. 1 . 2 . >> |
Author |
Message |
JD0
Member
|
# Posted: 9 Jan 2025 04:26pm
Reply
Hey everyone, This forum has been a big help over the years for various projects but this is my first post here. I'm in the planning stages for my seasonal cabin on a mountainside in southern WY. I plan on building this spring. At this point my plans are pretty general, but I would like to lay out what I have and get some input from those more experienced than me. This will be used probably just a few weeks a year total, mostly in the summer and fall.
The land does not have any trees, and has a gentle slope-probably about 5-8 degrees. The soil is well drained clay-gravel loam. For size I am thinking ideally 18x34 feet, with rafters and a simple 8/12 gable roof. Approximately half will be an open living room area, and the other half will have a loft for sleeping and storage, with a bedroom, bathroom, and a small galley kitchen underneath.
The foundation is the big sticking point at the moment. I like the idea of using sonotubes, however the frost line is prohibitively deep (guessing around (70") and I don't think it will be cost effective to get equipment in to auger holes deep enough. Everything I've built in the past (albeit nothing quite this big) has been on gravel and floating concrete blocks so I'm leaning towards going that way - I understand it's not ideal and I will have to deal with releveling in the future but it seems like the most feasible option. If I go this route, will I need to consider downsizing my plans to minimize the effects of settling?
Atop a 2x8 pt floor frame and 3/4 subfloor, I plan on using 2x4 walls. I could probably be talked into doing 2x6, but I'm not sure if I see the need for it. I plan on insulating some but I will not have very good access during most of the winter anyways, so it probably will not see much use between December and April. I will probably use T1-11 for the siding, and possibly just wrap felt around the studs and have it do double duty as the sheathing as well, since I read this is acceptable. Otherwise I am considering 7/16 osb, felt, then 1x4 spacers beneath the t1-11, but don't know if it's worth the added cost ($750 or so)
For the roof I plan on 2x6x12' rafters spaced 16" oc. I would like to do an 8/12 pitch for increased headroom in the loft but I might go 6/12 or even 5/12. I really do not like working on steep roofs. I plan on getting a chicken ladder and using safety equipment, but still. An 8/12 pitch gives me 12" of overhang, and 22" for 6/12.
T1-11 sheathing on the roof (upside down for a plank look on the inside), felt, a thin (1-1.5") continuous layer of ISO foam (glued/seams taped) then battens nailed over the rafters and exposed fastener metal roofing on top of all that. On the inside, 2x6x18' rafter ties on every rafter. For about half the space there will be a loft so these will double as the floor joists for the loft. So the rooms under the loft will have 8' ceilings, and headroom will be about 7' at the loft peak if I do 8/12 pitch. I do plan on an interior wall under the loft roughly halfway in between the span to help support the load of the loft.
That's basically it in a nutshell - there are no inspections or code to worry about but if there are any red flags or just ways that I could do things better I would love to hear your ideas. I will try to post some pictures of my latest iteration of a floorplan later on.
|
|
spencerin
Member
|
# Posted: 9 Jan 2025 10:34pm - Edited by: spencerin
Reply
To be clear, these are opinions, and as such, they don't carry much value. That said -
1. If you do a very good job prep-ing and laying the gravel-and-block foundation, as well as the beams supporting the cabin, settling will be very minimal.
2. I would do 2 x 6 walls if you can. Insulation isn't just for wintertime, it's for summertime, too. And even if you won't use it much in the wintertime now, you may in the future.
3. Do a shingle roof if you can, instead of exposed metal fastener. The metal sheets may last decades, but the screws sometimes don't, requiring replacement earlier. Also, if there's any minor damage to the roof, you often have to replace an entire sheet, vs. just a few shingles.
|
|
Grizzlyman
Member
|
# Posted: 10 Jan 2025 08:20am - Edited by: Grizzlyman
Reply
Wow sounds awesome! Sound very similar to what I built.
I would do 2x10 floor joists not 2x8- I’m guessing an 8’ joist span to middle beam and then cantilever over beam on sides? 8’ may be ok on the span tables but I would do 2x10 to make sure it isn’t bouncy at all- just my opinion.
