|
Author |
Message |
guuby
Member
|
# Posted: 10 Jan 2013 07:56pm
Reply
Hey guys Im gonna be blunt...I appreciate all the help but I need a clear cut-to the point-detailed-step by step answer on the process of putting on a metal roof on a 16x16 cabin in southern Indiana.
the rafters are set and ready to go, the next step is........
Thanks
|
|
guuby
Member
|
# Posted: 10 Jan 2013 08:07pm
Reply
here is what I have so far, in this order...OSB, felt paper, then metal roof. How thick OSB? Should I use foam sheets instead of felt? If so how thick? I do not plan on having a ceiling just leaving it open, does this change anything? Only climate control will be a stove in the winter, no AC.
Thanks
|
|
Sustainusfarm
Member
|
# Posted: 10 Jan 2013 08:17pm
Reply
I would use T-111 plywood with the grooves cut in and facing the inside so it looks finished on the inside then build up from there....the rest someone else will have to describe to you...sorry...take pics as you go so we can all learn the process! 
|
|
MtnDon
Member
|
# Posted: 10 Jan 2013 08:19pm
Reply
Quoting: guuby I do not plan on having a ceiling just leaving it open,
Does that mean you are not interested in insulating the roof?
|
|
Anonymous
|
# Posted: 10 Jan 2013 08:27pm
Reply
OSB, Felt paper and metal roof. I would use 7/16 OSB. You can put the insulation between your rafters and then a vapor barrier after that. Should be good to go. 
|
|
MJW
Member
|
# Posted: 10 Jan 2013 08:35pm
Reply
Went to a propane place last week to get a bottle filled for the RV and the inside of this guys building/office gave me an idea for how I want to finish our place.
Directly on top of the rafters, this guy had taken cabinet grade plywood and had a cabinet shop mill it to give it the look of 1 x 6s. He then installed it directly on top of the rafters, added a layer of 2 inch foam insulation topped by OSB then felt and the roof metal.
The inside plywood and rafters were sprayed with a poly/stain and they looked fantastic.
I took a ton of pictures (which unfortunately my wife is visiting her parents and I don't have the camera to show you) and I think we are going to do this exact thing.
|
|
guuby
Member
|
# Posted: 10 Jan 2013 09:07pm
Reply
Thanks gentlemen, I now have a plan...OSB, felt, then metal roof. MtnDon, as of now I do not plan on putting any insulation inside the cabin, just open rafters seeing the bottom of the decking.
Please tell me OSB, felt, then metal will still work and is all I need
|
|
MtnDon
Member
|
# Posted: 10 Jan 2013 09:28pm - Edited by: MtnDon
Reply
Quoting: guuby Please tell me OSB, felt, then metal will still work and is all I need
It will work. But if I can editorialize, personally I would not use OSB exposed like that unless the structure was a shed, garage, barn.... I would use plywood with the good/best side down. Mostly that is because OSB looks ugly and if it is decided to apply a finish of some kind, it still looks ugly. Been there, done that. But as far as structure goes it will work.
One more thought on this. It will look a whole lot better if all the roofing screws are aligned with the rafters. That can be very difficult as the roofing panel widths and rafter locations never quite match up perfectly with the spots you need to place the screws. It's just that the protruding screws add to the ugly look and the OSB will flake away in some places where the screw penetrates. Again, aesthetics more than anything; it will still be a good rain, snow and all round weather barrier. Been there, done that too.
|
|
MtnDon
Member
|
# Posted: 10 Jan 2013 09:36pm - Edited by: MtnDon
Reply
7/16 will be fine as most 7/16 will be span rated to 24" OC. You might verify your materials. 5/8 will give a more solid roof, but 7/16 meets code. I doubt you could tell any difference from looking up at the underside.
