|
Author |
Message |
jerejere
Member
|
# Posted: 6 May 2024 08:43pm
Reply Quote
Hi all, I read a thread from last year where gcrank1 and pbc312 discussed using exterior insulation only on a small bunkie (link here: https://www.small-cabin.com/forum/2_11646_0.html) I’ve got two walls and sheathing up on what I hope to be a similar project. It was suggested to me that with so little insulation, the exposed sheathing on the interior of the cabin might be cold enough for water vapor to condense there. Anyone have thoughts about that or about the wall configuration in general (details below)? I believe gcrank1 has experience with a similar design (exterior insulation only) in a similarly cold climate as mine. Would love to hear thoughts from anyone who wants to share.
My project is a small 8x16 cabin in Schoharie County, upstate NY, climate zone 6 (but on the border with 5). Listed in order from inside to out, I’m planning for the wall assembly to be: 2x4 rough cut hemlock frame (left exposed on the inside), 1x8 diagonal solid wood (hemlock) sheathing, 2-3” of external tongue and groove wood pulp insulation (Timber HP’s timberboard—listed at 40 perms per inch), air gap/drainage plane/rain screen with furring strips, followed by 1” solid wood siding (likely hemlock). There will be 2’ eaves on the load bearing walls and 18” on the gable ends. No house wrap.
There will be a wood stove or ideally a masonry stove (Walker tiny cook stove).
Most likely the cabin won’t see more than 30-40 days of occupancy each year but I would like to be prepared for potential full time living if plans were to change.
I could potentially increase the amount of exterior insulation if that is critical—the timberboard is listed at R 3.4-3.7 per inch.
My thought was that with such a small place and no real kitchen or bathroom, there’s not as much moisture. The wood stove/masonry stove shouldn’t have much problem keeping the tiny place decently comfortable and that any moisture would quickly dry to either side of the wall assembly.
|
|
ICC
Member
|
# Posted: 6 May 2024 09:21pm - Edited by: ICC
Reply Quote
A permeability above 10 is not considered to be even a vapor retarder, let alone a vapor barrier. Vapor will be able to pass theu to the HP board. Not fast but it would be able to soak in amd eventually pass theu. Or in winter the wall could get cold enough to frost up.
I have stayed in cabins with little or no insulation as well as tents with wood stoves. To me, in cold, freezing weather they always have cool / cold air always spilling off the walls and roof. But that may be different for different people.
|
|
ICC
Member
|
# Posted: 6 May 2024 09:38pm
Reply Quote
Permeability .... Most OSB had a permeability around 1.0 but it varies with thickness and the humidity. Advantech, a premium water resistant sheathing and sub flooring, has a permeability less than one. Less than 1 is considered a very good vapor barrier.
|
|
jerejere
Member
|
# Posted: 7 May 2024 01:50am
Reply Quote
Yes, I have advantech subfloor panels on the floor but opted for 1x8 hemlock diagonal sheathing for the walls in the hope that we can make it work with exterior insulation only and we get to use the rough cut hemlock studs and hemlock sheathing as our interior finish. I suppose there isn’t much harm in trying it out as the plan sits today and then I can always add cavity insulation/vapor barrier down the road if the rustic design results in an overly rustic experience.
|
|
Brettny
Member
|
# Posted: 7 May 2024 12:02pm
Reply Quote
Never meet anyone who said "I wish this building wasn't so well insulated".
|
|
Grizzlyman
Member
|
# Posted: 7 May 2024 02:28pm
Reply Quote
Vapor… I’m not sure- it would seem to me that unless it’s bitter cold you’d probably be ok for frost and vapor when heating… but really dont know. why not double up the wood pulp insulation sheathing now? This would have the added benefit of covering any seams as well.
as far as actually heating the structure… At 128 sq ft- insulation is important of course, but depending on outside temp- it may be tough To not cook yourself out! … even when just trying to cook something. How are you going to cook in the summer? I would imagine you need a different propane stove or similar for summer cooking.
What is the walker tiny stove BTU rating? Heat retention might not be a problem. I would imagine the insulations function is mainly to keep drafts out- especially with only 3-4 R.
What about the roof insulation? Most of the heat loss is through the roof.
The diagonal sheathing will look cool on the inside. It sounds like you have a well thought out plan- my suggestion would be to make sure you have a good system for marking studs on the exterior- especially with the air gap. You don’t want any nails popping through that beautiful sheathing!
And agree you are correct- if it doesn’t work and you need more insulation you can always go back and fill the cavities.
|
|
Grizzlyman
Member
|
# Posted: 7 May 2024 02:34pm - Edited by: Grizzlyman
Reply Quote
My bad. I missed you saying 2-3” of sheathing… so really we’re talking about 9-12r +on the walls.
|
|
gcrank1
Member
|
# Posted: 7 May 2024 02:41pm - Edited by: gcrank1
Reply Quote
Our 12x24 c/w 12x12 stand up loft had 1" blue DOW on the outside of 3/8" ply sheathing, NO ceiling insulation and the 1" under the floor deck. I had always intended to put bats in the ceiling and T&G boards but never got to it in the 33ish years we used it. The old, med-sized antique wood stove could cook us out! One your size with your proposed insulation I think you could heat with an old Coleman gas lantern. At the time I didn't know about house-wrap and didn't even use tarpaper outside the sheathing (nor a v-barrier inside). We never saw any signs of mold or rot but I also never had to pull off any of the barn board siding over the DOW to expose the sheathing.
|
|
jerejere
Member
|
# Posted: 7 May 2024 11:03pm
Reply Quote
Yes, agreed, with the small size, I was picturing us getting cooked out as well.