I wouldn’t do a 6/12 roof if you build the loft that way as you you won’t have any head room in the loft.
8/12 with steel roofing will be not walkable- so the install wil not be fun. but that pitch wil be good for snow load in the mountains. 12/12 might be better for both headroom and snow load if you’re not going to walk on it either way.
Sounds like you’ve thought I out well. Good luck and I look forward to seeing the progress!
|
|
paulz
Member
|
# Posted: 10 Jan 2025 08:23am - Edited by: paulz
Reply
Good points Spencer. After a dozen years my place still ‘looks’ square but the front door is starting to get a bit sticky. At some point I’ll have to get under there with a jack on the beams, but not too bad for all that time.
And prior winter a branch came through the roof. One spare shingle shoved under the one above it, done. Sounds like JDO won’t have that problem!
Good fortune jdo!
|
|
JD0
Member
|
# Posted: 10 Jan 2025 09:43am
Reply
Thank you all for the input
Quoting: spencerin settling will be very minimal.
This has been my experience in the past, but with a building this size I didn't know if that would change things much. From the reading I've done it seems like sonotubes aren't foolproof either, though. And when things go wrong, there seems to be more potential for damage.
Quoting: spencerin . I would do 2 x 6 walls if you can
Good point, I may end up doing this. My biggest drawback would be the loss of square footage on the inside. If I'm doing my math right, it would be a loss of 18 sf, so not insignificant. I would also need to increase my roof insulation, there's little point in doing r-19 in the walls of the roof only has r-6 or 8. But...it's not something I can change in the future if I change my mind so I might just bite the bullet.
Quoting: spencerin Do a shingle roof if you can, instead of exposed metal fastener.
Good idea, I hadn't really looked at shingles. It would certainly be cheaper than metal and probably decrease condensation, too. I guess my concern would be wind and snow shedding. Although I'm not 100% sure metal is more wind resistant than shingles. Something I will look into.
|
|
gcrank1
Member
|
# Posted: 10 Jan 2025 09:49am
Reply
That footprint is a good 'livable' size; we went from a long time 12x24 c/w a 12x12 loft to a 16x32ish at the new property. The open floor plan and 'elbow room' was very nice. But it was a shanty of a build by the prev owner....so last spring we brought in a prebuilt log cabin of 12x28. The sf is similar, though a bit narrower (could have gone up to 32 but we wanted the 4' porch roof over the door end). I did the 'gravel and cement silo staves (used)' floating foundation. I suggest you do the site prep asap so the disturbed ground beneath will get compacted, do a layer of 4" crushed rock topped with another layer of 'crusher run' then blocks. I really like the silo staves though they go 80# apiece!. Use as many as you can. We considered building again but don't have it in us anymore. If we had it would have been about your proposed size; as said, don't scrimp on joist size, 2x6 walls at 16oc, and some 'rainwall' and 'hotroof' concepts. Use as much styro on roof as you can And under the floor, doing the floor after the build would make you wish you has done it before. With exposed studding inside you can wire and insulate as you are able and take your time on interior walls. We like wood (thus our choice of a milled log cabin) so when thinking about maybe a build we would have likely gone with pine 'boxcar siding'. We wouldn't do a loft again as 'living space' though some would be ok for seasonal goods storage. Reason? When we built the first we were in our 30's and could negotiate a ladder up/down. Within 10yrs that became an issue with some injuries, and No-Way now in our 70's. YMMV There is Lots more....but remember you start from the ground up so do the bottom extra well, you only get one shot at that.
|
|
JD0
Member
|
# Posted: 10 Jan 2025 09:55am
Reply
Quoting: Grizzlyman I would do 2x10 floor joists not 2x8- I’m guessing an 8’ joist span to middle beam and then cantilever over beam on sides?
2x10 would definitely be preferred. The difference in price between 2x8 and 2x10 is not much in 8' material, but really jumps in 10' lengths. When I shop for materials closer to building I will try to find some reasonable prices for 2x10s and do that if I can. I hadn't thought about doing a cantilever, that would cut down on waste and cost if I only have to get half as many 10' boards.
