|
Author |
Message |
Sambo
Member
|
# Posted: 13 Aug 2013 08:36pm
Reply Quote
Hi there,
I'm glad that I found this place and hope to learn and later maybe share a few things. That is provided that I don't wimp out on the project that I've gotten myself in to.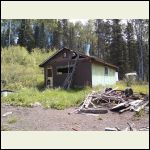 IMG_20130811_130650..jpg
| 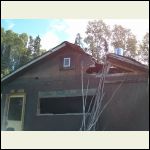 IMG_20130811_130708..jpg
| 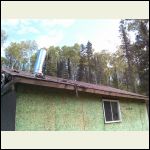 IMG_20130811_130735..jpg
| 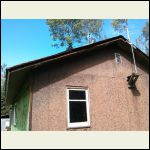 IMG_20130811_130807..jpg
|
|
|
Sambo
Member
|
# Posted: 13 Aug 2013 08:44pm - Edited by: Sambo
Reply Quote
I need to patch the roof before winter. I've never done this before.
Simply put, do I repair the trusses, lay down new chipboard, tar paper, and shingle away? I'll pull out the pipe for now as well.
Then board up the windows etc.? If I board up the windows should I have a couple vents to keep the interior environment relative to the outside environment? Should be seeing up to minus 30F days at some points.
Over this winter I'll make a plan as to what to do with this cabin next spring.
Frame and electrical is pretty decent. Insulation and interior needs gutted. Cabin needs re-leveled or even moved as it's situated over a spring of some sort.
|
|
OwenChristensen
Member
|
# Posted: 13 Aug 2013 09:14pm
Reply Quote
Welcome, When you finish that job , you'll be a pro.
|
|
Sambo
Member
|
# Posted: 13 Aug 2013 09:37pm
Reply Quote
Haha!
Some say tear it down, and others say keep it. The frame does seem solid, and there's extensive electrical connected to a 200 amp breaker box w/ ground plates.
I would rather the hassle than perhaps paying more if I started from scratch. It's a 27x20 cabin.
|
|
Borrego
Member
|
# Posted: 13 Aug 2013 09:55pm
Reply Quote
Have fun! I'd check that sheathing for mildew/mold, it may have to be replaced. Let us know if ya need any advice....
|
|
Just
Member
|
# Posted: 13 Aug 2013 09:59pm
Reply Quote
as long as the footings are solid and level I would say fix what,s there that way there are no permit issues . looks like a 4\12 roof should be easy to fix. welcome aboard. lots of help here ,take lots of pics. good luck .
|
|
Sambo
Member
|
# Posted: 14 Aug 2013 01:03am - Edited by: Sambo
Reply Quote
Quoting: Borrego I'd check that sheathing for mildew/mold, it may have to be replaced.
Now you got me thinking.... patch for the winter or redo the entire roof?
Rodents got in to the roof so I'm assuming that everything needs gutting. Could I redo the roof and gut the ceiling and insulation from the inside afterwards? Or is it ideal to re-roof after I've cleaned house down to the frame?
Quoting: Just as long as the footings are solid and level I would say fix what,s there that way there are no permit issues .
The previous owner was going to jack it and put two beams the length of the cabin under it, but he never got around to it. Another person claims that the floor is "soft." Having no experience, when I go inside it feels pretty hard to me. Needless to say I'm going to assume it needs to be leveled and fortified some. Possibly moved as there are signs of a spring coming up through the earth to one side. By spring I mean some wet spots
|
|
PatrickH
Member
|
# Posted: 14 Aug 2013 07:24am
Reply Quote
Is Hantavirus a concern? if rodents where present
|
|
CabinBuilder
Admin
|
# Posted: 14 Aug 2013 12:21pm - Edited by: CabinBuilder
Reply Quote
I agree with keeping in mind the permit concern. Depending on rules in your municipality, you are likely to go through the permit process if you choose to construct the new cabin.
