. 1 . 2 . >> |
Author |
Message |
241comp
Member
|
# Posted: 9 Nov 2011 12:41am
Reply
Here it is, fall, and I'm finally getting started on the cabin.
Got the driveway in: 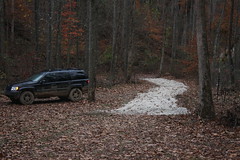 IMG_6410 by 241comp, on Flickr
Just starting on the posts. The posts are 6x6 and are set in 48" holes with a poured concrete footer and back-filled with crushed gravel. 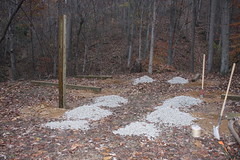 IMG_6412 by 241comp, on Flickr
Posts going up: 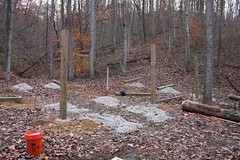 IMG_6422 by 241comp, on Flickr
Had to take down a small tree that was going to be in the way: 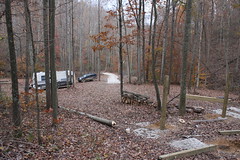 IMG_6426 by 241comp, on Flickr
Unfortunately, the local lumber yard only had two lengths of 6x6 posts available, so some are way too long. Fortunately, there will be plenty of opportunity to use the leftovers. 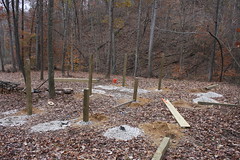 IMG_6432 by 241comp, on Flickr
|
|
MtnDon
Member
|
# Posted: 9 Nov 2011 12:54am
Reply
Good feeling to get started isn't it?
What is the size?
|
|
turkeyhunter
Member
|
# Posted: 9 Nov 2011 05:58am
Reply
looks like you are off to a good start, keep the progress and pic's headed this way!!!!!
|
|
241comp
Member
|
# Posted: 9 Nov 2011 07:40am
Reply
MtnDon, yes, it feels good to get started. The overall size will be 24x30, with a 16x30 gambrel-roof cabin and an 8x30 front porch, facing down the slope.
turkeyhunter, will do. Hopefully I will be installing beams, joists and possibly flooring this coming weekend. Yay.
|
|
241comp
Member
|
# Posted: 9 Nov 2011 07:53am
Reply
Here's a good shot of what it looked like when I finished putting all 9 posts in: 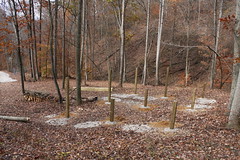 IMG_6438 by 241comp, on Flickr
And here's the eventual view from the cabin (minus the camper, which will go once the cabin is finished): 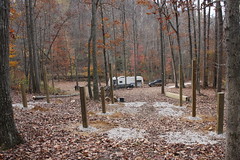 IMG_6440 by 241comp, on Flickr
|
|
MtnDon
Member
|
# Posted: 9 Nov 2011 09:59am - Edited by: MtnDon
Reply
16 wide x 30 long. I'm wondering what size of beams you are planning on using. IMO, that is a mighty distance between piers. That is a Big stretch. . Single floor? Loft? Have a drawing?
|
|
MtnDon
Member
|
# Posted: 9 Nov 2011 10:14am - Edited by: MtnDon
Reply
And I mean that in a very friendly manner. It is meant to be helpful as it is an unusually long span between piers.
The concern of mine is the beam span and the loading on the piers. The center pier in each long side will be bearing more than one third of the load on each long side, probably something more like close to one half the sidewall load.
|
|
241comp
Member
|
# Posted: 9 Nov 2011 11:04am
Reply
I appreciate the friendly inquiries. It will be single floor (probably add a partial loft, eventually).
I'm using 3-layer 2x12 for my beams (~13ft span, small overhang) and 16"oc 2x10 for joists (~10ft span, small overhang). By my calculations, this passes fiberstress, sheer and deflection.
The piers are 6x6 and the tallest will have a maximum "unbraced" height of about 60", down to about 12" at the shortest pier. By my calculation, my "worst" pier would have a max compression load of about 27,000lbs.
I welcome any feedback on these calculations.
|
|
cabinbasics
Member
|
# Posted: 9 Nov 2011 11:30am
Reply
Pretty spot 241, where you located?
|
|
MtnDon
Member
|
# Posted: 9 Nov 2011 11:32am
Reply
27000 pounds load on one pier. How big is the footer? 16x16 is more or less usual; that's 1.777 sq ft. 27000 / 1.777 = 15000 pounds per square foot. Most soils run between 2000 and 5000 psf.