Quoting: Grizzlyman I wouldn’t do a 6/12 roof if you build the loft that way as you you won’t have any head room in the loft. 8/12 with steel roofing will be not walkable- so the install wil not be fun.
I agree, 6/12 would make it uncomfortable in the loft. I haven't installed metal above 4/12 or really even walked on anything above 6/12 so 8/12 does make me a little nervous but that's the reason for the simple roof- so I can get that part over with asap!
|
|
JD0
Member
|
# Posted: 10 Jan 2025 10:00am
Reply
Quoting: paulz After a dozen years my place still ‘looks’ square but the front door is starting to get a bit sticky.
That's pretty much been my experience with blocks- sticky doors and windows after a while. What size is your cabin and what type of soil and weather do you have?
And yes, don't have to worry about braches or trees falling on it! There are some trees in the area so I will probably try to plant some along one or two property lines for some privacy in the future, but I'm guessing nothing will grow there if it hasn't already.
|
|
JD0
Member
|
# Posted: 10 Jan 2025 10:50am
Reply
Quoting: gcrank1 I did the 'gravel and cement silo staves (used)' floating foundation. I suggest you do the site prep asap so the disturbed ground beneath will get compacted, do a layer of 4" crushed rock topped with another layer of 'crusher run' then blocks. I really like the silo staves though they go 80# apiece!. Use as many as you can.
Great idea! A marketplace search shows an abundance silo staves for basically free, at least around where I live. Might be harder to find out near where I'm building but I'll keep an eye out. My plan is to go out and do site prep within a month or two (especially if I don't have to dig much), then let that settle for a few months and do the rest of the building when the weather is nicer. I live on the other side of the country so it's a little bit of a hassle to get there, but the plan is to get it dried in during a single 2 or 3 week trip, then take my time finishing the interior
|
|
paulz
Member
|
# Posted: 10 Jan 2025 01:11pm - Edited by: paulz
Reply
Quoting: JD0 What size is your cabin and what type of soil and weather do you have?
My place is smaller, 12x24 plus an add on 8’ bathroom. Hard dirt/rock soil, no clay. It’s on a steep hillside so lots of excavating on the high side and a little fill on the low side. Two big beams on blocks, you’ll need more I guess for a wider footprint but I’m no builder, others here are.
|
|
gcrank1
Member
|
# Posted: 10 Jan 2025 02:35pm
Reply
Keep yer eye on that crooked block  Btw, I was able to do all my rough ground prep with my little JD 1025r and bucket then all the gravel driving back & forth for compaction every time I had a full bucket. I leveled the top, then the blocks with a laser level, waayyy quicker than a line level. Those blocks must be the same height and level X/Y. On my 28' runs I have the blocks about 5" apart, that is 18 total/9 per side. I see way too many floating foundations with too few and too far apart. The more you have the more 'floatation' you get from the big footprint, ie, each has less ground pressure. And always get extra blocks/more than what you think you will use; you may have a few break and they come in handy for a bunch of things.
|
|
JD0
Member
|
# Posted: 10 Jan 2025 03:44pm
Reply
Thank you both for the insight. I'm still open to hear if anyone has concerns- I want to make sure I do it right, but it sounds like blocks are the way to go. Whether I do regular blocks, silo staves, or something else, I was planning on doing 15 total - 3 rows of 5. So maybe I'll add a few more around the perimeter. I hear ya on getting more than needed, that seems to apply to everything in building- especially when your closest hardware store is over an hour away.
This is my basic idea for a floorplan. The half on the left would be lofted and the living area would be open to the ridge. I'm not married to any of this - would love to hear if anyone has ideas. Like I said, I won't be doing anything on the interior for a while but I do need to get my windows and doors placed correctly.
|
|
JD0
Member
|
# Posted: 10 Jan 2025 03:47pm - Edited by: JD0
Reply
Not sure if that attachment worked...trying again.
|
|
ICC
Member
|
# Posted: 10 Jan 2025 09:56pm
Reply
Roofing: What is the snow load for the location of the cabin? That can affect the rafter size needed. The PSF can vary a lot across WY.
