|
Author |
Message |
Aklogcabin
Member
|
# Posted: 26 Aug 2022 10:33am - Edited by: Aklogcabin
Reply
I had the opportunity to visit with a gentleman from the cold climate research center at our university concerning the insulation in the new house we're building. His suggestions were. I'm starting out with 2x6 walls with 1/2" cdx plywood on the outside. The university recommends plywood over osb. Putting rockwool insulation between the studs in the wall cavity. 6 mil vapor barrier sealed with acustic butyl caulk on all edges on the walls n lid. Tyvex would be installed over the plywood outside. Standard construction techniques. Then install 2" ridgid foam insulation R-10, pinkboard for me, over the insulation directly to the studs. Then put 2x4s running horizontally fastened to the studs with timberlock screws. And fasten the sheetrock to the horizontally running 2x4s. I'm thinking about standing the sheetrock up so there would be minimal butt joints to tape. The plumbing and electrical that would normally be installed in the wall cavity will be installed on the inside of the sheetrock walls. Placed in the 1-1/2" gap that the 2x4 makes. Which acts as a still air gap also and helps to get a better overall energy rating. So yeah put 2" of pinkboard between the rockwool insulation and the sheetrock. This will act as a thermal barrier as well and not create a conductive energy loss. Has anyone else ever seen this type of construction method used ? Any options are considered constructive
|
|
gcrank1
Member
|
# Posted: 26 Aug 2022 10:49am
Reply
Guess that info is current 'state of the art'. What would be the real world dif of using only 1" styro?
|
|
travellerw
Member
|
# Posted: 26 Aug 2022 02:08pm - Edited by: travellerw
Reply
Quoting: Aklogcabin Placed in the 1-1/2" gap that the 2x4 makes. Which acts as a still air gap also and helps to get a better overall energy rating.
I find the pink board on the inside very interesting as all the advice I was given (and researched) was to put the thickest foam insulation I could afford on the OUTSIDE. Which is how the new ultra modern sheathing systems (like ZIP Systems) are installed. Did they provide a reason they suggested this? It really has me shaking my head as I don't think there would be any advantage over installing on the outside and you have a whole bunch of extra work (horizontal 2x4s, hanging drywall different, ect).
But what I find most surprising is the suggestion I quoted above. That wouldn't pass code here as it would put the "services" too close to the inside surface (just 3/4") where they could easily be punctured by a nail or screw. Here you would still need to run them through the 2X6 studs and rockwool.
|
|
ICC
Member
|
# Posted: 26 Aug 2022 05:00pm
Reply
My home, and many of the ones built in the past decade use XPS or polyiso foam sheets on the exterior of the 2x4 stud wall. Some of the homes did have cellulose blown into the walls after the plumbing and wiring was done, while some had the stud cavities left void of insulation. I like exterior sheet foam for many reasons. The plumbing is all on the warm side. Easy to retrofit plumbing or wiring if a remodel is done.
I built an exterior rainwall system with an air gap between the final layer of foil faced polyiso, 1 inch thick furring (vertical) and Hardie cement fiber lap siding. Inside walls are mostly drywalls but some of those have T&G pine or aspen over the drywall.
Polyiso would not be recommended for very cold climates as the r-value decreases with very cold temperatures.
|
|
NorthRick
Member
|
# Posted: 26 Aug 2022 05:53pm - Edited by: NorthRick
Reply
Quoting: travellerw But what I find most surprising is the suggestion I quoted above. That wouldn't pass code here as it would put the "services" too close to the inside surface (just 3/4") where they could easily be punctured by a nail or screw.
My Anchorage house is 2x4 construction with electrical and plumping run through the studs. That puts stuff about 1 inch back from the wall surface. (1/2" sheet rock, 1/2" from the hole in the middle of the stud to the surface of the stud). In AKlogcabin's case, things run along the backside of the hollow cavity behind the sheetrock would have a similar spacing.