Thst's what I see; could be wrong.
Never looked at the beam yet.
|
|
241comp
Member
|
# Posted: 9 Nov 2011 11:38am - Edited by: 241comp
Reply
cabinbasics, near Vanceburg, if you're familiar with where that is. I guess I could post a few pictures of my property as well as the cabin construction.
Perfect tree to build a tree-house for the kids (probably free-standing or attached to the tree for lateral support, not hanging from the branches): 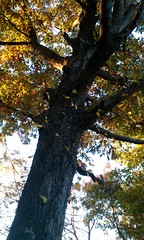 Nice tree I found that could support a tree-house? by 241comp, on Flickr
The view of "my side of the mountain" from the cabin valley: 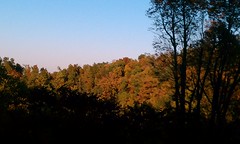 View from the valley looking my ridge by 241comp, on Flickr
View from the ridgeline, overlooking the valley: 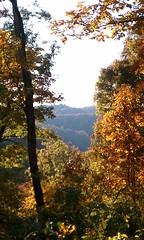 View from the ridge, overlooking my front valley by 241comp, on Flickr
|
|
241comp
Member
|
# Posted: 9 Nov 2011 11:50am - Edited by: 241comp
Reply
MtnDon, you're right, the 27,000lbs rating was for the post itself, not the entire pier as I mistakenly stated. I would say the footer is probably about the size you mentioned.
I calculated about 34,000lbs total weight (50lb/sf cabin load, 40lb/sf porch load). I figured that's probably generous considering this is a pretty basic cabin, not a full residence. Assuming I have even weight distribution on my piers, that's about 3800lb/post. I realize it won't be evenly distributed, but I have no idea how to calculate the exact distribution. Do you think I should be concerned about my posts tending to sink? The soil is extremely rocky - not sure if that affects the weight-bearing capacity of the soil much.
|
|
smitty
Member
|
# Posted: 9 Nov 2011 12:45pm
Reply
Cool! Will be watching your progress. Off to a good start!
|
|
MtnDon
Member
|
# Posted: 9 Nov 2011 01:20pm
Reply
When we look at the side row of piers the two at the ends will usually be the lightest loaded piers along that wall. In a row of piers like on our 16x30 (row of 5) the next pier in from the end will be the heaviest loaded pier in that row; that goes for both ends. Then the pier in the middle will have a load somewhat less than those. With only one pier in the middle of the run the center one will be taking the most load. So yes, I believe 2 extra piers per outside wall would be advised.
A very rough idea of what might be happening can be seen from drawing a rectangle to represent the 16x30. Draw in the piers. Draw a line across the 16 dimension half way between the pier sets. That's a very rough, totally unscientific representation of the load distribution. Most of the roof comes down on the side walls. Wind forces against the long side and roof pitch can cause one side to get "lighter" and the opposite side "heavier". Wind on the roof is also transmitted down through the gable end walls to the foundation. That can increase the load on the end pier on the leeward side. Calculating all that gets complicated.
In most cases there is no worry about the ability of the pier to safely accept the vertical load. The concerns come mainly from beam span, soil load bearing capacity and lateral support. Most pier and beam foundations come up a bit deficient in lateral support, IMO. A pier with 60 inches above grade is actually a somewhat scary thought, to me.
Soil bearing capacity can vary widely within a few miles in some places. Others have a widely distributed more or homogenous nature. There is a website that might help. Web Soil Survey uses USDA data. Have a look at it, it might have data on your area. Our mountains is one of the areas where conditions vary too much for this tool to be of any help.
With rock it depends what other substances there are between the rocks. I'm not a soils engineer or a geotech, though.
The floor joist specs look great. The three layer 2x12 beam looks to be overextended to me, depending on potential snow load and what loads come from the loft, if any. But I'm not calculating numbers, I'm using tables. A single story structure with a center beam down the floor indicates girder (beam) choices for 30 psf snow and is calculated on 40 psf Live Load. The LL in a cabin could be downrated to 30 psf as they don't usually have as much heavy equipment in them. The other factor from the chart that doesn't jibe 100% is the minimum building width starts at 20 feet, 4 feet wider than yours. But I look at that as a safety factor. I never like to use the maximum spans that tables or calculations indicate to be within the design limits. But that's just me.
A 3-2x12 beam of DF, hem-fir, SYP, S-P-F have a suggested maximum span of 10'2". With extra intermediate piers the beam could be built from 3-2x8 and be more than adequate.