Sheet goods are usually installed with an 1/8 gap, as per the APA recommendations. It might look funny from below... "eye of the beholder" stuff again. Tight edge butting is not recommended by the APA because of the edges becoming compressed/raised under conditions of increased humidity. Spacing is not a code requirement though.
|
|
Borrego
Member
|
# Posted: 10 Jan 2013 10:19pm
Reply
Quoting: Sustainusfarm I would use T-111 plywood with the grooves cut in and facing the inside so it looks finished on the inside
Yes! Good idea... I've done this.. And I would add an insulative barrier as well. So.... T-111 (upside down), rigid foam insulation, 1/2" CDX, felt paper, then metal roofing.
|
|
toyota_mdt_tech
Member
|
# Posted: 10 Jan 2013 11:33pm - Edited by: toyota_mdt_tech
Reply
Quoting: guuby Hey guys Im gonna be blunt...I appreciate all the help but I need a clear cut-to the point-detailed-step by step answer on the process of putting on a metal roof on a 16x16 cabin in southern Indiana. the rafters are set and ready to go, the next step is........ Sheeting over the rafters, felt paper (I'd use 30lb stuff) then metal roof over that. Done!
I'm with Mt Don on the "no OSB". I didnt use a single piece of OSB. I used all genuine plywood.
|
|
mgc
Member
|
# Posted: 11 Jan 2013 05:54am
Reply
No OSB, eventually it will slowly delaminate from the moisture it absorbs inside the cabin. Sweaty windows inside is moisture, add heat and it rises to roof level where it get absorbed into OSB. The edges of the little strands start to rise and then spreads. painting might slow it from starting, but it will happen. Plywood, heavy felt, metal roof. Decking and rafters are the foundation of the roof and just like the cabins foundation you want it to be sound for years to come. OSB costs less because you get less, please don't use OSB, you will not like it in 5 years. Mtn Don & TmT are right on.
|
|
Martian
Member
|
# Posted: 11 Jan 2013 08:04am
Reply
If you can afford it, put down plywood, run your purlings (either 1X or 2X material), fill the space between the purlings with foil-backed styrofoam, apply another layer of plywood, lay out the felt paper, and then screw down the metal.
You'll end up with a roof that will last a lifetime, provide a little insulation, and be relatively quiet.
Tom
|
|
MJW
Member
|
# Posted: 11 Jan 2013 08:00pm
Reply
Here are a few of the pictures of that ceiling I referenced earlier.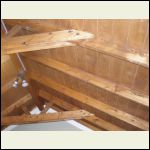 P1070001.JPG
| 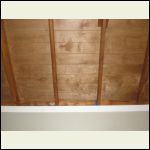 P1070002.JPG
| 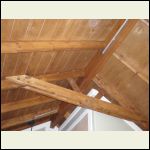 P1070003.JPG
| 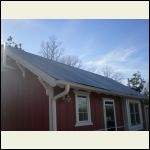 P1070007.JPG
|
|
|
guuby
Member
|
# Posted: 12 Jan 2013 07:09pm
Reply
thanks...posted this ? on another thread but here it is again
Obviously roof wont be as strong plus wont look very good but would this technically work? No plywood or OSB, but attaching 1" foam insulation sheets directly to furring strips then put metal on top of that? Would putting felt paper on foam matter at all?
Thoughts?
|
|
bldginsp
|
# Posted: 13 Jan 2013 07:06pm
Reply
Any roof construction needs to take into consideration issues of moisture and adequate ventilation, if the space inside is going to be heated.
Heated air holds more moisture than cold air. Inside conditioned (heated) space gets moisture from showers, cooking, and people breathing. Then, the warm moist air goes up. If it hits a cold surface, the moisture condenses, and the moisture can then cause mold. This is a big issue in the building industry and has caused a lot of grief.
If you put plywood/OSB, paper, roofing with no insulation, and then heat the space in cold weather, you will get condensation on the underside of the roof deck. Putting plywood, vapor barrier (poly sheet), rigid foam insulation, plywood again, paper, then roofing is a good solution. Because the visible underside of the roof deck is inside the insulated envelope, it will not be as cold as the outside, and will not cause moisture to condense (as much). The poly vapor barrier inhibits (doesn't prevent) moist air from getting to or above the insulation where it will hit cold surfaces and condense.
