|
Author |
Message |
HopefulHomemaker
Member
|
# Posted: 17 Nov 2012 09:26pm
Reply
We have our 12 posts in (foundation grade PT 6x6 posts, set on 80 bags of concrete, tamped and backfilled) and the floor joists in. But my husband decided to cut the posts based off the top of the one in the back corner, where the ground was lowest, to leave a crawl space. That means that the back corner post is 43" from ground to house. The other posts all have less out of the ground than that, with the shortest being about 24" out. That's too much. I know it's too much. What can we do?
|
|
MtnDon
Member
|
# Posted: 17 Nov 2012 09:58pm
Reply
How deep in the ground are the piers? All more or less the same?
How many piers in how many rows? Spacing?
Do you have beams on top of the piers?
Ate joists on the beams or hung from the beam sides? Or... ?
Pictures?
|
|
HopefulHomemaker
Member
|
# Posted: 17 Nov 2012 10:07pm
Reply
The posts are all at least 48" into the ground. A few are deeper, because the trench got dug out a bit too deep. There are nine posts for the house, three more for the porch (porch joists are scheduled to go up tomorrow. The house is 16x20 with an eight foot porch, so 16x28. So 8 feet between the three posts across the width, ten feet between the house posts down the side, eight feet to the porch posts. We laminated and set the beams this morning. Three 2x8x16s for the center beam (which the joists are sitting on top of) and two of the same for each side beam (which the joists butt up against using joist hangers). The floor joists are 2x8x16 and are set 16"oc. Uploading pics now, they'll be in the next post.
|
|
HopefulHomemaker
Member
|
# Posted: 17 Nov 2012 10:12pm
Reply
Here are best photos I have of it.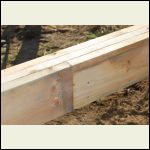 Laminated center beam
| 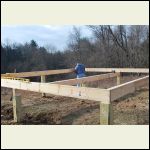 joists
| 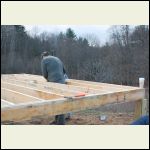 joists
| 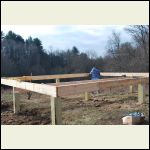 joists
|
|
|
MtnDon
Member
|
# Posted: 17 Nov 2012 11:20pm - Edited by: MtnDon
Reply
Quoting: HopefulHomemaker Three 2x8x16s for the center beam (which the joists are sitting on top of) and two of the same for each side beam....
Clarify this for me if you will. When you say "two of the same for each side" you mean two more beams like the center one (three 2x8's)? OR two laminated 2x's placed on top of the outside rows of piers? ... Looks like two layers in the outer beams in the images, but they appear deeper than 2x8... perhaps a trick of perspective??
So my question is what are the outer beams? Size and number of layers?
|
|
Anonymous
|
# Posted: 18 Nov 2012 12:19am
Reply
I think the way you have these is great. 24" isn't too much... Plus it gives you room to crawl around underneath.
That looks well built to me!
|
|
MtnDon
Member
|
# Posted: 18 Nov 2012 01:31am
Reply
As for the original question... you need bracing. From each pier to the beam it supports as well as to a floor joist that crosses over the beam. That is bracing in the 20 foot direction down the long side and bracing across the 16 foot width. I'd suggest 2x6 material, carefully picked for the least number of knots and straightest grain, especially near the ends where the fasteners would be located.
Braces would be diagonals, one end about two feet down the pier and the other end of the brace about 2 feet along the beam or joist from the pier. Set at 45 degree angle. Bolted through the brace member and the pier with a large washer under the bolt head and the nut at the other end. No carriage bolts. One 1/2 inch diameter per brace end.. Do not over tighten; that is do not crush wood. Add five or six 16D nails; hot dipped galvanized.
A better solution would be constructing what an engineer would call a shear wall. That is the spaces between the piers would be framed like a short wall with PT studs and a PT bottom and top plate. That would then be sheathed with 3/4 PT plywood on one side. The plywood would overlap the piers and the beam or joist. Nailed every 3 inches.
I know the question was about pier height, but other things caught my eye. So, for what its worth here it is.
The picture of the center beam showing an unsupported splice. A splice that is not directly supported by a pier is a bad splice. There is no nicer way to say it, it;s weak and potential trouble. It is also apparent that the beam slice is secured with a grey colored screw. They look much like the screws sold for use with pressure treated wood for securing deck boards, a surface to walk on. If that is correct those are not good as you used them. They are hardened and somewhat brittle, ideal for securing boards yopu walk on, but not for any structural use.