It might make sense to go even thicker with the exterior insulation--easier than having to go back and do cavity insulation later. The Timber HP people will have thicknesses up to 9". So could do 4-5" and get closer to what the R value would be with cavity insulation anyway. My only hesitation there is that I'm wondering if the expanded footprint of the cabin plus exterior insulation will be counted towards our square footage. We're at 128 sq ft and need to stay under 144 to not need a permit or have property tax implications. I emailed the local code enforcement guy and am waiting to hear back about that. I'm hoping the square footage is determined by the foundation/footings--would seem silly to include external cladding/insulation...
As far as the roof, I also wanted to leave our rough cut 2x8 rafters and diagonal roof sheathing exposed. Planning to add additional wood pulp insulation/Timberboard up there--at least 4 inches. Same idea with a roof membrane over the sheathing followed by insulation, furring strips on top to create a 1" ventilation space, and then metal roofing.
And yes, summertime cooking will be done outside on a propane stove like we do now when we're camping there.
I'll add a couple pictures of what I've gotten done so far.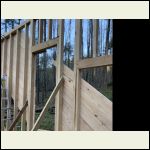 IMG_1436.jpg
| 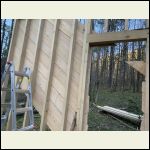 IMG_1437.jpg
| 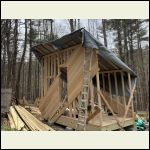 IMG_1452.jpg
|  |
|
|
Brettny
Member
|
# Posted: 7 May 2024 11:22pm
Reply Quote
That wood pulp insulation is interesting stuff. Never knew they made such a thing. Why use this over foam that's generaly 2x the R value? I'm sure the timber pulp is also prety expensive stuff?
|
|
ICC
Member
|
# Posted: 7 May 2024 11:30pm
Reply Quote
Every jurisdiction I have worked in constructing structures for others has wording in the regulations that limit buildings that do not require a building permit in some ways.
One very common thing is to limit the permit-free building to be an accessory building, which means there must be a larger building on the site that was built with a legal building permit. The maximum size varies from location to location. Other rules often involve the use of the permit-free building to be strictly for storage or to be a playhouse. That will no mean no kitchen, no sleeping facilities.... depends on the locale. Regulations vary and should be checked out very carefully unless you don't mind perhaps being illegal construction or use with the possible recriminations.
As for the question about footprint, the actual text of the rules should be carefully read to not let one's wishes influence the perceived meaning. OTOH, that is more or less why many centuries-old buildings in Europe were built with a smaller footprint for the main floor. Then it was a question of reducing the taxes with a smaller footprint.
|
|
jerejere
Member
|
# Posted: 8 May 2024 01:45am
Reply Quote
As far as cost, the timberboard/exterior product is supposed to be competitive with other conventional choices. I haven't seen the pricing yet on the exterior grade product because it hasn't actually come out yet. It's supposed to be available end of this year. The loose fill and batt insulation is available now, looks like it's a little more than fiberglass insulation, about $1.75/sq ft for the 5.5" batt: https://shop.hancocklumber.com/shop/insulation/timberhp-wood-fiber-insulation
It's all just starting to be produced here in the US, in Maine (they've been making it in Europe for a couple decades, I think).
The price is comparable or at least in the neighborhood, and the R-value per inch I think is comparable to most other products (3.4-3.7 per inch for the exterior product), not quite as good as xps.
Our building site is the kind of place that I don't see too many people wanting to ever put a house on (it's a bit steep and has a small cemetery awkwardly placed in the middle of our 10 acres). So I like that it's being made from a waste product and a natural material and that if my kids or their kids don't take care of this cabin and it disintegrates in 80 years, it'll have an easier transition back to dirt.
As far as the permitting, I definitely read about the need for these unpermitted, 144 sq ft and less buildings to be an "accessory" building to a primary home/residence/etc., but I explicitly asked the code enforcement officer what I can do on this vacant lot without a permit. I think this is one of those towns that is pretty undeveloped and they give folks a bit more leeway than some other places.
|
|
Brettny
Member
|
# Posted: 8 May 2024 10:17am
Reply Quote
The price per Sqft isnt that comparable. R21 is about $1sqft.
Since your in NY I know a place you can buy poly iso for very cheap. Its roughly 1hr from you. I used 4in in my ceiling and will be useing 4in in my floor.i paid $100-$120 for a 4'x4'x4' square pallet of the stuff. Doing quick math that's about 50c a sqft. Plus caned foam for the edges.
|
|
|