|
Author |
Message |
Livinlife4jc
Member
|
# Posted: 19 Aug 2013 12:19am
Reply
Hi all, building my first home- 16x32 downstairs, 18'x32' upstairs sitting on 6x6 pine open beam. The gambrel roof upstairs has turned into a nighmare and I'm looking for input. It's a yearound home, and we have a pretty reasonable snow load, even though with the pitches most of the snow will just slide right off. I'm needing 10"-12" of depth in the trusses for insulation, wiring and venting. The original plan was picture 1 done instead in a 2"x12" and just plated together and bolted at the top join, but now we're facing something like picture number 2 with a central beam and hangers at double the original price- Nearly $5000 and a 10th of my overall budget. It might break the bank for me and I'm wondering if anyone has any input about saving all this headache with extra beams and hangers.
|
|
razmichael
Member
|
# Posted: 19 Aug 2013 09:52am - Edited by: razmichael
Reply
looks like you require engineering approval for the Gambrel roof? Much more difficult to get than standard trusses. Here is a pair of connected articles on gambrel rafters: Part 1 Part2
In my case I went with a structural LVL beam (as I have an open concept thus no ceiling joists or rafter ties to hold the walls from pushing out) and made my own rafters using 3/4" plywood gussets. These are hung from the beam and also strapped across the top. If you have ceiling ties then you could likely do this without the beam although it has some advantages and was actually cheaper than I suspected originally. As I will be spray foaming between the rafters, I only used 2x8's. Given the limited span of 16' all the way across and with a metal roof this was unofficially deemed as more than suitable for the snow load- but I did not need to have it signed off by an engineer. A real pain to build but provide so much extra headroom in the lofts.
By the way - take all of this with a grain of salt as I am no building expert nor engineer.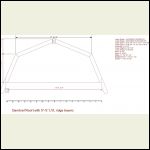 Rafter Overview
| 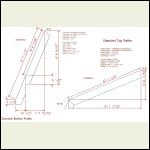 Rafter Details
| 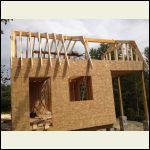 Rafters going up
| 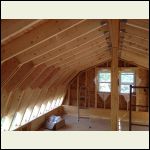 Inside view
|
|
|
MtnDon
Member
|
# Posted: 19 Aug 2013 01:39pm - Edited by: MtnDon
Reply
The question that is not directly answered is regarding what permitting and inspection process in in effect where this is to be built. Along with razmichael I assume there is code enforcement because of the change from one design to another.
I see the first design was not approved for residential use but the second is. Is that difference a structural reason or an energy code reason? The first would be difficult to get through energy code unless the members were 2x12, IMO. However, would the first design be approved if you changed to building with external sheet foam insulation on the roof?
The layer order is truss, then structural sheathing, then foam in layers with seams staggered, furring strips screwed through the foam to the trusses, to hold down the insulation and provide a drainage plane (run vertically), then another layer of sheathing and then the final roofing material (shingles/metal). No ventilation is required when done right.
|
|
MtnDon
Member
|
# Posted: 19 Aug 2013 01:48pm
Reply
Or does the original truss design not resolve the horizontal outward forces sufficiently for a residence?
In that case following razmichaels lead with a load bearing ridge beam may be an acceptable path. The issue then becomes one of getting home built rafters like razmichaels approved by the building department, assuming there is one. That might be difficult, may need an engineer to approve the design.
|
|
|