A closer look at enlarged images leads me to believe that, yes, the two outer beams are also layers of 2x8's as the center beam and joists are. And it does appear that each outer beam consists of two layers. OK? If that is correct and the spacing between the piers under the beam is 10 feet, those beams are, IMO, woefully undersized.
You are in NY state as i recall. Most of NYS has a rated snow load of more than 50 PSF.
NYS snow load map
So, if my assumption that the two outer beams are built from two layers of 2x8 grade 2 common lumber is correct here's what my reference materials indicate. The piers should be no more than 5'4" apart if the snow load is 50 PSF; 4'9" if the snow load is 70 PSF. And all splices over a pier. That's assuming a lightly loaded loft is in the building design. Lightly loaded = no furniture to speak of.
Or another way to look at it would be to use 3 - 2x12 or 4 - 2x10 for each beam with a post under each splice, for a 50 PSF snow load. For 70 PSF snow load, 4 - 2x12 per beam.
I'm sure you did not want to hear all that. It is my opinion, an educated opinion, but not one backed with any degree paper. You can do with it what you want.
|
|
HopefulHomemaker
Member
|
# Posted: 18 Nov 2012 09:12am
Reply
It will have a loft, which is half over the porch. The two out beams are two 2x8s. We did not use deck screws, we used exterior screws. We couldn't have had our splices over piers, because they all would have had to line up on the center piers, and that would have been even weaker than what we did.
We really have no choice but to move forward. We don't have the money or the manpower to tear down and rebuild from the ground up. If we brace the piers as suggested, is this house going to be strong enough to live in?
|
|
MtnDon
Member
|
# Posted: 18 Nov 2012 11:32am - Edited by: MtnDon
Reply
Quoting: HopefulHomemaker We couldn't have had our splices over piers, because they all would have had to line up on the center piers, and that would have been even weaker than what we did.
That's incorrect. It would be stronger than what you have. We do not use 2x lumber to build beams because they are better than using timbers cut from a tree for our large beams. If we still had large numbers trees that were suitable to cut 6x12, 10x 12 and larger timbers we would. Those would then still be positioned with the joints directly over a post/pier. But today trees that are large enough for large timbers are reserved for special uses and their prices are high. So we build them from 2x material. It is desirable to have the joints/splices spread out over different piers. However, having all layers spliced over the same pier would be preferable to splicing between piers.
EDIT: If it is not possible to stagger the splices over piers, and if the calculations indicate a triple 2x8 would provide sufficient support, then it might be a good idea to go up a size. Like 2x8's would become 2x10's. That is also with placing all joints/slpices over athe same pier, not having unsupported splices in "midstream".
If those screws are the grey Grip-Tite they appear to be, yes they are exterior screws. That just means they won't rust and those are also suitable for PT lumber. If you were to ask Grip-Tite if they were approved for structural use they would reply in the negative. I've asked.
Bracing the piers to the beams in one direction and the joists in the other will make the structure more rigid. That will help prevent shifting of piers. It does little to increase the load carrying ability of the beams. That is the deficiency with the beams you have built. They are not strong enough to meet current accepted design practice.
Nothing will likely fall down all of a sudden. One of the beauties of wood construction is that unless precipitated by some external event like flood, earthquake, extreme winds, etc., buildings that have structural deficiencies will slowly develop leans, tilts or sags. You will have rebuilding, strengthening at a future time most likely. And that is invariably more work than if done correct the first time.
You don't have to answer this; how did you decide the beams you built were of adequate size?
|
|
HopefulHomemaker
Member
|
# Posted: 18 Nov 2012 08:31pm
Reply
The beams were sized according to the plans we have. Engineer stamped plans, in fact.
Today we took down the side beams and rebuilt them. They're still only two 2x8s, but we balanced both splices on the post, with just a slight staggering of about 4 inches. We added plates to the inside of the corners. In the spring when we return, we're going to work on beefing up the center beam. We're also going to add metal plates to the joints of both side beams to provide even more strength to those. We'll also work on adding structure to the posts, under the house, so they can't shift (as much, anyway). Our soil is so sandy it's almost like beach sand, and it's full of rocks.. I'm not sure if that's working for or against us.
As for the screws, we left them. We searched the Home Depot for better screws and could find none. The cabin in the next lot over, built from the same plans but done by a contractor, was put together with nails. I hope we're at least doing better than that.
|
|
MtnDon
Member
|
# Posted: 18 Nov 2012 09:43pm - Edited by: MtnDon
Reply
Quoting: HopefulHomemaker The beams were sized according to the plans we have. Engineer stamped plans, in fact.
