. Not sure where your frost line is where your from but just dig down below the frost line and set a bag of cement and set the post ontop and level and backfill and your done. It looks like you already constructed your deck but it may be worth dismantling now before you construct walls and a roof because if you get any kind of shifting at a later point it will be x10 more difficult and expensive to repair at that point. Thats just my opinion there are a million different ways to do something and they are all correct. Just a method that I have used in the past and had good success with. What are you going to be constructing your walls out of 2x4 or 2x6? One level or two? Are you using trusses or are you making your own rafters? It wouldn't hurt to invent in a tarp to cover your material and your deck with to protect it from the elements while your constructing.
|
|
rockies
Member
|
# Posted: 6 Oct 2013 06:17pm
Reply
The conversation got a little side-tracked from this poor man's initial question about what to do about his foundations, and yet I think the discussions that followed goes to the heart of any person's cabin build. "Falling down" is NOT a small risk compared to having a building inspector find a lot of problems and shutting down the site. If an inspector can find enough wrong to shut down a project you'll KNOW it will eventually fall down. If you've got yourself and your family inside this thing and a severe storm dumps a ton of snow on the roof and it collapses or a strong wind blows it apart you'll be far worse off than having to deal with inspectors. Code is very simple to apply to a building whether it is big or small. Joists attach to beams and posts to roofs and floors in only so many ways, and the experts have tested them to see how much or little you need in order not to have building failure, and that is usually the minimum needed. My concern is that people think that by going out into the countryside where they can't see another human being for miles around lets them think that codes and regulations don't really apply to them anymore and they can build their cabin any way they want. I would think that saving your cabin from collapse (and your time and money as well), is worth building to code and perhaps exceeding it, but find out what code is! We're lucky because the cabin's usually ARE small and therefore not too complicated, but build it right, build it waterproof and build it solid and your grandkids will be enjoying it one day rather than tossing it into a bonfire after 20 years because it rotted out and fell over.
|
|
marcwebdude
Member
|
# Posted: 6 Oct 2013 06:21pm
Reply
I had moved my joists to be 16" inside and turns out I only had to shift one sided of the perimeter of the frame, I just used a hoist and pulled til it was at a steady 90 degree and now all of the plywood is straight and lines up from front to back. I had plans, but now that the hand's on application is underway, I've had to adjust to make it work. So in a sense I'm kinda wingin it, and I keep referring to the instructions on this site to move forward. I ended up getting some 3.25 mil plastic to cover the whole thing since it has rained most of the weekend and I didn't really see a reason to take updated pics when it's all covered in plastic, I think I'm in good shape thus far, just a small issue with angles which I was able fix pretty quickly, maybe lost about 3-4 hours of rework. We don't plan on installing any piping for water underneath, but even if we do I still have some room underneath the subfloor, short side about 4 inches from fram bottom to the ground and about 12 on the high side. We are only making this a simple one room one story and I had planned on trusses, but I'm kinda more pulling for the "column" idea for roofing support.
|
|
toyota_mdt_tech
Member
|
# Posted: 6 Oct 2013 09:43pm - Edited by: toyota_mdt_tech
Reply
Quoting: PatrickH And if you are not flat and square to begin with (Or at least close) It will fight you the entire way to the last piece of steel roofing or asphalt shingle.
This is the absolute most important thing. The floor must be perfectly level, (plumb, level and square) the corners at right angles (perfect) and the walls straight true and square. If its not, the problem is compounded many times over as you move forward, amplifying with each stage, ie framing, then sheeting, then finish...). Then the building progression slows to a miserable pace. You can not use sheeting without wonky cuts and its even worse (10 fold) when it comes time to trim it out. If the floor is not perfect, go back and re do it. Trust me, its the easy part, if you advance, its much tougher all the way thought the process and gets worse as you advance.
Buy one of those long 6 foot levels and dont even toss it on the floor or ground, always gently set it down.
I still think the footing is going to be questionable. Dig in, install huge post on a concrete pad in the ground, gravel under it, lacked down. Poke them upward, do 3 rows of 6 post, 4 feet between the post, then run a large beam over the top of them that can handle the 4 foot span. One large beam across the back, another dead center and one more in the front. Gusset the post with blocks and huge lag bolts to keep it from wobbling/shifting. As other said, get some elevation, you need to be able to access underneath and then put a nice vapor barrier on the underside of the flooring.
Thanks for not taking the advice personally as an attack, but as help.
If this was my project, I'd disassemble what you have, lay it all in a nice pile, cover it up and start digging for your foundation post. Be a great project over the winter, especially if you dont get to freezing. I think you are in a hurry to build and rushing through the most important part of the build which you will regret later.
|
|
marcwebdude
Member
|
# Posted: 8 Oct 2013 09:39am
Reply
@toyota_mdt_tech Thanks for the feedback, but as I stated in my last post, I had already done the leveling, and now I'm sitting on a good square angle on all four corners. I already had a long level, it's not a 6 ft level, but it's a 4 ft level and I've made sure everything is always level through each step thus far in the build.
|
|
toyota_mdt_tech
Member
|
# Posted: 8 Oct 2013 10:43am
Reply
My concenrn now would be the footings or pads. They appear to be just on topsoil. But if its resolved and wont change position, then the decision to move on it entirely yours. Keep us posted on progress and post any questions if you have them.
Keep it all level, plumb and square as you proceed. If its not, fix it right away before advancing. Save you lots of trouble.
Good luck and have fun . 
|
|
marcwebdude
Member
|
# Posted: 10 Oct 2013 09:44am - Edited by: marcwebdude
Reply
Ok will do, thank you for the support, I understand the need to keep it level, I've spent a large majority of the time leveling and making sure it's perfect. Also only 3 of the pads are actually on the top soil, the rest of the 15 are buried and are secured. I've let them really sink in over the past few months and the rain has just help secure them even more. I had the squared issue that I've been able to resolve, now I just have to wait to catch up on funds to move on to the next step. The plywood was by far the most expensive step thus far.
|
|
rockies
Member
|
# Posted: 11 Oct 2013 08:24pm
Reply
Hey. What is the frost line below ground in your area? Do your buried footings go beneath it? If the rain has caused the posts to "sink in and secure them even more" is there any concern that the ground water could freeze around the posts and heave them out of level? Since we are getting so close to winter, are you going to continue with the build now or wait until spring? If you wait a tarp should keep the framework safe (snow isn't usually a problem until it melts and starts to wet the wood) so in the spring you'll definately notice if there are any foundation issues. Hope there aren't any.
|
|
MtnDon
Member
|
# Posted: 11 Oct 2013 10:22pm
Reply
Quoting: marcwebdude I've let them really sink in over the past few months and the rain has just help secure them even more.
They've sunk/moved on their own? If so why should they stop moving now?
|
|
marcwebdude
Member
|
# Posted: 14 Oct 2013 02:47pm
Reply
@MtnDon I had originally dug a few inches down and put the pads down and slowly built the perimeter and then each joist and made sure everything was level as I moved along. As time has moved on the pads have gotten rained on and have readjusted from the weight, but just enough to make up for the loosened soil. I had also buried them with the topsoil that was there beforehand and the rain has helped bury them more naturally. but It has still been just as level and the same height for about months. I wasn't happy with the plywood, and I recently removed all of it to add a few more joists and reduce the spacing from 24" to 16".
|
|
|