ASCE has an online tool that can be helpful with snow & rain loads, winds and so on. I may be able to assist if you have troubles with it. The risk category must be set for it to use. Level II is what we use for single family dwellings. Set the location by address, la titude & longitude or by clicking on the map.
In snow country, if I want snow to slide off a roof I prefer metal roofing over shingles. A pitch of 4/12 can hold a lot of snow before it slides. We can easily have a foot stack up before it begins to slide. A 6/12 will likely have the snow slide off faster and a higher pitch is more prone to very rapid shedding… like you walk out and slam the door. Boom.
Speaking of doors, the floor plan has the door in a side wall. How do you plan to avoid snow falling on people at the door? Or is that not a concern as the plan does not include winter use? The easiest solution may be to place the door in the right end, near a corner the door can swing up against and not take up interior space.
Floor Plan: The bathroom seems a little to me (for a cabin). A full bathroom can be 8 x 5 though that can be considered a tad small.
I’d be trying to make the center load bearing wall be more down the centerline so it would actually be over the center floor beam and be able to carry the loads straight down to the earth.
I see you are set on using blocks sitting on the ground so I will not bother to address the foundation, other than to say I believe that a large cabin should have a proper foundation. One never knows what life changes may occur and one could end up spending more time there than one thinks.
I believe two doors would be advised from a safety standpoint. One at the front (right) end and another instead of the window at the desk.
Anyplace to hang coats, jackets and place your boots when you come I the door?
Moving the entry door to the end would allow the table to be closer to the kitchen area.
Questions: What sort of heating? I see nothing in the floor plan.
Water; a well? Septic? If you can move the kitchen sink to the center wall at the bathroom you should be able to simplify the plumbing and keep all pipes out of the exterior wall framing.
Power from the grid?
Regarding T1-11 siding panels. Those are often non-structural panels. If it is structural rated there will be an APA stamo on the backside of each. See images below for examples. And I believe that GP states that its T1-11 panels should not be installed in the manner you mentioned for the roof.
You may find the AWC span calculator handy for joist and rafter sizing while you plan.
There are apps available for smartphones. I find it very handy to have. FYI AWC does have a tutorial online as well. That can help figure out what to set things like the deflection limits when making calcs.
|
|
ICC
Member
|
# Posted: 10 Jan 2025 10:00pm
Reply
APA grade stamps reference
https://solutions.dunnlumber.com/projects/how-to-read-a-plywood-grade-stamp
|
|
gcrank1
Member
|
# Posted: 10 Jan 2025 10:56pm - Edited by: gcrank1
Reply
Fwiw, we specified door at the corner (peak end overhang 4') with interior jam 12ish" from wall. From past experience that gives us a good coat hook area and room for the broom, etc. I was surprised how much I had to think about which side corner to put it in. Details, details.....
|
|
ICC
Member
|
# Posted: 10 Jan 2025 11:07pm
Reply

|
|
Brettny
Member
|
# Posted: 11 Jan 2025 05:54am
Reply
Quoting: ICC Regarding T1-11 siding panels. Those are often non-structural panels. If it is structural rated there will be an APA stamo on the backside of each. See images below for examples. And I believe that GP states that its T1-11 panels should not be installed in the manner you mentioned for the roof I believe it was you who told me about a Simpson strap that was prety cheap and would help with racking it was something like a 2in metal strap with nailing holes in it. If the OP wanted something more structual than t1-11 for siding they could use this.
How ever I would not use T1-11 (even the 5/8) for roof sheething. Its prety thin in the groves. They also make that LP smart siding stuff that's about 3/8 thick, I wouldnt even use that as siding unless theres sheething behind it.
|
|
ICC
Member
|
# Posted: 11 Jan 2025 08:51am
Reply
Yes to the Simpson wall bracing straps.
That helps but the framing and using osb wall sheathing panels make walls that resist high winds better than almost anything else.