Wow! I am amazed at that. If you don't mind could you tell me from where? I I'm just personally curious
Sandy soil structures will benefit highly from great bracing as sandy soil offers little in the way of lateral support.
|
|
HopefulHomemaker
Member
|
# Posted: 18 Nov 2012 09:55pm
Reply
Got the plans from Christmas and Associates. This is one of the "Hemlock" cabins that a few people here have. Stamped by McElwain Engineering in Newark Valley, NY.
|
|
MtnDon
Member
|
# Posted: 18 Nov 2012 10:07pm
Reply
Thanks
|
|
CottonPicker
|
# Posted: 19 Nov 2012 03:45pm
Reply
Hopeful,
This may be too late to help you as you are too far advanced in your construction but it may be useful to a beginner reading this.
I noticed that the outside vertical sides of your posts are not in alignment with the outside vertical surfaces of your sills.
When I build I ensure that these two surfaces are perfectly aligned.
In this manner, when you attach the outside covering (Smart board?) it will present a perfect vertical surface from roof line to ground surface.
Cotton Picker
|
|
CottonPicker
|
# Posted: 19 Nov 2012 03:49pm
Reply
Hopeful,
I forgot to mention that the crawl space will come in very handy as storage space.
I would remove all rocks & do some superficial leveling.
Cotton Picker
|
|
cobra grover
|
# Posted: 19 Nov 2012 07:04pm
Reply
I think the piers/posts are plenty deep and I don't think the height is a problem. Normally I would use three 2 x's NAILED together with two 1/2 inch pieces of plywood sandwiched between (not sure how wide the 2 x's should be. Probably 2x10 or 2x12's. This would give you 5 1/2 inch wide beam which would fit perfectly on your 6 x 6's. I would have 3 beams instead of one. Then the floor frame would set on top of the beams with some sort of ties holding the floor to the beams.
Take my advice with a grain of salt. I am not a licensed contractor. Just trying to help.
|
|
MtnDon
Member
|
# Posted: 19 Nov 2012 07:51pm
Reply
Quoting: cobra grover 1/2 inch pieces of plywood sandwiched between
Just a FYI... The best thing about using 1/2 ply is to space the built up beam out to fit standard metal connectors. The plywood does not add appreciable strength; in fact most engineers will disregard the plywood. Only the plies that have the grain oriented horizontally would count towards strength anyhow. So, consider a cheaper and easier alternative; cut plywood "patches" and use then on the outside of the assembled beam wherever the beam passes through a connector.
@HopefulHomemaker I found Christmas & Associates website but they don't have a listing to buy plans; just built cabins. So far, no response from them re my email inquiry.
|
|
Sustainusfarm
Member
|
# Posted: 19 Nov 2012 08:07pm
Reply
MIne is built the same way but close to the ground like you were hoping for...I will tell you, you will learn to appreciate that extra space to be able to get underneath to various projects like rinnung wire, plumbing or insulation! I wish I could get under mine!!
|
|
cobra grover
|
# Posted: 19 Nov 2012 09:02pm
Reply
As I said, not licensed nor an engineer. Aren't the layers of plywood running perpendicular to each other? Isn't that what gives it stability? And what about OSB?
|
|
MtnDon
Member
|
# Posted: 19 Nov 2012 09:29pm
Reply
Quoting: cobra grover Aren't the layers of plywood running perpendicular to each other?
Yes. In a 5 ply plywood three layers run with grain in the 8 foot direction. Those 3 layers would be counted in the engineer's calculations. If it was cheap 3 ply then two layers would count. The layers with grain running across the width / depth of the beam give no increase in strebgth at all. OSB is different but probably comes out with around the same stiffness as the plywood. Don't know for sure as I'm not an engineer either.
We only gain a small amount of stiffness, no more than an extra 15%. Seems to me a lot of work and material cost for a small return. Plus the tables used for girder sizing in the IRC do not count ply or osb or any other spacing or laminate materials. So discounting them makes it easier to use table information, IMO. Full length strips between layers will never hurt, just not a great return, IMO. For similar reasons glue is not normally counted. A good glue job can increase stiffness of the built up beam. Gluing is a variable the designer has no control over though, so it is safer to not count glue.
|
|
MtnDon
Member
|
# Posted: 20 Nov 2012 10:45am - Edited by: MtnDon
Reply
I got a copy of the plans this AM. I see they are stamped for the occupancy code U (NYS code U is utility which means "a cabin, camp or lean-to or other similar structure designed for occasional occupancy for hunting, fishing, or similar purposes." That info comes from a 2006 NYS document.