The above describes a 'vaulted' or 'cathedral' ceiling, where there is no attic. The situation is easier if you have a ceiling, attic, and then roof. Place the insulation above the ceiling in the joists, and then ventilate the attic space. Any moist air that makes it into the attic and condenses will have a large body of ventilated air to carry it away.
This is a little complicated, but here's how I plan to do my vaulted ceiling, from the rafters up: -Site cut timbers for rafters, exposed on the inside. -Redwood T+G 1x8 finish material on the rafters -Poly vapor barrier on the finish material -3/8 plywood on the poly for shear (structural strength requirements) -6-1/2" polyisocyanurate rigid foam insulation, R-40 -1x4 sleepers on top of the foam, allowing an air flow space above the foam for any developed moisture to dissipate. Requires eave vents for air to enter, and a ridge vent for air to leave. Ventilated space must have cross ventilation. -1/2" plywood on top of the sleepers, then paper and metal roofing.
This is a more extreme solution, having a ventilated air space above the rigid foam insulation, but is the best insurance. My cabin is in snow country, and will be thoroughly insulated and heated, with a shower and cooking, so there will be considerable moisture.
If you never heat the space the whole issue is irrelevant.
|
|
Deerfan
Member
|
# Posted: 13 Jan 2013 11:16pm
Reply
Great post, bldginsp!
|
|
bldginsp
|
# Posted: 14 Jan 2013 08:38am
Reply
Thanks Deerfan. This is a major issue in the building industry which is why I've studied it. On further reflection here are a few more relevant points-
-In my experience mold and ventilation is a bit mysterious. I've seen situations that should have had moisture problems and didn't, and situtions that seemed less likely too which did. So, point 2:
-Could be that moisture ventilation is really only important in spaces that are lived in all the time. If you only go to your cabin a few times in the winter for a week or so, and you have no insulation, I wonder if you will accumulate enough moisture to cause a problem. The main problem will be that you will be very uncomfortable with no insulation, despite the woodstove.
But then when you do insulate it pays to think about ventilation. Worst case scenario is fiberglass bats of insulation inside rafter bays, sealed above by roofing and below by finish material (sheetrock, nice plywood, whatever) with no ventilation. This is a scenario for mold throughout the unventilated bay.
|
|
rayyy
Member
|
# Posted: 14 Jan 2013 06:59pm
Reply
Here is another way you can look at it,too.The part of your cabin you will be in is a 6 sided box.Those are the 4 wall's,ceiling and floor.That's what you insulate and vapor barrier.The roof's job is to just keep the rain and snow off the insulated box.The roof is vented to the out side,it will just maintain what ever tempeture that is outdoors.If the roof is below freezing,you don't want any heat from the box to get up there at it.All my roof's are steel on purlings.Purlings are just 2x4's nailed across the rafters.No plywood or OSB.No felt.If your gonna heat it,you got to let the metal roof material be outside in the cold,well away from the heated box.
|
|
Rossman
|
# Posted: 14 Jan 2013 07:16pm
Reply
MJW - those pics are great, love those beams!
|
|
Deerfan
Member
|
# Posted: 14 Jan 2013 07:43pm
Reply
Rayyy, this is exactly the way we did the roof on our cabin.
|
|
bldginsp
|
# Posted: 15 Jan 2013 01:47pm
Reply
Rayyy-
Very good summary of the situation. Here are a couple more wrinkles:
Some people have put vapor barriers on exterior walls where there is a shower wall against the inside of the exterior wall, thinking they want to keep the moisture from the shower out of the insulated wall where it will condense. But the opposite happened. No vapor barrier is 100%, so water got to the other side of the vapor barrier, then the vapor barrier inhibited the evaporation and release of the water, promoting mold. So, I've heard the suggestion that you do not use paper backed insulation in an exterior wall with a shower against it, and no vapor barrier (poly) against the inside of the studs, so that moisture in the stud bay can dissipate and release. Tyvek house wrap allows vapor moisture to pass through and dissipate. So does tar paper. I don't really understand the advantages of Tyvek over good old tar paper.