The LP thin stuff looks great, for dog houses, maybe a privy
|
|
JD0
Member
|
# Posted: 11 Jan 2025 08:59am
Reply
Quoting: ICC What is the snow load for the location of the cabin? That can affect the rafter size needed. The PSF can vary a lot across WY.
That's a fantastic tool, I didn't realize such a thing existed to get an accurate location for snow load. I was estimating based on general show load charts and annual snowfall averages for the area. This shows my snow load will be 88lb/ft, can't do that with a 2x6 even going 12"oc. So 2x8 it is, if I want to stick with a 9ft span.
I don't think there was a specific reason I put the door in the middle, I was planning on doing a covered porch addition eventually but it does seem to be less intrusive on the side (and can still do the porch). I changed the drawing a little based on that and moving the center wall in a little. That makes the bed/bath a little smaller and kitchen a little bigger. However, if I do 8' floor spans and cantilever one side out (like grizzlyman suggested) my original floor plan would put the wall right over the center beam. Still need to look into that, though. It'll be a wood stove for heat, I noted that as a block next to my ladder to the loft. I switched it with the bath door so it's on the corner now. Probably a propane heater to supplement.
Off grid for now, but there is power close (within a half mile) so I might look into connecting it to the grid in the future. If it's going to cost anything more than a nominal fee I'll stick with a generator. Hauling in water, possibly collecting rainwater. No septic, more than likely just a composting toilet. Not a bad idea regarding keeping plumbing on interior walls.
Quoting: ICC I see you are set on using blocks sitting on the ground... Not totally set on it, in fact I came here half expecting my idea of using blocks to get shot down pretty quick. I appreciate the counter point and I'm still exploring my options. If I can find a practical/cost effective way to get equipment in and auger the holes required for piers, I will probably do that.
Quoting: ICC Regarding T1-11 siding panels. Those are often non-structural panels. If Right, I have always used sheathing under t1-11 in the past. I had only recently come across the idea of using it as sheathing, and I understand it has to be rated for it. I haven't looked hard enough to find a product that actually does what I'm looking for, maybe it doesn't exist or might just cost less to do sheathing anyway. Also considering doing sheathing and hardie panels or planks. That stuff seems to be a pretty decent value for something that will probably last longer than t1-11.
|
|
paulz
Member
|
# Posted: 11 Jan 2025 11:03am - Edited by: paulz
Reply
Quoting: JD0 Quoting: ICC I see you are set on using blocks sitting on the ground...
If I had it to do over again would I dig and pour? Probably, not that today it would improve anything. At that point I thought ‘I’ll just build a fort!’. Little did I know I’d be pretty much living in it a dozen years later.
Flooding rains haven’t bothered it. We do have earthquakes, with a good enough one probably wouldn’t matter.. No freezing. Point is think ahead, which you obviously are doing. Good on you.
|
|
ICC
Member
|
# Posted: 11 Jan 2025 11:52am
Reply
Quoting: paulz At that point I thought ‘I’ll just build a fort!’. Little did I know I’d be pretty much living in it a dozen years later.
Yes! That is why I believe in building better, if not best, and not simply something that "will do" because "it's just a cabin".
You never know what curves life will throw at you or how your interests may change over time.
|
|
gcrank1
Member
|
# Posted: 11 Jan 2025 01:22pm
Reply
Our first build was '83-'84, on silo blocks on a sand and gravel hill in my dad's woods 1/4mi from the farm. I didn't prep the ground other than level out the spots for the too few blocks (never thought Id build it as big as it became and total structure weight adds up quick). Even so, that cabin, in the 35ish years there, only needed shimming at the centrally located door once because it got sticky. Better prep and more blocks would have probably solved that. We have several past threads about running grid in, at that kind of distance I expect it would be 10s of thousands of dollars.
|
|
ICC
Member
|
# Posted: 11 Jan 2025 03:41pm
Reply
One other thing to think about regarding the use of T1-11. It comes in 4x8 sheets. When building on a platform floor (floor joists supported by beams with subfloor on top of the joists and the walls built on top of the subfloor) It makes for a much stronger building if the exterior sheathing panels not only cover the wall framing but also overlap the rim joist that is nailed over the ends of the floor joists. 4X8 sheets of osb and plywood are available to do this.
the image shows a mfg floor joist but the rim overlap can be seen.
|
|
ICC
Member
|
# Posted: 11 Jan 2025 03:47pm - Edited by: ICC
Reply
Quoting: JD0 Quoting: ICC I see you are set on using blocks sitting on the ground... Not totally set on it, in fact I came here half expecting my idea of using blocks to get shot down pretty quick. I appreciate the counter point and I'm still exploring my options.