As for the tall piers I have some ideas on best methods of bracing them. If you'd like to hear about them, please ask. I worried about that for our cabin as we are in a moderate seismic zone as well as being exposed to some good winds. Our area is rated for up to 90 mph wind bursts. Since 2007 we've recorded a couple in the 55 to 58 mph range.
|
|
241comp
Member
|
# Posted: 9 Nov 2011 01:42pm - Edited by: 241comp
Reply
MtnDon, thanks for all the useful info. I'd definitely be interested in hearing your thoughts on bracing.
My current plan is basically an X of through-bolted 2x6's from each post to the one(s) next to it. Members of the X being on opposite sides of the posts, and a block where the braces cross allowing them to be tied together to prevent bowing. Actually, a lot like the "Step 3" picture on this page: http://outdoor-living.hardwarestore.com/learning/a-guide-to-building-a-deck.aspx
|
|
MtnDon
Member
|
# Posted: 9 Nov 2011 04:06pm
Reply
A solid X as described is good. 2x8's would be better. Also better would be to add some 16D nails (hot dipped galvanized if in PT wood) to each 2x to pier connection. The through bolts with large diameter washers will keep the 2x tight to the pier. The 16D nails will help spread the stress around. That can help prevent formation of splits.
Constructing what an engineer would call a shear wall between the piers is probably the best, most rigid, solution to piers that are tall. This would be framing a wall between two piers with dimensional lumber, bottom plate with vertical studs every 24 inches or less. On the long side this would be sheathed with 3/4" exterior grade (PT if any is close to the ground) plywood. The plywood would be nailed every 3 to 4 inches with 6 or 8D nails... ring shank or spiral are best. Plywood on the outside face with the upper portion of the plywood lapped over the beams and the ends lapped over the piers. Nailed securely same as to the 2x framing lumber.
In the direction across the cabin width it is a little trickier. It is in the lateral direction, across the width, that is most often the less well braced. Here it would be best if the floor joists above could be positioned to have one vertical side face align with the face of the piers. That way the plywood could be lapped over the joist and the post and nailed in well. There would also be 2x framing across between the piers to nail the plywood panels to.
This would stiffen the pier to beam to joist connection much better than any diagonal bracing ever can. The piers would be braced by the shear wall and not have to reply on the ability of the ground to withstand the lateral forces on the piers. I have seen piers about 36 inches tall lean out of plumb by a very visible amount when the ground got wetter than usual.
Come spring I have such a shear wall retrofit planned as an insurance against the vagaries that mother nature can and does throw at us.
|
|
trollbridge
Member
|
# Posted: 9 Nov 2011 09:50pm
Reply
Welcome and congratulations on getting started! Your land looks beautiful and it will be fun watching your cabin come along!
|
|
hattie
Member
|
# Posted: 10 Nov 2011 07:34pm
Reply
Beautiful location. That tree does seem to be screaming for a tree house doesn't it? *S*
|
|
241comp
Member
|
# Posted: 16 Nov 2011 03:06pm
Reply
This past weekend was productive and a lot of fun (except for the rain).
Staging the beam lumber 
Posts cut to proper height 
First beam going up 
Two beams up 
Three beams up 
Lumber staged and ready for construction 
Lateral support (pictures don't show it, but lateral support was added in the other direction as well) 
Lateral support detail 
Setting joists 
Joists complete 
Joist and blocking detail 
Starting the flooring 
Cabin floor ~1/3 complete (and porch deck barely started) at quittin time 
|
|
jrbarnard
Member
|
# Posted: 17 Nov 2011 10:14am
Reply
I am curious. The reason I elected to take a week off from work and gather a lot of guys to help build the cabin next spring is because I did not want the wood to be exposed to the weather.
Does building it in the weather you are building in hurt the wood? I would think that mold or rot might set in with it getting all wet etc.. (?) I have no idea on that aspect, just curious.
I would start building the base of mine if I thought I could leave it out in the open for a month or more.. heh
Russ
|
|
241comp
Member
|
# Posted: 17 Nov 2011 10:28am
Reply
I'm honestly not sure how the weather will affect the non-treated pine tongue & groove flooring, but I'm hoping to have it "in the dry" by December 1, so the amount of time that it will actually be exposed is just a few weeks. The rest of my structure is pressure treated for either ground contact or above-ground exterior use, so it is designed to be exposed to the weather. I imagine that if I left the untreated pine out all winter, I would have some significant weathering to deal with, though a floor sander would probably take care of most of it.