Quoting: travellerw find the pink board on the inside very interesting as all the advice I was given (and researched) was to put the thickest foam insulation I could afford on the OUTSIDE.
Water vapor management in walls is far from straight forward and differs from region to region and even then the "experts" will disagree. I suspect the recommendation for putting the foam board inside instead of outside for a house in south central Alaska is reduce the amount of moisture from inside the house that makes it into the wall. And, to maximize the ability for the wall to let water vapor out to the outside.
The main vapor barrier on the inside is the 6mil poly. Foam board will let some water vapor through but it does impede it, so better to be inside than outside in this situation.
I also suspect that's the reason for plywood over OSB recommendation on the outside as water vapor goes through plywood easier than OSB.
In short, try to keep the water vapor inside the house from getting into the wall and let any water vapor that does get into the wall escape to the outside.
|
|
Aklogcabin
Member
|
# Posted: 27 Aug 2022 10:51am
Reply
NorthRick hit the nail on the head. The main reason for putting the insulation on the inside wall is moisture management. The 6 mil plastic vapor barrier will get plenty of nail holes, holes for electric boxes n such in it with standard building techniques. Moisture can travel through to the walls through different atmospheric pressures and temperature differences. Materials such as sheetrock, wood absorb moisture and can transfer that moisture into the walls. Moisture migration Or through a leak. With the 2" r10 ridgid insulation on the inside will help stop moisture. Having only the holes from the timberlock screws holding the nailer, perlands, is beneficial. Tyvex on the outside of the plywood walls will let the moisture out of the wall and help keep moisture out. We have large temperature and humidity differentials that have to be considered. Especially since I will be trying to seal it up. I'm trying to shoot some holes in this idea of putting the pinkboard up inside. Not finding many. Other than loosing 3-1/2" of floor space. And the utilities where they will be more exposed. I have thought about putting a piece of 1-1/2" metal channel on top of on of the horizontal 2x4s to place them in. Or a piece of flashing nailed on a 2x4 that extends up a couple inches. We are mostly looking for practical and not cosmetic. Energy efficiency is the goal. Concerning the use of plywood over cdx. The university stated in its studies that the plywood just works better. Here the cost difference is margin in the big picture. My personal experience is that plywood has been better. Although each has its place. We just finally got most of our windows, Pellas, and a couple triple plane picture windows. Now I can get them framed in. Any suggestions on how to build the best headers ?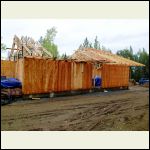 Rolling trusses
| 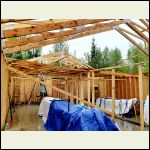 Inside
| 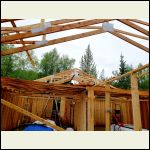 Looking up
|  |
|
|
Aklogcabin
Member
|
# Posted: 27 Sep 2022 11:57am
Reply
I had a little battle with covid so that slowed things down a bit. I'm finalizing the plans for insulating and would appreciate feedback. 2x6 walls will have 5-1/2" of rockwool insulation. 6 mil vapor barrier. 2" pinkboard. Changing up the 2x4s to 1x4s. Going to run 5 rows horizontally. One on the bottom, top, middle, middle of the middles. Then run 1x4s vertical. Screwed to the studs 16"oc. This will create a channel for the wire n water lines to run in. This type of design is commonly used for basements. And can be used to increase insulation in a remodel. Another major reason for not placing the foam on the outside is that siding can sag. Lot of weight out there. Especially with the 2" foam. Outside is 1/2" plywood with tyvex. 1x2 nailers installed vertically 16"oc on the studs. 1x6 pine boards nailed flat. 3/8" gap between boards filled with permachink. Thinking about installing 3/8"×3/8" foam with glue on one side on the back edge of the pine boards for backup to the permachink and to help reduce costs. Permachink is spendy. But hey, everything is spendy. Just need to get this correct the first time. Thanks for any suggestions folks
|
|
Tim_Ohio
Member
|
# Posted: 28 Sep 2022 11:27am
Reply
The reason you might want to run your drywall in horizontal fashion, verses upright is because horizontal seams are less noticeable verses vertical. Also, any vertical seams where the horizontal sheets meet will be shorter, and alternate.