Here’s some of my thoughts….
I have some sheds and utility buildings that sit on concrete blocks sitting on the ground. They are okay as sheds but I wouldn’t want to live in them. One of them shifts a little as the seasons change. However I built it with a gate like door that has a turnbuckle adjustment across the diagonal and I twist it one way or the other as needed.
The one thing I dislike most when it comes to maintenance, remodeling, rebuilding, is to have to crawl around on the ground underneath a building. That has lead me to a real dislike for structures that have one or more beams running down the middle.
20 years ago I built my present cabin. Two 30 foot long beams supported on piers every 7 feet. Beams are four layers of 2x10. Piers are rough cut foundation grade 6x6. The beam overhangs the end posts by about a foot. Floor joists are 16 foot 2x10, #2 hem-fir 16”OC that cantilever over the beams about 10”.
Note: It is allowed to cantilever floor joists over a beam by the same amount of the height of the joist. That is, a 2x10 joist can overhang the outside edge of the beam by 10”. That tucked the beam under the side which may keep it dryer if the crawl space is left open. Cantilevering also reduced the effective span down to 13’4”. It is a nice solid floor.
I used ¾” OSB T&G subfloor, ¼” hardi-backer board, ceramic tile flooring. No cracks anywhere after all this time. No movement. The piers go down to frost depth with holes belled out for a poured concrete footing and the soil is very gravelly; no clay.
Since building it I have learned more and realize I had a little luck in having well drained soil and no clay.
Since my build family members have built nearby. They have followed my lead with one exception. They wanted a wider cabin and went with helical piles installed by a contractor. They do have a center beam but there should be no movement with the engineered foundation. Plus they have a decent height crawl space.
I understand that some locations, especially those here in the west, are too great a distance out into the boonies over sometimes iffy roads for contractors to want to bother with. If you can find someone who will do helical piles for a price that suits you I’d give that some thought.
Maybe consider this, if you decide that a proper frost depth foundation is not practical for you to build. What if your design was changed to two beams? Eliminating the center beam would simplify any future need to adjust the beam to support block connection—no need to crawl under the building.
Two four-layer beams could be made using 2x10s. Note, if the bottom edge of the beam is greater than 12 inches above grade PT lumber is NOT required.
If we used 2x12 floor joists the joist could cantilever a nominal 12” over each beam. The built-up beam would measure 6 inches wide. With a cabin width of 18 feet (216”), we would subtract the cantilever and beam width; 216 - 12 - 12 - 6 - 6 = 180 inches or 15 feet actual span distance.
Doug Fir, 2x12 grade 2 lumber on 16” centers with the standard LiveLoad of 40 PSF and DeadLoad of 10 PSF can span up to 18’1” according to the AWC calculator, so there is ample margin. DF 2x10 calculates to a max span of 15’7”. Technically allowable but possibly too close to the maximum?
See what species of 2x12 the local suppliers carry. Hem-Fir is common here and has slightly less span than DF.
Of course, doing twin beams would also change the requirements for the loft floor and ceiling joists.
|
|
ICC
Member
|
# Posted: 11 Jan 2025 03:50pm
Reply
An alternative to digging deep holes or trenches for a frost depth foundation....
Shallow Frost Protected Foundation: Two different categories; heated building and non-heated building. Occasionally occupied and not heated during absences would be in the non-heated category.
Downloadable document
Those need quite a bit of excavating to lay the horizontal insulation sheets so may not be suitable for this project.
|
|
ICC
Member
|
# Posted: 11 Jan 2025 04:12pm - Edited by: ICC
Reply
One more ramble....