The question arises- should you ventilate walls and floors just like ceilings and roofs. Apparently roofs are more important because hot air goes up so that's where most of the moisture gets applied. But mold in walls and floors is a potential problem too. The tendency in the building industry is to make buildings more 'tight' for energy efficiency, but the more we do that the more we see moisture problems inside the tight envelope. Never wrap your building walls with poly, or under the insulation in the floor. Always provide under floor ventilation, and wrap the walls with a permeable underlayment like Tyvek or tar paper.
|
|
toyota_mdt_tech
Member
|
# Posted: 15 Jan 2013 11:26pm - Edited by: toyota_mdt_tech
Reply
bldginsp, I have seen many home improvement shows (Holmes on Homes comes to mind) where the exterior wall is in Tyvek (under exterior sheating), while he always covers the inside with plastic vapor barrier (plastic). Is that acceptable if one side is wrapped with breathable (outside) while inside in no breathable?
Whats you opinion on spray foam? I assume that does breathe? I would think it could soak up moisture like a sponge.
You are right. Had a buddy with a home built in 1940, I have been helping him remodel it. It has zilch for insulation, not an ounce of mold or wood rot anywhere. It breathes so well. It didnt even have the black vapor barrier in the crawlspace over the ground!
I really enjoy reading your responses too. Its nice to get "inside info" on building practices (what works and what doesnt) right from the inspector.
|
|
rayyy
Member
|
# Posted: 16 Jan 2013 06:25am
Reply
Using hot showers or burning propane/NG in a ventless heaters or cooking (boiling water)on the stove.are what make lot's of excess moister inside.That moister has to go somewhere and it seek's the cooler surfaces in the building.Anything metal or glass or even wood surfaces that are much cooler than usual including your vapor barrier.That's where it will accumulate.The vapor barrier keep's it from soaking into your insulation saturating it and reducing it's insulating value also providing the perfect environment for mold and mildew to grow if it's not allowed to dry out.It's tough dealing with excess moister.Best thing to do is to ventilate it to the outside right from the sorce.Using outside wall vented heaters,hood exhaust fans over stoves vented outside and bathroom ceiling exhaust fans are commonly used.House wrap like Tyvec is pourous and will let out any moisture that does get into the insulation.
|
|
bldginsp
|
# Posted: 16 Jan 2013 11:14pm
Reply
I agree Rayyy
Toyota- I'm sceptical of putting a vapor barrier on the inside of walls, but I can't nix it entirely. Vapor barriers don't totally prevent moisture from passing through. Polyethylene is a porous material, believe it or not. You are not supposed to lay poly pipe in soil saturated in gasoline or oil, cause it will get in, and some types of caulking can damage it. If you use PEX piping you need a PEX approved caulk at plate holes.
So anyway moisture can get past the poly, then what? You hope it goes out the Tyvek, and probably will most of the time. What about the rest of the time? It's really a risk management issue- plan for the worst case scenario as much as possible. Older, 'loose' houses were hard to heat but the same seeve let out the water, like your buddy's 1940 home. Now we make the houses tighter, it's harder for moisture to get out. I say give it all the opportunity you can. But on a roof which has an open ventilated attic space, or above insulation space, there is plenty room for the water to get out so using the vapor barrier cannot hold in any moisture that does get past it. IMHO
There are two types of spray foam- open cel and closed cel. The closed cel makes a very tight moisture block, so I am told. It's expensive so it is rarely used, but is ideal in ceilings where ventilating above the insulation is impractical.
Open cel spray foam should be treated just like fiberglass in terms of moisture- moist air that gets to it can go through it. I don't think it soaks up moisture, but I don't know and have very little experience with it. It has a better R value than fiberglass, so it lets you get R19 or 20 in a 2x4 wall, far better than fiberglass's R13.
|
|
|