|
|
gunslinger22
Member
|
# Posted: 14 Aug 2013 12:52pm - Edited by: gunslinger22
Reply Quote
I'd say buy a couple air jacks or hydraulic ones, 8 ton or something and gently lift it up. If the floor joists are in good shape try doubling up a 2x10 and using it to span between or more joists and lap over the rim joist. Place the jack in the middle of your 2x10 so you're spreading the pressure out over all 3 or so joists and the edge of the 2x10s are catching the rim joist. this is assuming you have room to get that stuff under there of course. try lifting at two corners at once to prevent twisting and then do the other two corners. Work your way back and forth between the ends of the cabin and keep blocking it solidly and adding blocking under your jacks so you can get more height. Try get the thing up 3 feet or something and then maybe you could form up some 2x6's into concrete forms like i did on mine. 3'x3' and put them under each corner and a couple in the middle of your long span. Pound stakes beside the forms and put screws in to level your forms, or you can use blocking but pegs are better. fill them with concrete mixed in a wheel barrow and screed the tops off level with a two by four. once the concrete is set Use a laser level to find a good height for the building to sit at and if each pad is at a different height you just figure out what length of post is needed at each pad so that the tops of all your posts are level with each other. Cut 6x6 treated posts for each height necessary at each pad.Since you wont be able to pour a pad under the middle of the cabin realistically you should run some hefty beams between your posts perpendicular to the length of the cabin, and notch the ends of the beams so that more beams can share the tops of the posts and span the posts parallel to the length of the cabin. If you dont have somewhere you can get long beams then glue and screw 3 2x8's together to make beams. Use PL400 or similar and lots of screws and make sure that each run of 2x8 laps the joints of the other runs by at least 6 feet or whatever works best for the length of your building. Just make sure it is REALLY well blocked before crawling under there to set a beam on your posts. Then get some strong metal straps and wrap them from one side of the post, up and over the beam and down the other side of the post with a lot of heavy joist hanger nails pounded in through the straps. Theres also the option of using big lags and bolting metal plates where the beams meet the posts. Do a bunch of braces between your posts, making sure they posts are all level and then you should be able to lower the building onto the beams. Try get the bracing to butt up against each other piece so that not only are nails holding it but it is transferring load from the beam down to the pads. ANd dont use screws except maybe to hold the bracing for nailing, as big spikes have much higher shear strength than normal deck screws. My pictures on the thread about google sketchup might help you a bit, but right now i dont have the blocks in the pictures that will transfer the brace strength to my pads. Once you have set the building back down tie the buildings floor to the beams with metal strapping or better yet some drilled metal plates with big ass lags crews let it sit for a couple weeks and then check your levels again. Use a transit or laser level for this as checking level on a warped floor doesnt tell you much. Get some metal or good cedar shims and go around shimming any that are low, up to the level of your highest point. Also remember to get some copper wood preservative and paint any of your cutoff edges on your treated posts and since concrete can eat away at your posts make sure you put something between your posts and the concrete such as rolled roofing or pieces of asphalt shingle. Paint any weather exposed wood on your foundation with the copper preservative too.
I'm not sure if this makes sense but feel free to ask lots of questions, it isnt an expensive fix for the foundation and i dont think its as difficult as it sounds. If you want i could do up some drawings when i have time.
As far as fixing the roof is concerned I'd first check that your wall studs and top and bottom plate of your walls are in good shape.
If they are then go through and replace any thing in the roof that needs replacing, and then put sheet metal roofing on. If its gonna be cold there then maybe consider a ridge vent and good metal soffit. And when you insulate the roof put cardboard insulation stops above your soffit to prevent the insulation from sliding down over the tops of your soffit vents. Gable vents would help too.
Might as well wrap the place in house wrap too, even the bottom if youre gonna insulate the floor, tyvek is cheap and works wonders at keeping your walls dry.
Good luck! it'll be worth it!
|
|
gunslinger22
Member
|
# Posted: 14 Aug 2013 12:57pm
Reply Quote
As for soffit you could make your own with 1x6's and metal screen but its a lot easier and quicker to use metal soffit. And I just realized that with the type of truss you have there the insulation stops arent really needed i dont think, unless im miss reading the picture.
Literally none of this might work since i'm going on just a few pics and i might be a dullard. 
|
|
gunslinger22
Member
|
# Posted: 14 Aug 2013 01:00pm
Reply Quote
One more thing, the main point of lifting it up is so air can get under there and dry things out, once it's dry you could put some skirting on with a few vents in it and maybe lay some plastic down to prevent moisture coming up from the dirt, and blammo, set for life. Or at least the life of the cabin ;)
|
|
Sambo
Member
|
# Posted: 14 Aug 2013 01:06pm
Reply Quote
Wow thanks for the input. I'll read more in detail over the next little while and look up some of the jargon as well before asking anymore questions. Appreciate it 
|
|
Sambo
Member
|
# Posted: 5 Dec 2013 11:41pm - Edited by: Sambo
Reply Quote
Well I managed to patch up the roof and seal things up. Also gutted all of the interior siding and insulation. I would of loved to have raised it if even temporarily for the winter, but I'm just a bit slow in this dept.
|
|
Sambo
Member
|
# Posted: 5 Dec 2013 11:49pm - Edited by: Sambo
Reply Quote
There appears to be three log beams running length wise under the joists. The log beam to the far left is 90% buried. I thought about freeing up these timbers completely off the joists and raising the cabin without them, but it's been suggested otherwise. Dig out around the timber and leave them on at least until it's off the ground.