Back to piers and sonotubes for a moment. These require a steel reinforced concrete footing pad to spread the load out over more area. The deeper the frost depth the more difficult that gets.
Without tying the bottom end to a footing the per/sonotube is free to move in any direction from the top end down. It seems far fetched, but piers do move or tilt. Moisture can soften up the soil and a pier can rotate, swing or tilt in any direction. When a full perimeter foundation footing can be dug to frost depth and concrete poured the whole wall or series of pillars can be tied to the footer at the bottom and the beam at the top. Then shear walls can be created between pillars. Again, probably out of the question for this project.
One disadvantage of piers of any kind is that they are single units. One or two could shift. A full perimeter footing would help tie them all together. Movement of any one pier would be restrained by others. Too much excavation required?
And finally, Even if an area has no code enforcement, no inspections the building code is a good reference as to what techniques work well. That may be considered as mu opinion. If one looks it can be seen there are good engineering reasons behind the methods that have code approval. Code sizing, etc are minimums. The better quality homes and cabins exceed what code lists.
Code also contains handy tables for such things as what size and how many nails are required to securely fasten the work. Example; as the snow loads go up, not only do the size of the rafters increase but the number of nails used increase. There's a table for that info.
Free online IRC access
Click on the Chapter links in the left sidebar
|
|
ICC
Member
|
# Posted: 11 Jan 2025 04:30pm - Edited by: ICC
Reply
Quoting: JD0 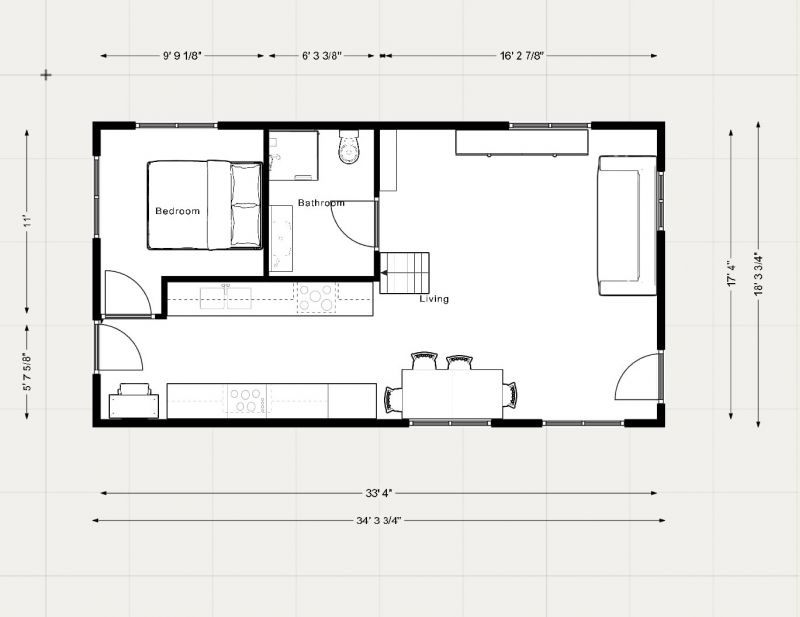
Perhaps change the swing of the bathroom door.
|
|
paulz
Member
|
# Posted: 11 Jan 2025 05:27pm
Reply
Quoting: ICC Yes! That is why I believe in building better, if not best, and not simply something that "will do" because "it's just a cabin".
Yes, again if I had known… When I bought this place, I don’t really remember why now, a friend was selling it, I already owned my house outright, had no interest in building on it nor experience. Money was just burning a hole in my pocket I guess. Already owned an RV, was great to camp here in that at first.
Is there a build thread on your cabin Izzy? If so I don’t remember it now. Memory’s shot..
|
|
ICC
Member
|
# Posted: 11 Jan 2025 05:40pm
Reply
Quoting: paulz Is there a build thread on your cabin Izzy?
No, it was already built before I got here.
We had an old RV trailer we first took up to the property years ago. About 1995 or so. It was great for a few years then we wanted more space, a better shower.
|
|
. 1 . 2 . >> |