|
|
Montanan
Member
|
# Posted: 17 Nov 2011 11:18am
Reply
We had the same issue last spring, as our shell was delivered a number of weeks before we were able to get out there and start putting the roof on. It rained and rained and rained the whole month (serious flooding in nearby areas.) We were pleasantly surprised at how well the wood held up. With the exception of some chinking that needs to be redone, the damage was minimal. That being said, we had the summer sun that came out and quickly dried the wet wood and we are in an arid climate. By the time we starting putting tar paper on the wood roof panels, everything was bone dry.
|
|
oldbuddy
|
# Posted: 25 Nov 2011 10:19pm
Reply
I like the sounds of your build. If it goes anything like ours did, progress will come to a slow halt in the near future due to the weather in our area of the country which I'm sure is very similar to yours. It is a great experience and has allowed my son and I (he's 37) to spend a great deal of time doing something he and his family as well as my daughter's family and my wife can enjoy, for years to come. Good luck with yours. After reading all the technical info on the load bearing weight/etc., I'm hoping mine is fine. I guess I never gave it a thought....considering everyone tells me I "overbuild" everything. If it isn't, I'll just have to pull some big tree underneath it to support it...should it ever start sagging.
Old Old Buddy
|
|
241comp
Member
|
# Posted: 10 Dec 2011 11:19am
Reply
We had an Amish crew come down and construct the shell of the cabin yesterday. Below are some pictures of the process.
Finishing the floor: 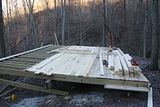
First wall ready to be raised into place: 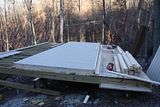
First wall up: 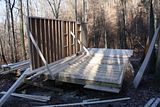
Second wall up: 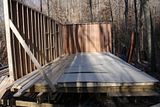
Four walls up: 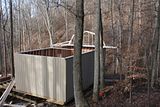
Starting the roof: 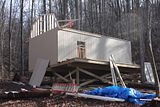
Porch construction: 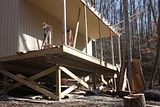
Sheathed and preparing for metal roofing: 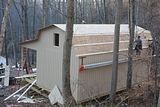
Working on the roof: 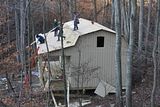
Installing metal roofing: 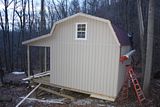
Interior: 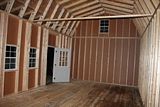
Unfortunately, I don't have a photo of the final result as they finished up well after dark. That's all for now - hopefully I'll have some interior construction updates over the winter. But at least, the floor is now covered and I no longer have to worry about it weathering. Final weight for all construction material is just shy of 15,000lbs so I think the foundation should be plenty strong enough for anything additional I do in the interior.
|
|
hattie
Member
|
# Posted: 10 Dec 2011 02:50pm
Reply
This looks fabulous!! Can't wait to see the final photos and the inside when it is all completed.
|
|
turkeyhunter
Member
|
# Posted: 10 Dec 2011 08:10pm
Reply
great job..............looks likes a fine cabin spot.
|
|
Bevis
Member
|
# Posted: 10 Dec 2011 08:16pm
Reply
Looks good...that is the idea I've had in my head as my hunting cabin. I'll be watching this one.
|
|
241comp
Member
|
# Posted: 16 Jan 2012 05:30pm
Reply
So, I made it back down to Kentucky this weekend and was able to finish the porch and add a temporary railing and steps.
Laying the porch decking: 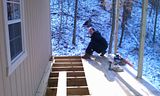
The porch: 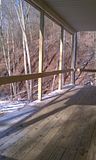 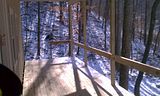
Cabin in the winter: 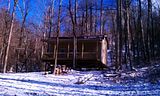
A view of the porch and steps: 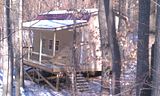
|
|
241comp
Member
|
# Posted: 17 Jan 2012 11:17am
Reply
Here's a panoramic view of the cabin:
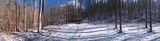
And one from the cabin porch: 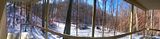
|
|
exsailor
Member
|
# Posted: 17 Jan 2012 01:01pm
Reply
I see you used a metal roof on a gambrel design. I am thinking that style roof on my future cabin. I want to use a metal roof so I can collect water from the roof. I have learned asphalt shingles taint the water and the petroleum run off makes it unsafe for human consumption. One thing I couldn't figure out was how to weather proof the angle change in the roof. It doesn't look like you use corrugated tin as a roofing material. What was your metal roof covering and how did they weather seal the roof angle change? Thanks for helping to solve a future problem and the enlightenment.
|
|
. 1 . 2 . >> |