I don't live in NYS and so am not 100% familiar with what exactly is current code. The plans are dated 2005. I believe in 2010 NYS adopted the IRC as the base for its building code. I have no idea if they still use the same occupancy codes as in 2005 - 6.
Anyhow I just thought someone might be interested. Someone might have more up to date info as well. But now I understand what the plans are and for what purpose the stamp is good for.
|
|
HopefulHomemaker
Member
|
# Posted: 20 Nov 2012 10:12pm
Reply
We ended up taking down the two outer beams and rebuilding them. They're still only two boards wide, but the have just a slight overlap so that both splices are supported by the posts. We'll be redoing the center beam next year. I don't know the best way to do it (obviously a single 6x8x20 beam would be the best, but that isn't going to happen) so I'll spend the winter researching and calling around, I guess. Next spring we'll also be cross-bracing the posts, adding a retaining wall on the low side, and possibly having a truckload of fill dirt brought out to raise the grade just a bit. It still won't be perfect, but hopefully sturdy enough.
|
|
adakseabee
Member
|
# Posted: 21 Nov 2012 08:00pm - Edited by: adakseabee
Reply
Hopeful Homemaker -
To strengthen your center beam I would add two "sisters", one on each side of your existing "laminated" beam of three 2x8s. To support the "sisters", add vertical 2"x6"x4 foot scabs attached to the existing 6"x6" piers using "ledger-lok" fasteners (those with the built-in "washer") such that the top of the scabs supports the new "sisters" from below. If you cannot find 2x8s sufficently long to span the entire width of your building, ensure you splice over the center pier.
Of course, you could replace the entire center beam with a steel I-beam or an engineered beam, but I doubt that you will want to go to the expense and trouble.
For the perimeter, since it appears that outside edge of the 6x6 piers extended beyond the outside of your double perimeter rim joists, I would have added an additional 2x8 fastened to the outside surface of the rim joists supported by the 6x6s or scabs, if necessary.
The Home Depot carries Ledger-Lok fasteners. If their cost is too much for you, by all means use/supplement the Ledger-Loks with galvanized nails/spikes.
You mentioned that the engineering firm that stamped your plans was in Newark Valley. Are you located in Newark Valley township? If so, you may find the attached link helpful: http://townofnewarkvalley.com/codeenforcement.html
If you are not in Newark Valley township, but in another township of Tioga County (my cabin location), go to the following link:http://www.tiogacountyny.com/towns-villages.html
The township code enforcement officer should be able to inform you of what version and section of the Building Code that applies in your situation.
|
|
HopefulHomemaker
Member
|
# Posted: 24 Nov 2012 10:41pm
Reply
We're not in that town. We're already in contact with the code guy in our town, and he's been very helpful. He hasn't been out yet to see what we've done, but I expect he will be out this next week, so I'll be calling to see what he has to say.
As for the center beam, we're looking at a few options. One is to beef up the beam in the way you suggested, by adding more boards to it, supported by extra planks attached to the posts. Another option is to find a beam that will fit the house, but I don't see that happening. The third option is to take the beam out and remake it like we did the other two. The final option is to come up with two beams the are wide enough, but half the length of the house, and connect them on top of the center post. I have some research to do.
|
|
Martian
Member
|
# Posted: 25 Nov 2012 09:22am - Edited by: Martian
Reply
To save having to re-build the center beam, why not just add supports to shorten the spans? It looks like your soil is easy digging.
I'm not sure why you didn't use full length material for the beams, but a simple solution for stiffness would be to add a 2X12 to the perimeter. Just extend the notch down the post and nail/screw/bolt it on.
As for the strength of your current beams......Its been 13 years since I built my first cabin. It is 9' above grade as its in a flood area. I used doubled 2X10 for banding/perimeter beams supported on 8' centers under the loft and down the sides. It is 16X24 w/an 8' loft. obviously you can see the span is greater under the shorter gable end; its 12'. There have been no problems show up. There are angled braces 2' down the 6X's up to the beam. Even in 80mph winds, it doesn't move.

Notice the downed limb? I slept through the storm that brought it down.
Here's another view: 
If you can pass inspection the way you have constructed it, add the bracing and move on.
Tom
|
|
|