I would like to turn the roof in to a split roof loft. With the left side sloped substantially higher than the right. Could anyone suggest some options for getting help with plans for this? There will be windows and possibly a balcony involved
|
|
rockies
Member
|
# Posted: 6 Dec 2013 04:37pm - Edited by: rockies
Reply Quote
When you redo the roof in the spring I would use 5/8 tongue and groove plywood, not chipboard. Since you have patched it for the winter it should prevent water from causing any more damage when the snow melts, but tear off the old shingles and sheathing and inspect the rafters for rot (or they may be undersized) before doing a new roof. You'll have to consult an engineer if you're going to change the roof radically with different ridge beam heights and a loft. Perhaps increase the pitch to a 8:12 (or higher) and add a dormer for windows? Since all the interior wall surfaces and insulation is gone now, you shouldn't need to leave any openings for air. The cabin is probably drafty enough as it is. The log beams are probably unlevel, so you might jack the cabin up and put it on a new pier foundation. Screw in metal posts could be done. No digging, concrete or back filling. Just have them installed and then put on your perimeter beams and put the cabin on top. http://www.technometalpostbc.com/
|
|
Sambo
Member
|
# Posted: 6 Dec 2013 05:50pm - Edited by: Sambo
Reply Quote
I've heard of helical posts, and that they are especially great for areas with lots of clay (not my area), but I've also heard it's a pretty steep investment. I need to do everything at the near cheapest solution. Even this split roof idea I had...it's beautiful what I had in mind, but it's tedious and lavish. It's probably best to increase the pitch like you said, and try to work within the gables.
What do you know about pricing on helical posts? How many would you need for a 20x27 ft structure?
|
|
turkeyhunter
Member
|
# Posted: 6 Dec 2013 06:48pm
Reply Quote
Sambo--looks that was a JOB gutting it...
what was the story on that cabin?? was it a hunting camp??
|
|
Sambo
Member
|
# Posted: 6 Dec 2013 07:09pm - Edited by: Sambo
Reply Quote
I believe it was erected about 25 years ago, and someone lived in it for about 15 years. Then for the previous owner it was a sort of hunt camp away from the wife camp. I believe he wasn't occupying it much as he was worried about the mold and rodents. He put the tree through the roof last spring.
Gutting it was interesting. I don't think the rodents did as much damage s they could of, the mold was bad in some areas but could have been worse, and I found three concentrated patches of ants at work, but the lumber seems unaffected. Found an old 22 cooey between the studs as well 
I was up in the ceiling between the trusses in 42C (with humidex) heat, stomping out the ceiling. It was so hot I had to pay real good attention to my energy levels, and how far I had to move to get back down to the ground. It sure beat an overhead take down, and not having debris falling all over me.
|
|
redlandfd
Member
|
# Posted: 8 Dec 2013 10:47am
Reply Quote
If its been sitting on foundation logs for 20+ years and its worked, I'd think twice about raising it. If the logs, sill and joists are still solid, then I'd just leave it. As for the spring or seep, you might be able to channel it away from the house or dig it out and seal it off (although it will pop up again somewhere). If you are still going to raise it you could use concrete block piers, but shovel digging the footing for them would be a pain..but cheap.
Definitely strip the chipboard from the roof and go metal, either on decking or use nailer boards..again cheaper.
That's a heck of a project, but its do-able, stay positive!
|
|
Sambo
Member
|
# Posted: 8 Dec 2013 04:28pm - Edited by: Sambo
Reply Quote
Thanks. I'm totally down for it 
I'm not versed in all of the house construction jargon, but I'm not sure there are sills on this cabin. It looks like just floor and rim joists on timbers
|
|
rockies
Member
|
# Posted: 9 Dec 2013 05:20pm
Reply Quote
I think putting a metal screw pile in the ground costs about $150-$250 per pile, which isn't too bad considering that the company can put in the whole foundation in about 2 hours with a special machine, so there's no digging, formwork, metal rebar or concrete mixing (plus the labor involved if you hire someone). You also don't have to wait for any concrete to set up, just weld a bracket on the top of each pile to attach your rim joists to. The company will calculate where and how many piles you need and provide strength bearing info for the building inspector. I would also check your current inground beams for termite damage. We don't get termites up here in Canada much, but it can happen.
|
|
|