Tim_Ohio
|
|
travellerw
Member
|
# Posted: 28 Sep 2022 02:20pm
Reply
Quoting: Tim_Ohio The reason you might want to run your drywall in horizontal fashion, verses upright is because horizontal seams are less noticeable verses vertical. Also, any vertical seams where the horizontal sheets meet will be shorter, and alternate.
Horizontal seams are also WAY WAY easier to mud and tape. The seems are just above hip height and easy to work on. Vertical seams require bending and stretching, and maybe a ladder.
I'll be interested to watch the progress as you continue. I'm still not convinced of the foam on the inside. The expert opinion around here, is rigid foam goes on the outside and you put up as much as you can afford. I believe our climates would be similar (gets +40C in the summer and -40C in the winter here). However, we are a pretty dry climate. Anyway, maybe the experts around here are using old school thinking... or maybe they don't want the extra work.
|
|
Brettny
Member
|
# Posted: 28 Sep 2022 06:21pm
Reply
Quoting: Aklogcabin So yeah put 2" of pinkboard between the rockwool insulation and the sheetrock. This will act as a thermal barrier as well and not create a conductive energy loss. Has anyone else ever seen this type of construction method used ? Any options are considered constructive You should really put the 2in foam outside of the studs then the sheething on that. By doing it this way your studs wont transfer cold and it will act as a vapor barrier
|
|
ICC
Member
|
# Posted: 28 Sep 2022 09:12pm - Edited by: ICC
Reply
Quoting: Aklogcabin Another major reason for not placing the foam on the outside is that siding can sag.
That is not necessarily correct. Much depends on the technique used. We have done many retro insulation jobs using xps and/or polyiso foam sheets up to 4 inches thick. The foam sheets are in 2 or more layers with staggered seams. The foam is secured to the sheathing (osb or zip panels) using screws and special for foam 1.75" plastic washers with anti-spin tabs. Usually the final layer of foam is foil faced polyiso, though sometimes the budget calls for foil faced eps.
Then 1x3 or 1x4 vertical furring strips; minimum 3/4", often a full 1" we saw ourselves. The furring strips are screwed to the studs with Fastenmaster HeadLOK structural rated screws. There is an engineered table of how many screws at what spacing that has provision for foam thickness and type of siding. Even cement fiber boards. This makes for a great rainscreen wall.
Many of these are older than 12 years old, including mine. No issues.
|
|
Aklogcabin
Member
|
# Posted: 29 Sep 2022 11:12am
Reply
Thanks folks. On the sagging of the siding, I've not had problems personally. While researching this issue appears in several different reports. I suspect that the type of siding matters most. And usually something thinner is used. I know I won't need to be considered. The studs won't transfer heat. 2" foam is a pretty good thermal barrier. From information I've read this style of construction had been used in Norway, Sweden regions for a while now. As far as expert opinions. I was fortunate to be able to visit with a technician from the cold climate housing research center in Fairbanks. He is an expert. And I've gone to college for 2 years for RHVAC. So I do have a clue. I do have a pretty good understanding of the physics associated with energy transfer and dew point of moisture. This wall design is made to dry to the outside. There are many ways to build. I'm going to try to improve what most do. And i appreciate the responses
|
|
cabinnewbie
Member
|
# Posted: 1 Oct 2022 08:33pm
Reply
Quoting: ICC The foam sheets are in 2 or more layers with staggered seams. The foam is secured to the sheathing (osb or zip panels) using screws and special for foam 1.75" plastic washers with anti-spin tabs. Usually the final layer of foam is foil faced polyiso, though sometimes the budget calls for foil faced eps.
For 4" of foam, do you use like 4" screws to attach washer to sheathing? Imagine the screw runs flush with the foam board and then shouldn't pierce the sheathing all the way?
|
|
|